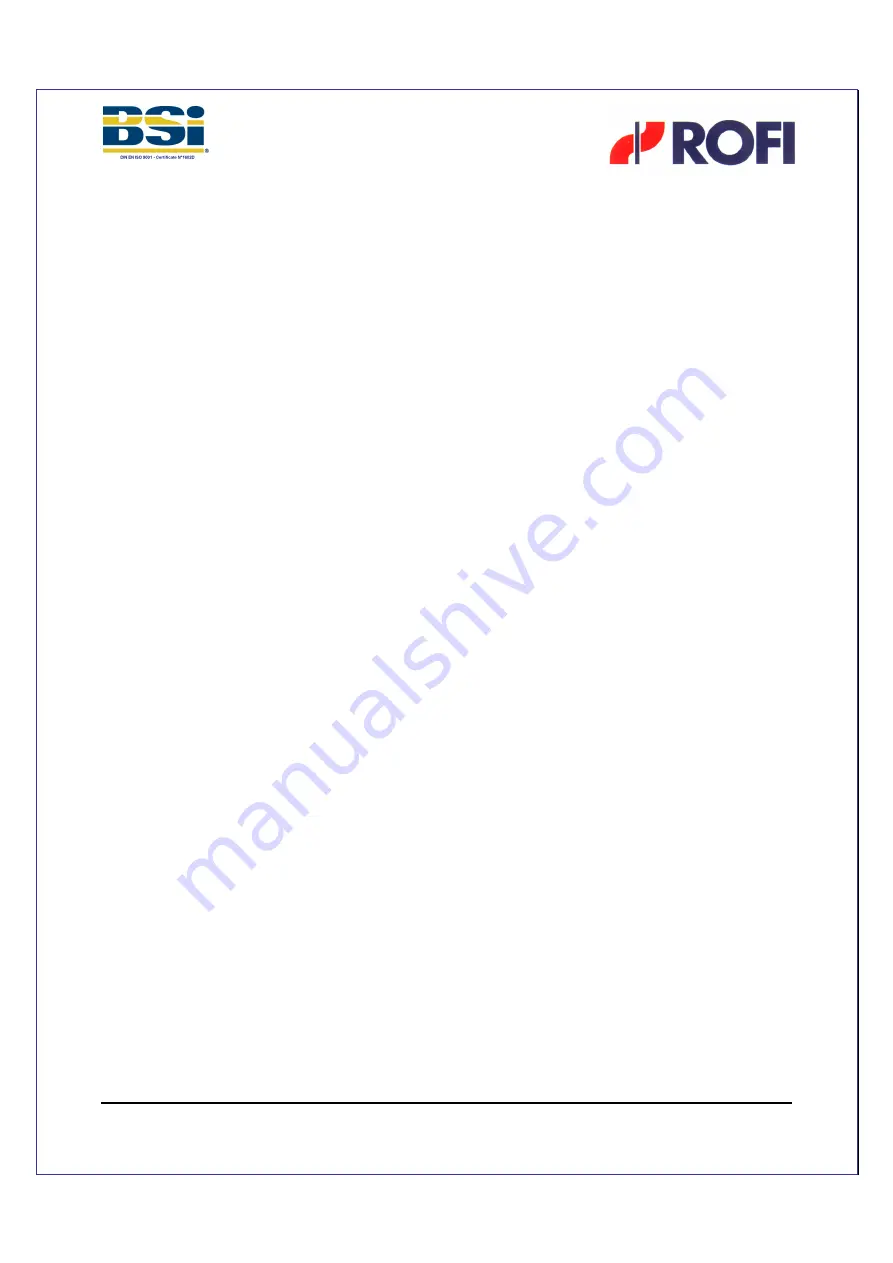
QM-Nr: FB_BMA_01-R-0804engl_3
Erstellt/
Prepared
: am/
on:19/11/2015
Genehmigt/
Approved: am
/
on19/11/2015
10 / 16
by ROFI S.A.R.L.
4.3. Temperature changes
To prevent damage and leakage due to rapid heating, the valves should be provided with properly
designed bypasses or drains that open at the right time. The usual temperature rise rates in power station
duties for example are of the order of 3-6 degrees C per minute. If more rapid warming rates are
anticipated, we should be consulted regarding the appropriate measures to be taken. Frequent operation
through broad temperature ranges at high rates of temperature change can lead to premature fatigue
(relaxation) of the bonnet flange bolts among other components. If in doubt, ask our advice.
4.4. Additional instructions for installation
As a general rule the direction of flow is marked by arrows in accordance with DIN EN 19. In case of
doubt, refer to the relevant sectional drawings. Always allow for adequate access clearance in the
planning and installation phase for easy assembly and disassembly of internal valve parts. Valves should
never be taken as fixed reference points within pipe systems, and substantial pipe loadings on valves
should therefore be avoided. Exceptions to this rule are subject to our specific approval for each individual
case. It has to be on a case-by-case basis because the forces resulting, for example, from shear, bending
and torsional stresses as well as temperature gradients vary according to duty and installation, and occur
in a variety of combinations. We are therefore not able to make any generalizations. Before fitting the
valve in position, remove the flange- or butt weld end protectors and moisture absorbers, if provided. The
valve must be free from foreign matter of any nature. Cleanliness is the cardinal rule when fitting valves. If
the pipe ends require machining, chips and other foreign matter must be carefully removed. The pipe ends
must be properly aligned so as to prevent the valve being subjected to unnecessary strain. Bricklaying or
painting should not be carried out in the vicinity of installed valves until stuffing boxes, spindles and valve
position indicators (if fitted) have been properly protected against soiling. Valves are despatched from our
works with a high shut-seal property. This is a quality feature that can only be maintained if care is taken
during installation and subsequent operation to prevent the ingress of foreign matter into the valve and
hence damage to seats and other areas.
4.4.1. Flanged Valves
The sealing faces of flanged valves must be clean and in good condition. Before bolting-down, flanges
must be correctly aligned. When bolting-down, all flange boreholes must be used at all times. For initial
fitting, threads can be smeared with graphite or molybdenum-di-sulphide to stop seizure - do not use oils
or greases. Never use damaged parts such as bolts, nuts or washers. Make sure that materials are
suitable and correct for the job. Tighten bolts evenly and in cross-sequence using the correct tools to the
correct torques (see chapter 5.1).
4.4.2. Valve with butt-weld or socket-weld ends
The piping contractor is responsible for welding the valves into the pipeline and any necessary heat
treatment. Gate and Globe valves should be lightly closed to prevent damage to the seating surfaces and
stem caused by thermal expansion during the socket welding process. Never attach the welding cable
(opposite pole) to the bonnet, spindle or any other places on the valve assembly! This could cause spots
of arcing on the spindle or seat faces. The weld cable should be attached to a bright area on the valve
body or, even better, to the pipe itself. For valves with socket weld ends, the socket depth of the pipe ends
should be selected in accordance with codes of practice, and unacceptable weld-seam stresses prevented
by leaving a gap between pipe end and socket seat.