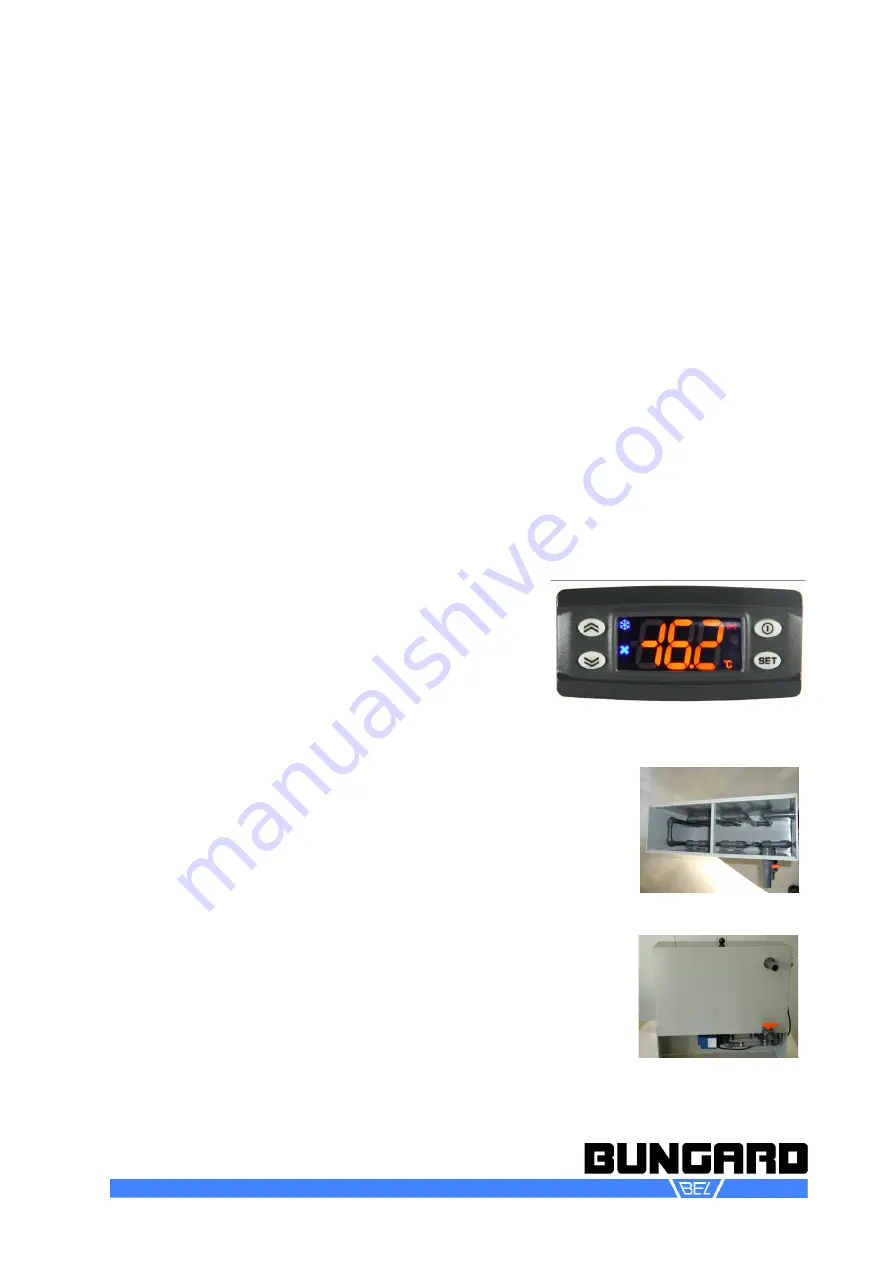
DL500-Manuel-E
Page 11 / 20
The tank capacity is about 55 litres. The correct filling level is about 1 cm below the tank cover plate. A too
little filling level will cause the pump to suck air, which can be heard as a specific sound.
If the filling level should be lower than the pump inlet level, the heater element could run free. This would
most certainly lead to a damage to the machine. It is though necessary to control the level periodically. To
fill up, switch the pump off and add water or etching medium until the liquid level is 1 cm below the tank
cover.
Conveyor
The boards to be etched are inserted into the machine at it's right end, seen from the front. Boards are put
onto the first roller and carefully moved forward until they are attached by the next roller pair. It may be ne-
cessary to support very long boards manually until they have completely entered the machine.
If you did not install a trap table at the machine's left end, you must take off the etched boards from the
machine manually. Otherwise they might fall down and get damaged. We offer inlet and outlet tables as
an option.
Speed can be varied using the button right to the conveyor switch. At a reading of 1 on the button scale,
the conveyor will run at it's minimum speed. Actual speed setting depends on temperature, saturation and
type of the etching medium as well as on copper thickness and spray pressure. For fresh warm ferric
chloride at about 45°C, a speed setting of about 3 will do.
It might be a good idea to keep a once found setting for 35µm also if boards with 70µm copper are
etched: Just have the board pass the machine twice.
The speed adjustment is at it's optimum if there are only very few rests of copper remaining on the board
at the moment that it reaches the last roller pair in the etching compartment. A board which was incom -
pletely etched may be processed again at a high speed setting. A too little speed will cause severe under-
cut.
Heater
Important: The heater circuit may only be activated with the
tank filled!
The control switch being lit, the heater circuit is enabled. The
switch relates to the thermostat located on the right. The
thermostat first makes a self test and after some seconds
the present temperature of the etching liquid is shown.
The temperature of the thermostat is preset to 45°C. You
should only changes this value, if your etching liquid
com-
pellingly
requires another temperature. You can change the
value by pressing 2 times the
SET
-key. With the arrow-keys
you can move up or down to the desired temperature. Press
SET
again. On
the display appears the word “Set” and above the display the orange “OUT”-
LED goes on. After some seconds the present temperature of the liquid is
shown again.
The temperature setting depends on the type of etching medium to be used.
For ferric chloride we suggest to set temperature to 45 °and for sodium per-
sulfate to 40°C. For copper chloride or sulfate based media, 30°C are recom-
mended. Ask your chemistry dealer for details.
Although the thermostat range is up to 60°C, a temperature setting of
more than 50°C is not permitted. Please note that certain etching media
produce heat when used. In this case, the temperature setting must be
reduced in advance. Do not feed the machine with boards until it has
cooled down. We supply a cooling tank as an option.
Rinse
The rinse compartment can either be used with fresh water or, with an op-
tional tank and pump, as a closed loop rinse.
Bungard Elektronik GmbH & Co. KG, Rilkestraße 1, 51570 Windeck – Germany
Tel.: +49 (0) 2292/5036, Fax: +49 (0) 2292/6175, E-mail: [email protected]
Cooler
Closed-Loop rinsing Unit