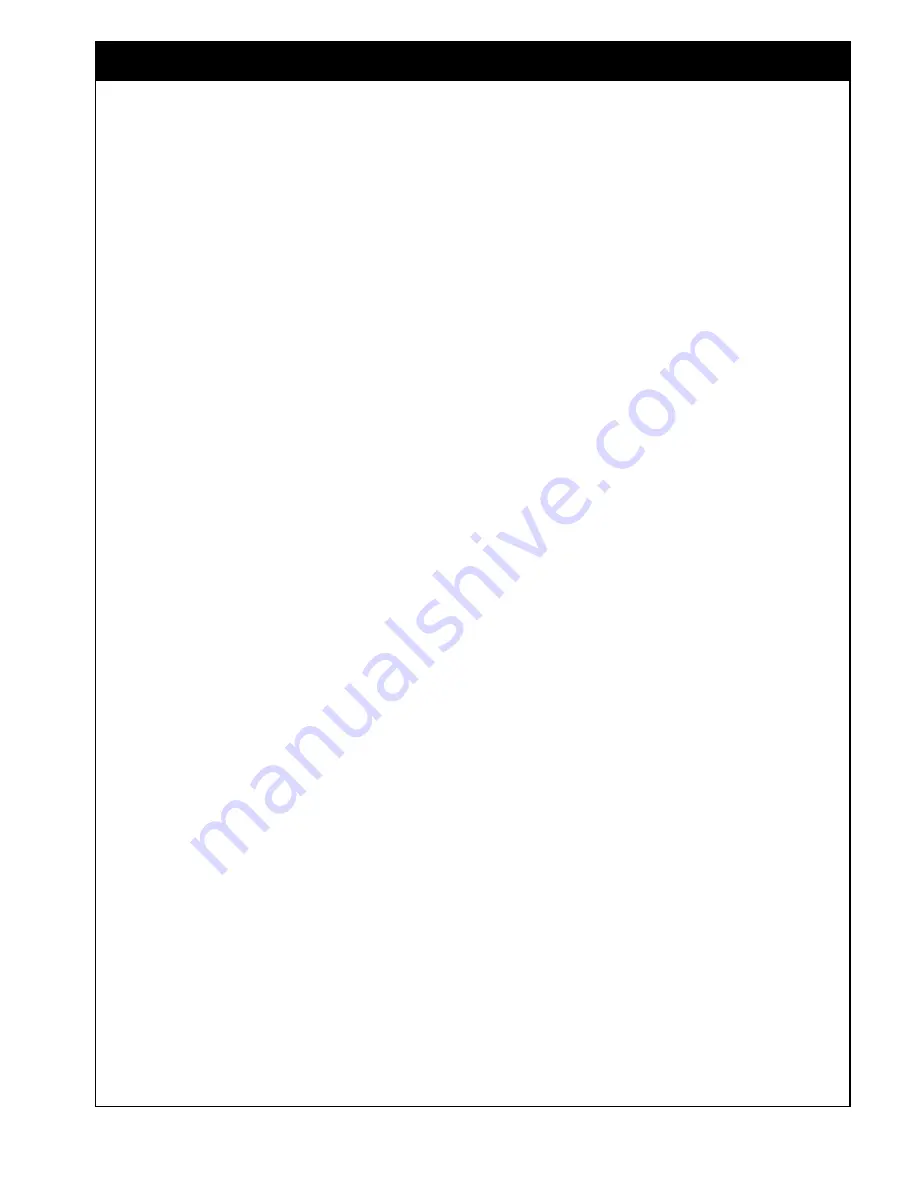
9000 Series Air Seeder
Service & Maintenance
10.1
10 Service and Maintenance
10.3.1.3 Harness Re-Configuration
..................................................................................10.13
Surge Brake System Pressure .................................................................10.18