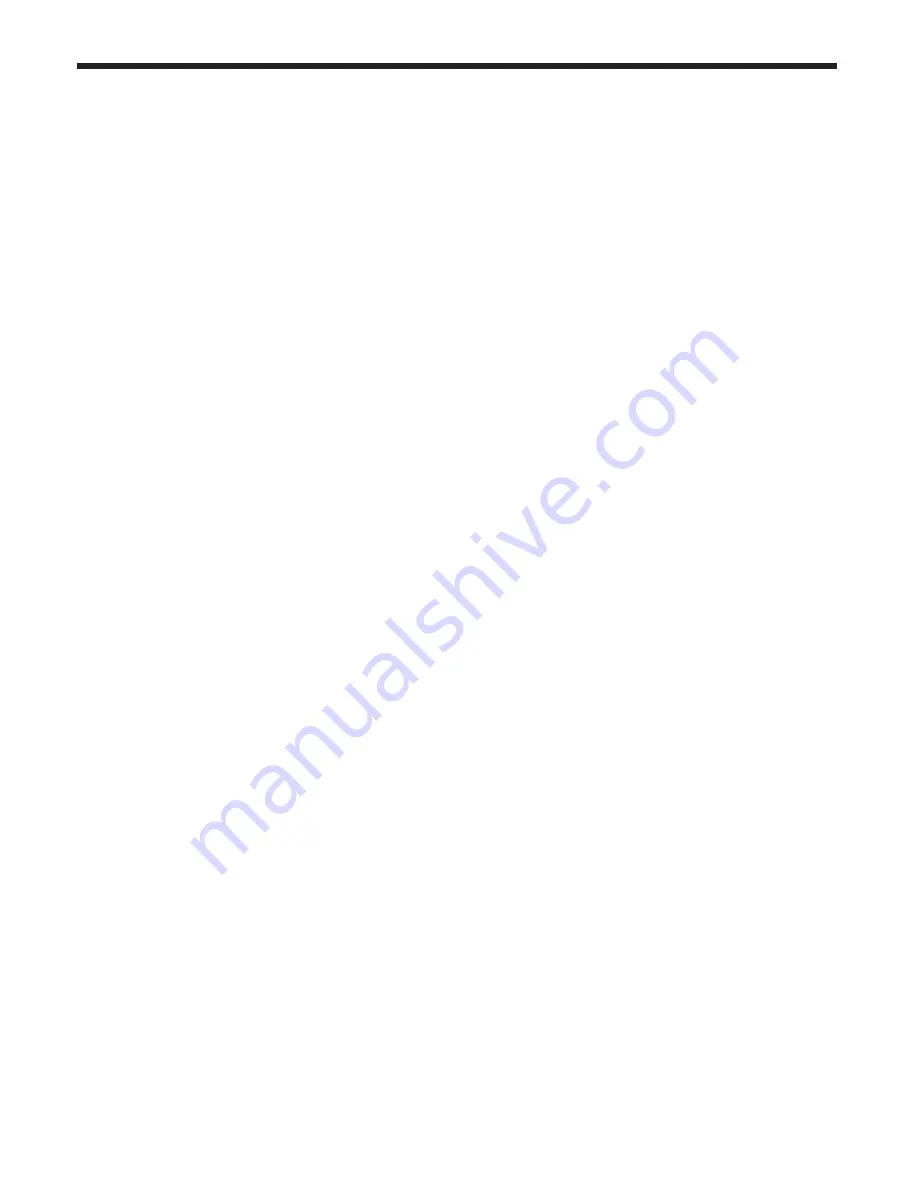
Page 19
MagnaTech
BOILERS AND VOLUME WATER HEATERS
be equipped with flow control valves or other
automatic means to prevent gravity circulation
of the boiler water during the cooling cycle.
A boiler installed above radiation level, or as
required by the authority having jurisdiction,
must be provided with a low water cutoff device
either as a part of the boiler or at the time of
boiler installation.
6.3 BMGH Freeze Protection
MagnaTech units may be installed indoors
or outdoors. If installing outdoors in a location
that may experience freezing temperatures,
precautions must be taken to prevent water in
the heat exchanger and condensate inside and
outside of the boiler from freezing. Damage due
to freezing water or condensate is not covered by
the warranty.
If installed indoors, and there is an event such
as a power outage, interruption of gas supply,
failure of system components, activation of
safety devices, etc., this may prevent a boiler
from firing.
Any time a boiler is subjected
to freezing conditions, and the boiler is not
able to fire, and/or the water is not able to
circulate, there is a risk of freezing in the
boiler or in the pipes in the system.
When
water freezes, it expands. This may result
in bursting of pipes, or damage to the boiler,
and this could result in leaking or flooding
conditions.
Do not use automotive antifreeze. To help
prevent freezing, Bradford White recommends
the use of inhibited glycol concentrations
between 20% and 35% glycol. Typically, this
concentration will serve as burst protection
for temperatures down to approximately -5°F
(-20°C). If temperatures are expected to be
lower than -5°F (-20°C), glycol concentrations
up to 50% can be used.
When concentrations
greater than 35% are used, water flow rates
must be increased to maintain a 20°F to 25°F
temperature rise through the boiler.
Section 6 -
WATER CONNECTIONS
BMGH BOILERS
6.1 BMGH System Piping:
Hot Supply Connections
Note -
This appliance must be installed in a closed
pressure system with a minimum of 12 psi (82.7
kPa) static pressure at the boiler.
The hot water piping should be supported
by suitable hangers or floor stands. Do not
support the piping with this appliance. The
hangers used should allow for expansion and
contraction of pipe. Rigid hangers may transmit
noise through the system resulting from the
piping sliding in the hangers. We recommend
that padding be used when rigid hangers are
installed. Maintain 1” (2.5 cm) clearance to
combustibles for all hot water pipes.
Pipe the discharge of the relief valve (full size)
to a drain or in a manner to prevent injury in the
event of pressure relief. Install an air purger,
an air vent, an expansion tank, a hydronic flow
check valve in the system supply loop, and
any other devices required by local codes. The
minimum fill pressure must be 12 psig (82.7
kPa). Install shutoff valves where required by
code.
Suggested piping diagrams are shown in Figure
7 through Figure 10. These diagrams are meant
only as guides. Components required by local
codes must be properly installed.
The MagnaTech’s efficiency is higher with
lower return water temperatures.
Therefore,
to get the best low return temperature with
multiple boilers, pipe as shown in Figure 9 and
Figure 10.
6.2 BMGH Cold Water Make-Up
1. Connect the cold water supply to the inlet
connection of an automatic fill valve.
2. Install a suitable back flow preventer
between the automatic fill valve and the
cold water supply.
3. Install shut off valves where required.
In some installations, a hot water heating
boiler is connected to heating coils located in
an air handling appliance where the coils may
be exposed to refrigerated air circulation. In
these cases, the boiler piping system must
Содержание MagnaTech BMGH1600
Страница 4: ...BRADFORD WHITE ...
Страница 35: ...Page 31 MagnaTech BOILERS AND VOLUME WATER HEATERS ...
Страница 98: ...Page 94 BRADFORD WHITE 1 13 12 4 3 5 13 2 15 Final Assembly DETAIL A 9 10 8 Final Assembly ...
Страница 110: ...Page 106 BRADFORD WHITE 6 2 7 11 1 5 4 12 10 3 3 8 9 6 Control Panel Assembly ...
Страница 114: ...Page 110 BRADFORD WHITE 7 8 15 14 9 4 16 12 5 1 6 2 11 AC DISTRIBUTION BOX ASSEMBLY PART NUMBERS MODELS 2500 AND 3500 ...