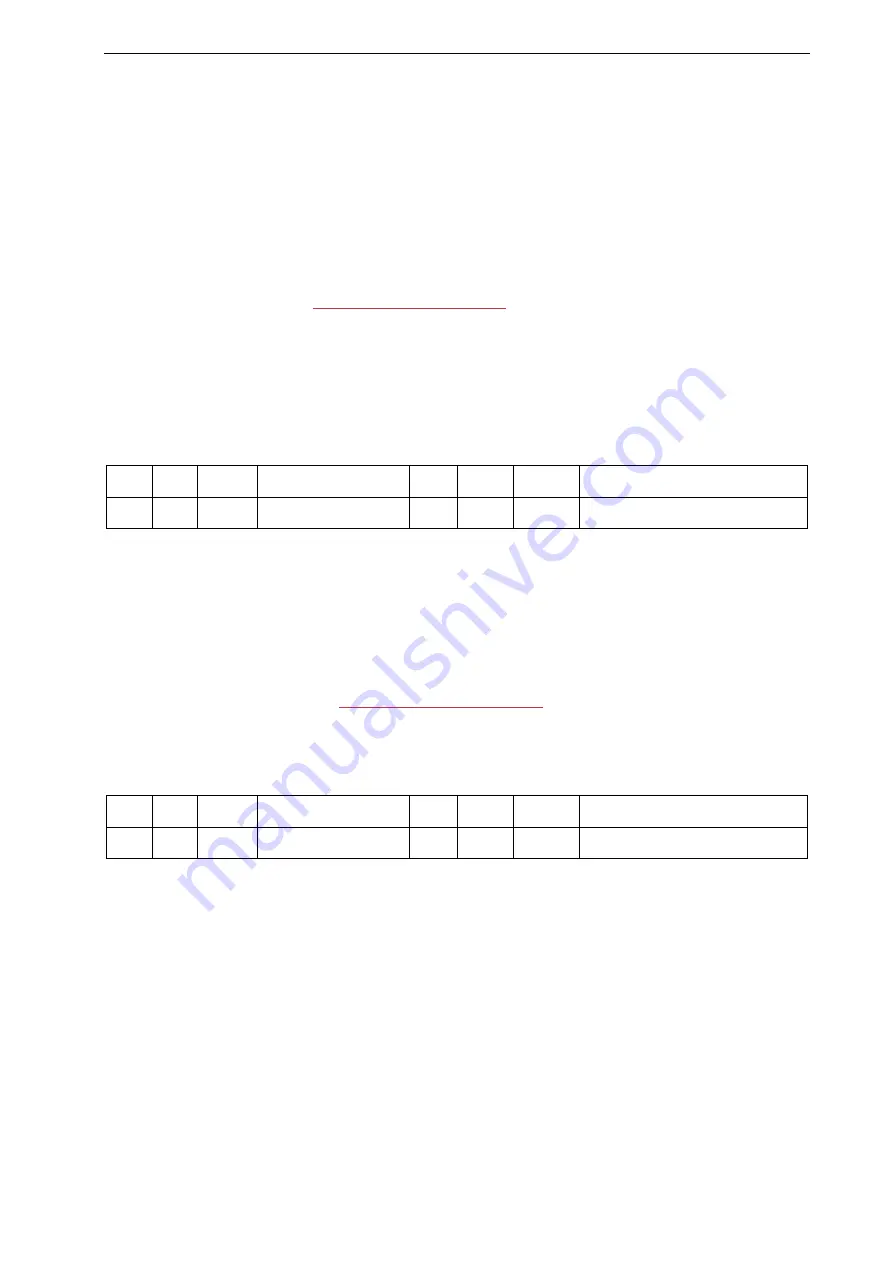
Liquid Dosing Control Manual
9.17.150 rev A – September 2020
Page
30
of
34
5.4 Correct for actuator delay
A control valve (or pump) needs a minimum electrical current (threshold) to open (or start
running). Normally, when opening the valve, the current is increased gradually, until the threshold
is reached and the valve opens. The time to reach the threshold (dead time) can be minimized,
by specifying a starting power/current, just under the threshold. This shortens the valve response
time, because the starting power is immediately applied when the valve is opened (instead of
gradually).
- Write value <_> to parameter 190 – Valve Open
(set opening power)
Value as required. An automated script can be performed in FlowPlot to automatically
determine an optimum setpoint.
Note,
in the firmware is referred to the parameter as ‘Valve Open’, but when a pump is
used, this parameter can be considered as the threshold to enable or start the
Actuator.
Step DDE ProPar Name
Data
Type Execute Value
Remark
1
190
114/24 Valve Open
Float Write X
Minimum power (Amps) to stay
open shut-off
5.5 Setpoint Slope
Setpoint slope can be used to smooth 'nervous' behavior of the PID controller (reduce setpoint
overshoot or undershoot), but with proportional batch dosing, this might lengthen the dosing time
unacceptably. The recommended value for Setpoint slope is 0.
- Write value <_> to parameter 10 – Setpoint Slope
(smoothen PID behaviour)
Adjustment time when changing setpoint from 0% - 100%.
The value can be set from 0 – 30000, where value 100 will result in a time of 10 seconds.
Step DDE ProPar Name
Data
Type Execute Value
Remark
1
10
1/2
Setpoint Slope
Uint16 Write X
0 – 30000, where value 100 will
result in a time of 10 seconds.