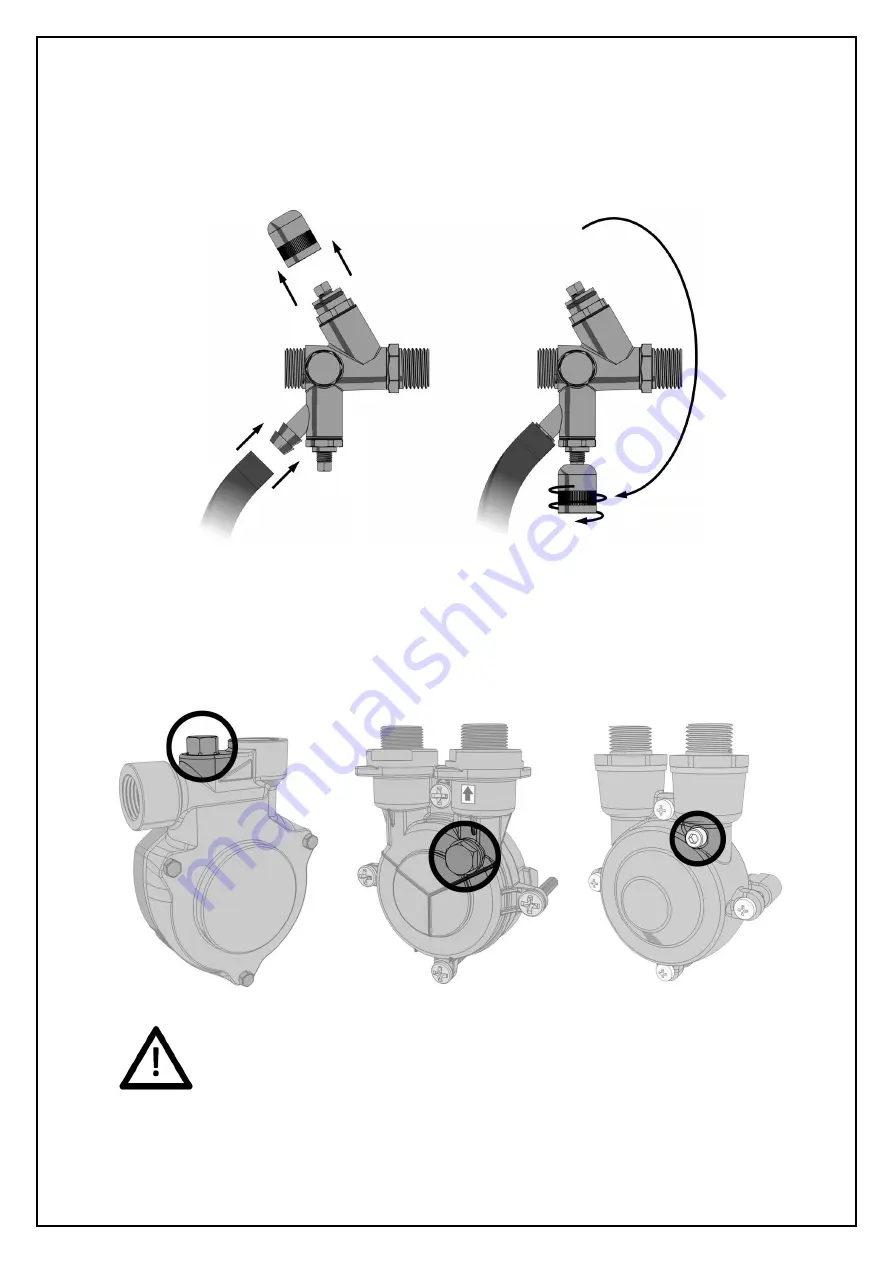
21
Attach a length of hose to the hose tail on the drain valve and put the other end to drain. Then, using
the cap off the isolation valve, open the drain valve:
Locate the bleed screw on the pump. The following diagrams show examples of typical bleed screw
locations for most pumps:
Do not use excessive force when tightening the bleed screw as this may damage the
pump casing.
Содержание AX1-2.5E
Страница 33: ...33 Wiring Diagram ...
Страница 34: ...34 Service Log This service log should be completed by the service engineer after each annual service ...
Страница 35: ...35 ...
Страница 41: ...41 Notes ...
Страница 42: ...42 Notes ...
Страница 43: ...43 Notes ...
Страница 44: ...44 Notes BOSS Pressurisation O M Manual Version 8 February 2014 ...