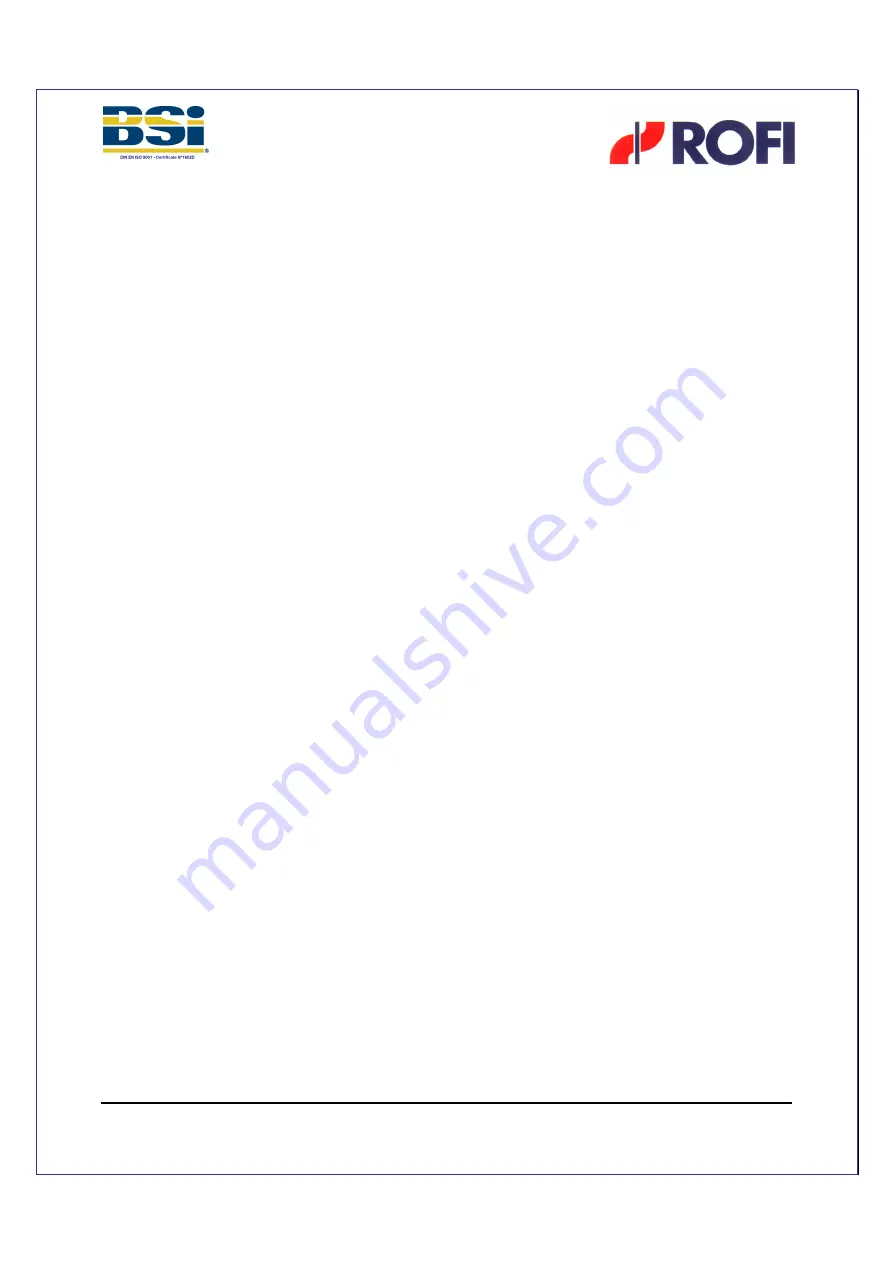
QM-Nr: FB_BMA_01-R-0804engl_3
Erstellt/
Prepared
: am/
on:19/11/2015
Genehmigt/
Approved: am
/
on19/11/2015
7 / 16
by ROFI S.A.R.L.
3. Notes to safe transport and storage
3.1. Transport
When loading or unloading ensure that the valves are not thrown or subjected to sudden knocks. Large
valves should be handled with hemp or synthetic ropes slung to the yoke arms or the bonnet flange.
Valves with actuators should be slung using a three-point suspension at the main connection nozzle and
the yoke arms or yoke head (note centre of gravity). Special eyebolts must be used when supplied with
heavy valves.
To avoid damages at the sealing areas during transport and storage the valves are supplied in closed
position – except of Ball Valves and Swing Check Valves. Locking caps defend the flange openings from
pollution. The valves may not be damaged upon transport and storage. For this reason they are coated
against corrosion with a primer coat. For further protection the valve has to be adapted in the plant
according to the operating conditions.
3.2. Storage
On site the valves must be stored so as to be protected against mechanical damage and/or corrosion. The
preferable storage condition is in closed rooms with ambient temperature. Flanges or weld ends can be
sealed using plugs, lids, plastic caps or oil paper. Internal surfaces can be treated with preservatives or
moisture absorbers. The protective packaging we provide must be left intact during storage and removed
prior to installation or operation respectively.
4. Details on safe installation
During installation and operating, the corresponding valve manuals have to be taken into consideration.
An electro-static conductive connection from the valve to the earthing-potential must be given.
During installation of electrical valves, EN 60079-14 has to be taken into consideration.
Special requirements of the type testing certificates for the installed valves, e.g. electric actuators have to
be taken into consideration.
The valve-actuators has to be conform to the European Directive 94/9/EG (ATEX).
In explosive areas, the electrical equipment installed must be in accordance with the corresponding
category (2 / 3) – EN 50014.
The installation of the electrical device must be in accordance with DIN VDE 0100 and EN 60079.