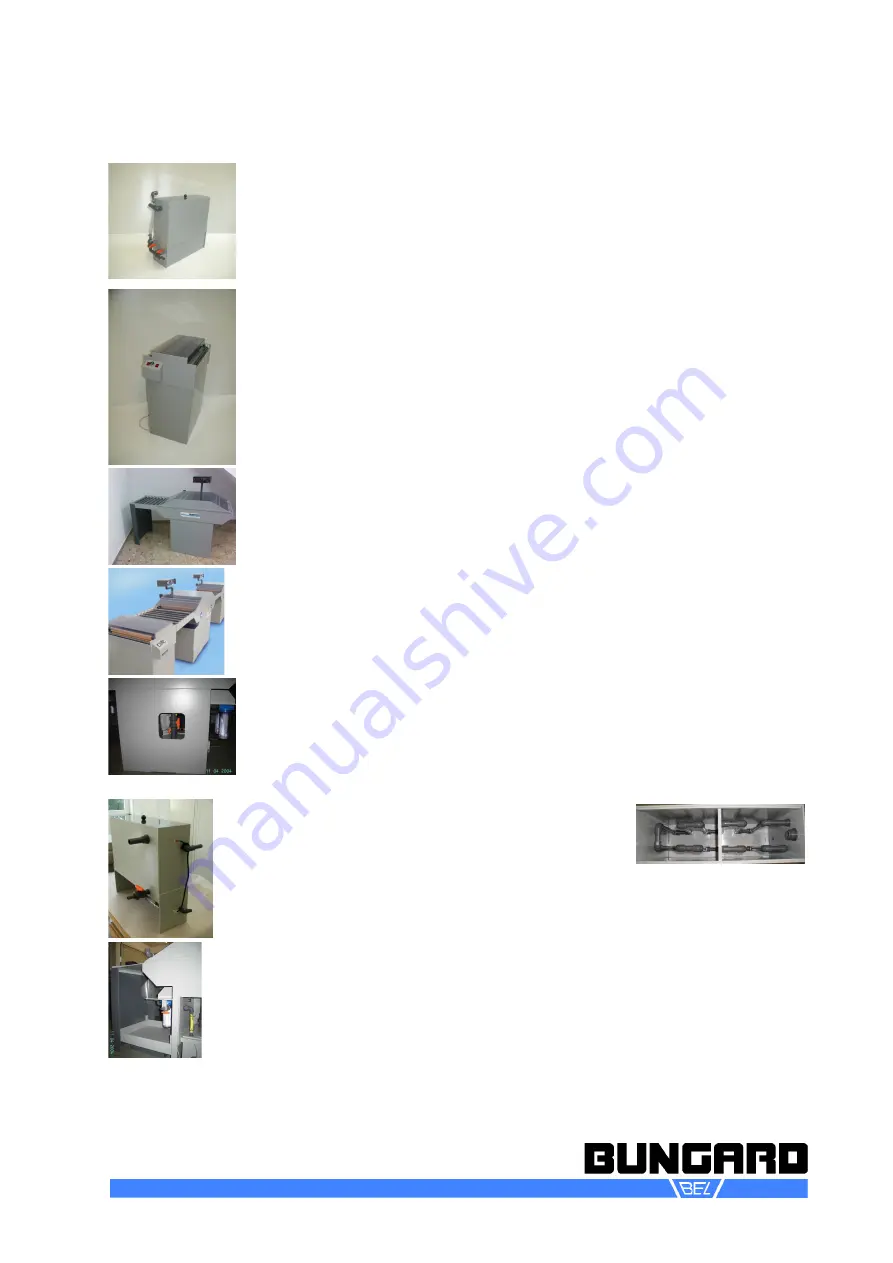
DL500-Manuel-E
Page 3 / 20
Options:
Option # 1: Recycled Rinsing Tank
recycled rinsing tank with magnetic centrifugal pump instead of fresh water. Saves
water costs. With a cock drain valve the used rinsing water can be used to com -
pensate evaporation losses or to make up new etching liquid. Waste water free rins-
ing technique. The magnetic valve from the standard version is here obsolete. The
tank fits underneath the machine body of DL 500. Format: 200x600x700 mm (Bx-
HxT).
Option # 2: Conveyorised Rinsing Unit
a)
conveyorised rinsing unit, stand alone version with adjustable conveyor speed, in-
tegrated magnetic valve for fresh water inlet (controlled by DL 500), squeeze drying
roller. Transport width and height same as DL 500. Format: 450 x 940 x 620 mm
(BxHxT)
b)
as above but second stage cascade rinse (in combination with recycled rinse tank
and magnetic centrifugal pump), 3 way cock valve to bypass rinsing water e.g. to wa-
ter treatment unit IONEX. Format: 450 x 940 x 620 mm (BxHxT)
Option # 3: Inspection Table
Control zone in form of a roller table (not conveyorised). This roller table can be
mounted between two DL 500 (e.g. Developer and Etcher), between DL 500 and
rinsing unit or as a single exit table. Format ca. 620x530x50 mm (BxHxT)
Option # 4: Production Line
3 DL 500 and the rinsing unit can be connected to a small production line (Develop -
ing – Etching – Stripping - Cleaning) coupled together with inspection tables. Of
course other variants are possible as well.
Option # 5 DL 500 Vario
with separately adjustable spray pressure for bottom and
top side.
For physical reasons the etching result on the bottom is better than on the top. For
this reason, may be useful to adapt the spray pressure. Unlike many competitors, the
board in the etch chamber is securely fixed by upper and lower transport rollers so
that the spray pressure for the top can be completely turned off without the board
stands by the lower spray pressure. This Version is standard since 2015!
Option # 6: Cooler
Some etching agents as well as other chemicals tend to
exothermic reactions and need to be cooled during the
treatment process. For this purpose we offer a special
cooler for the DL 500. The Cooler consists of a recyc-
ling rinsing tank with cooling coils for the etching liquid. With a cock valve the etching
agent is adjustable bypassed through the cooler.
Option #8: Filter unit
On request you can equip your DL 500 with one or two 10 " filter units to remove
residues from the etching process. You can easily adjust the filter throughput via
cock valve. On the picture you can see a filter unit together with an exit table.
Bungard Elektronik GmbH & Co. KG, Rilkestraße 1, 51570 Windeck – Germany
Tel.: +49 (0) 2292/5036, Fax: +49 (0) 2292/6175, E-mail: [email protected]