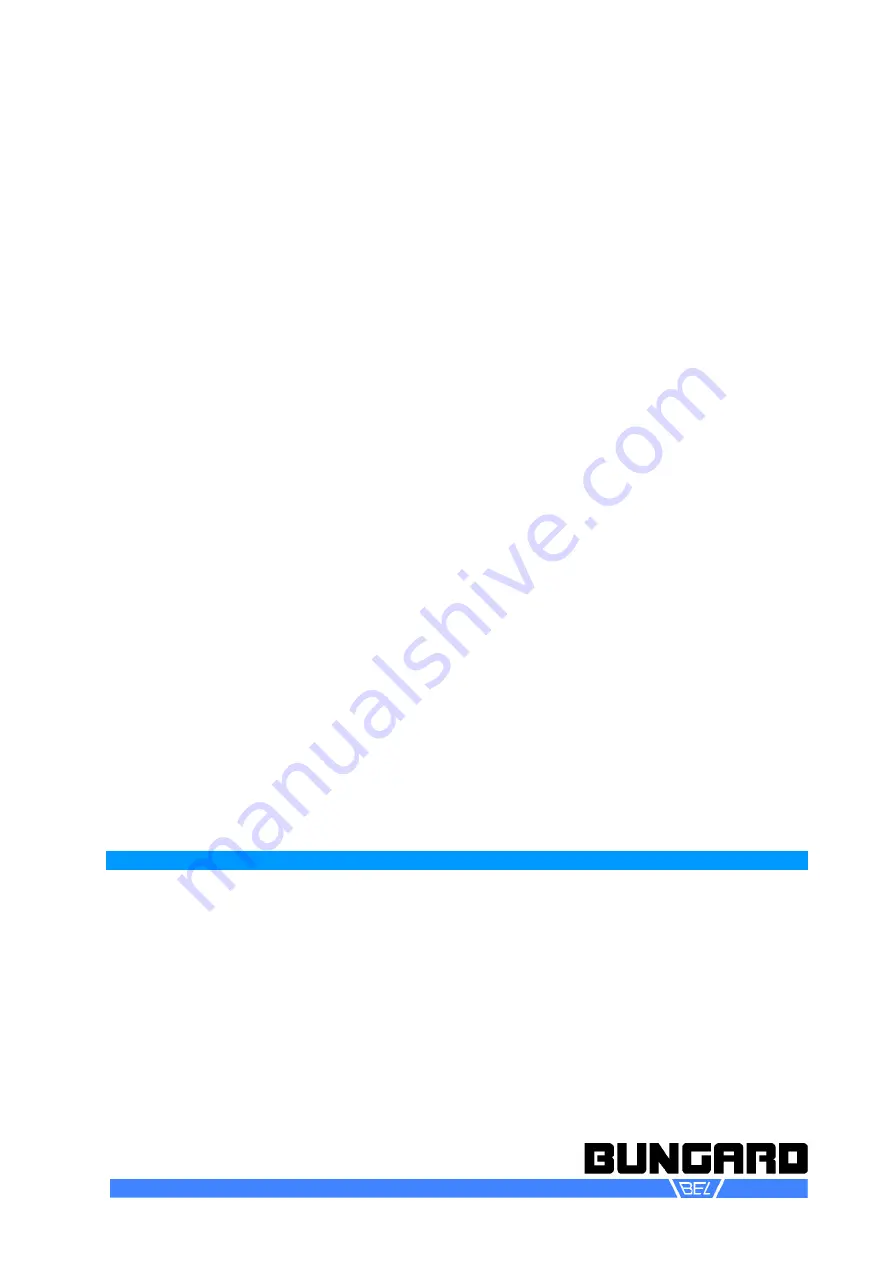
DL500-Manuel-E
Page 10 / 20
Rinse compartment
Check if there is sufficient, but not too much water. Pressure is good if the lower jets almost reach the
cover. See if the descent to the drain is sufficient. If not, the water floods the rinsing compartment and
exits into the etching zone. Adjustment of the water inlet is described in chapter
Cleaning and Mainten-
ance
.
Discharging
Empty now the machine completely and pull the power supply plug. In order to replace the filled in water
by etching agents, empty the medium container:
Fasten a short piece of hose to the ball valve of the medium container, the other end of the hose should
end in a plastic bucket. Open the ball valve and let the air escape from the hose. Hold the filled hose then
into the bucket. With this `principle of the communicating tubes you can empty the medium container so
far, that you can move the container from its position without spilling and then empty it completely. Do not
forget to loosen the fittings and the electrical connections before moving.
There is a ball valve at the bypass of the tubing leading upward. Opening this ball valve while the etching
pump is on will lead to exit of etchant. This is an unavoidable danger in case of any improper or unatten-
ded operations at the back of the machine. The you may encounter by the closing the ball valve, pull off
the handle and store the handle separately.
Alternatively: emptying the machine via the etching pump: The ascending tubes in which the etchant is
transported under pressure to the nozzle manifolds, has a bypass with a ball valve. At the spout of this ball
valve you can put on a piece of hose. The other end of the hose must end in an appropriate bucket. Turn
on the pump and carefully open the ball valve of the bypass. The water will be drained into the bucket.
This way you can empty the medium container down to 1/3 of the content. The remaining ater you can
drain via the ball valve at the bottom of the container.
The ball valve has a screw connection to the ascending tubes. Before starting the pump check this screw
connection on tightness and retighten if necessary by hand.
Fill with etching agent
The machine can be filled alternatively through the hand hole of the medium container or after removing
the hood, from above via the etching zone (in that case do not forget to firmly close the tube fittings).
Make sure before filling that the drain cock of the medium container is closed. This is the case, if the
handle stands perpendicularly to the sleeve. The correct filling level is about 1 cm under the cover of the
medium container with the pump switched off. A too small amount of filling can lead to damages and
must be avoided. After some operation refilling of etching agent can be necessary by the hand hole in the
cover of the medium container. After you filled in the finished and cooled down etching agent and the pos-
sibly dismounted parts are reassembled the machine is ready for use.
Trouble
If there were problems coming up during this first test, which are not described in this manual, please
contact us immediately.
Operating
Control Panel
All electric functions of the DL 500 are controlled from the front panel of this unit (compare
Composition
).
From the left to the right, there are: The switches for the main supply, for the pump motor, the heater and
the conveyor. Next is the button for speed control of the conveyor. All to the right, there is the thermostat
unit.
The main switch turns off all other switches and circuits. This permits an instant stop
Etching circuit
The second switch from the left being turned on and the cover being closed, the etching pump will start. It
propels the liquid to the nozzle-equipped manifolds. The flow capacity and the pressure can be set manu -
ally by a valve located in the liquid mounting pipe. The liquid returns to the tank via two fitting connected
PVC pipes.
Bungard Elektronik GmbH & Co. KG, Rilkestraße 1, 51570 Windeck – Germany
Tel.: +49 (0) 2292/5036, Fax: +49 (0) 2292/6175, E-mail: [email protected]