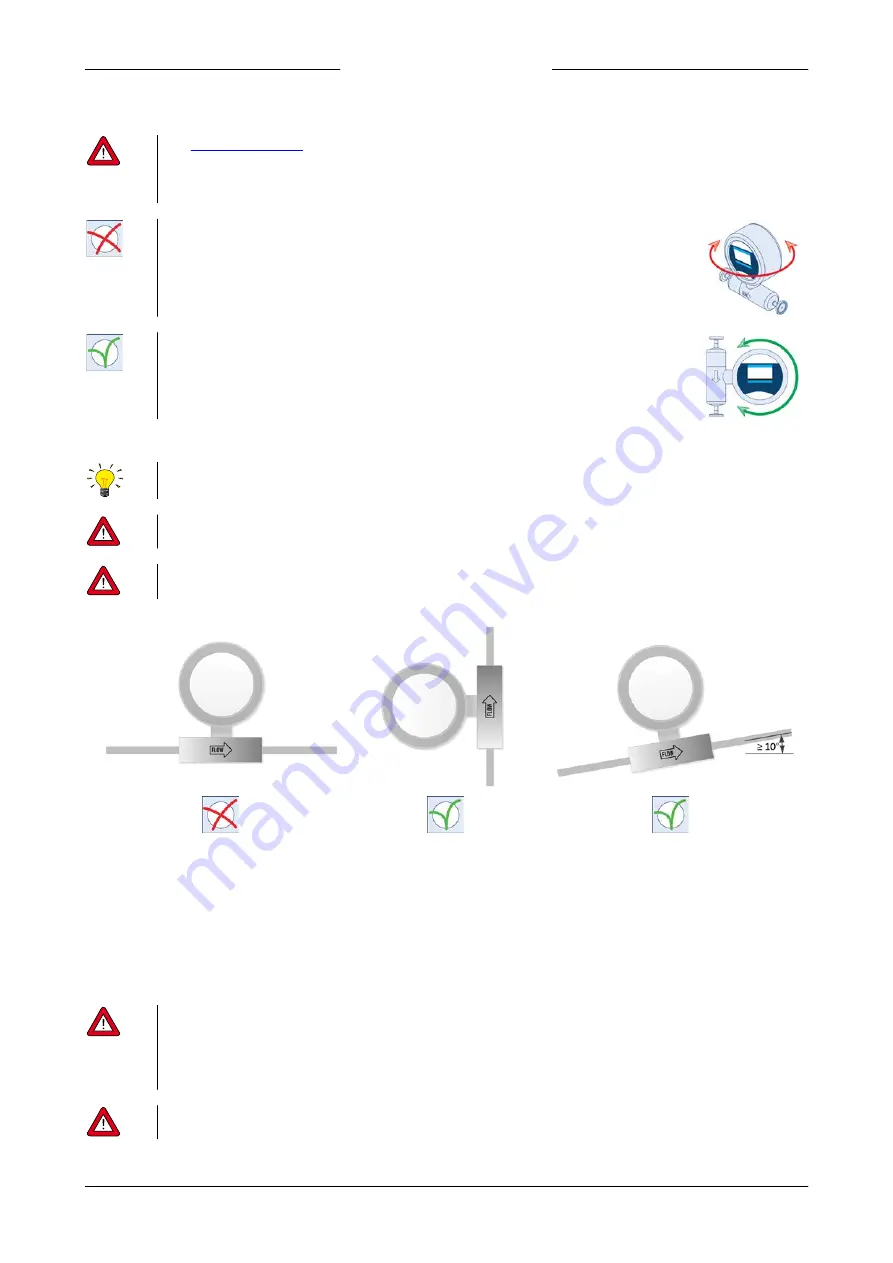
Bronkhorst®
Instruction Manual ES-FLOW™
9.17.145E
13
2.2.2
Orientation
·
In
, the
ES-FLOW™
should be mounted in such a way that it allows self-draining (see further).
·
To prevent liquid from pooling on the display surface, the instrument should not be mounted with the display surface
facing up.
·
Other than that, the instrument has no preferred mounting orientation.
Note that the connection between the measuring tube and the electronics housing is fixed; the housing
cannot be rotated to get a better view of the display. Its orientation can only be altered by
repositioning the entire instrument.
On models starting from MkII, the flow direction and display orientation can be adjusted at the
factory, for which the instrument has to be returned. Contact your Bronkhorst representative for more
information and arrangements.
2.2.3
Hygienic applications
In order to comply with the 3-A Sanitary Standards, the
ES-FLOW™
should be mounted in a location where its exterior
cannot come into direct contact with food substances and/or the product contact surfaces of their packaging material.
For Sterilization in Place (SIP) it is advised to mount the instrument with the electronics housing (display) below the sensor
tube, to prevent rising hot air from damaging the display and/or electronics.
To allow self-draining, mount the
ES-FLOW™
vertically or with a minimum inclination of 10°, with the normal flow going
upward (note the FLOW arrow on the instrument).
2.3
Fluid connections
The FLOW arrow on the measuring tube indicates the normal flow direction. For normal use, install the
ES-FLOW™
in the
process line, in accordance with the direction of the FLOW arrow. For bi-directional measuring, install the instrument in the
direction in which the highest flow will be measured (if applicable). When deciding which direction to install the instrument
in, take into account that the measuring range in the reverse direction is approximately 73% of the full scale range (whereas
the instrument can measure 131% FS in the normal direction).
Tighten fittings according to the instructions of their manufacturer.
·
Use piping or tubing that is suitable for the operating conditions of the application (media, maximum temperature,
maximum operating pressure).
·
Do not install small diameter piping/tubing on high flow rates and avoid abrupt angles or other disturbances within a
distance of 10 times the (inside) pipe diameter from the inlet or outlet of the device.
·
Do not install pressure regulators within a distance of 25 times the (inside) pipe diameter from a controlling instrument.
Check the fluid system for leaks before applying full operating pressure, especially when using hazardous media (e.g. toxic
or flammable).