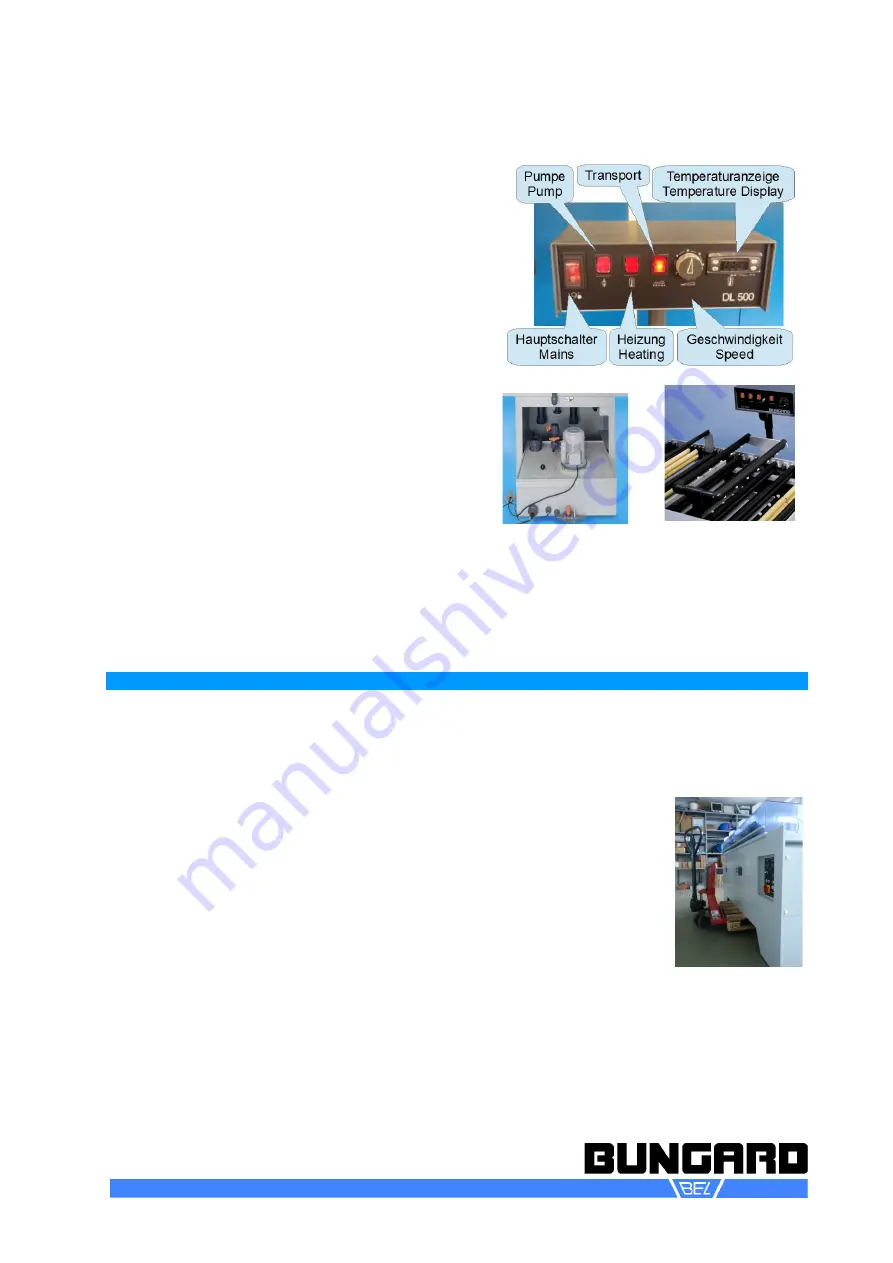
DL500-Manuel-E
Page 8 / 20
The machine body is made from PVC. It is divided into
infeed-, etching-, rinsing- and outfeed-zone. The remov-
able media tank is located in the pedestal of the ma-
chine.
The cover is made from grey and transparent PVC. It
carries housings to fix the removable partition walls.
The media tank is easy to access and can be entirely re-
moved from the machine. The top cover of the tank car-
ries the pump. This is a submersion centrifugal pump
which propels with highpressure the etching medium to
the 4 manifolds, each of them equipped with 14 flat
spray nozzles. The liquid returns to the tank via 2 PVC
drain pipes of big diameter. The tank carries a 1000 W
heater element and the temperature sensor.
The conveyor system is made from 13 pairs of PVC
covered rollers and of one infeed and outfeed roller at
each end of the machine. The squeegee rollers are
covered with a sponge cloth each. Using an endless
belt, the rollers are directly coupled to a gear motor.
The water access to the rinsing compartment is con-
trolled by both a magnetic and a manual operated valve.
The magnetic valve opens only when the etching pump
is operating. A circuit rinse or a downstream rinsing wa-
ter treatment are as an option available.
The control unit is mounted on top of the machine. To permit easy access from each side of the machine,
it can be turned into almost any position. The front panel carries illuminated switches for the main supply,
pump, conveyor and heating circuits as well as a potentiometer for conveyor speed adjustment and the di-
gital-reed-out thermostat.
Setup
Take over from the transport agent
After receiving and unpacking, check the machine for possible transport damages. In case of trans -
port damage, please inform your insurance, the transport company and the manufacturer / supplier.
Transport to the place of installation
Only use suitable lifting and transport equipment such as forklifts or pallet lifts.
Secure the machine against sliding / tilting.
The machine is fixed to the transport container or to the palette by plastic tapes.
Remove all packing material and tapes from the cover, the control unit and the me-
dium tank.
To avoid damage, do not move the machine on the ground. With the help of at
least one other person, carry it to the desired location. The best possibility to
handle the machine is to hold it at the left and right side walls on each end.
Place of installation
The location must fit the labour protection requirements for etching machines, i. e.
ventilation, sealed floor etc. It must further offer power and water installation close-by.
The place must be straight and even. It must carry the entire bottom of the machine (no palettes!). With
respect to an easy feeding and a good access also to the back side of the machine, there should be a free
area of about 2m x 2m.
Bungard Elektronik GmbH & Co. KG, Rilkestraße 1, 51570 Windeck – Germany
Tel.: +49 (0) 2292/5036, Fax: +49 (0) 2292/6175, E-mail: [email protected]