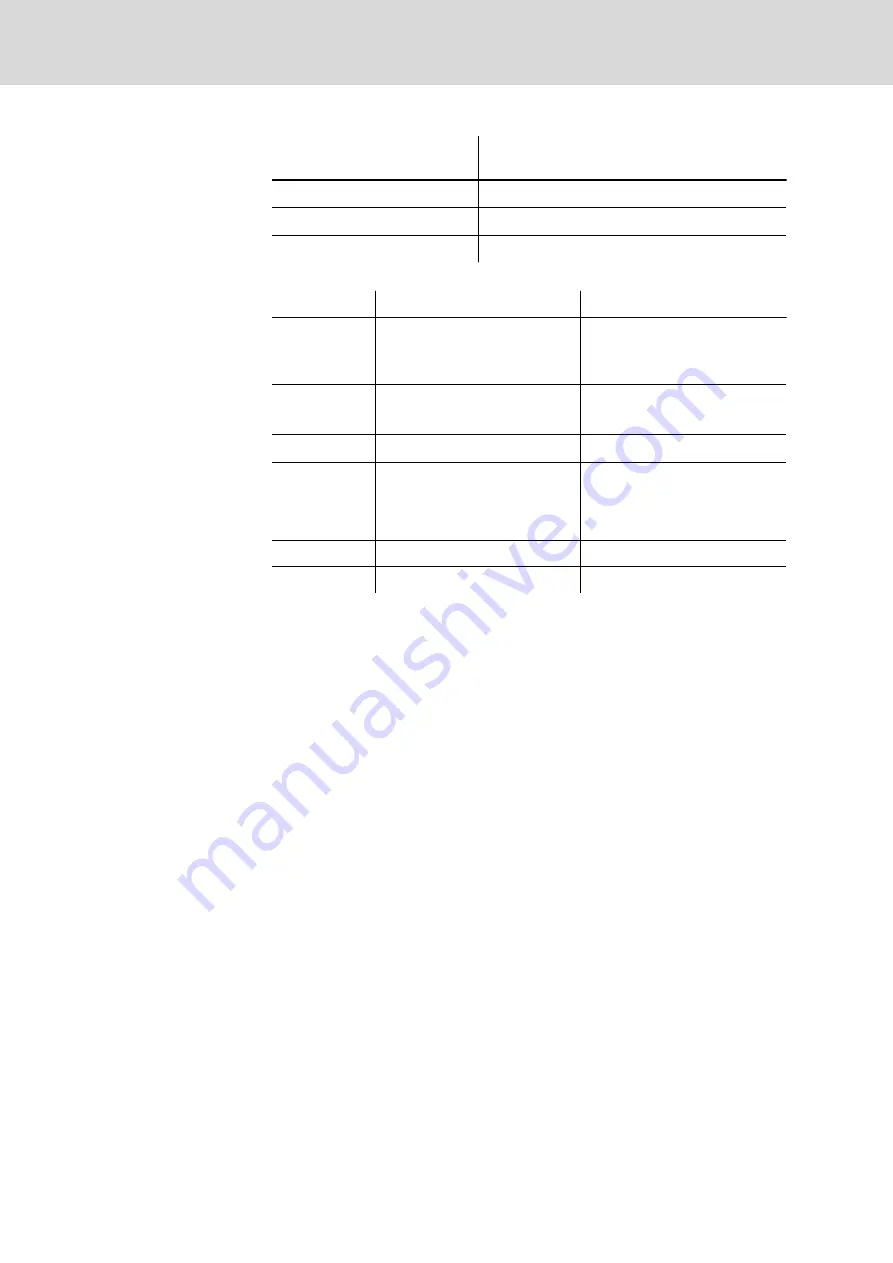
PL (Performance Level)
Average probability of a dangerous breakdown
per hour 1/h
c
≥10
-6
to < 3 x 10
-6
d
≥10
-7
to < 10
-6
e
≥10
-8
to < 10
-7
Tab.4-23:
EN ISO 13849-1, Performance Level (PL)
Abbreviations
Abbreviation
Term
Explanation
B
10d
-
Number of cycles until 10% of
the components fail dangerously
(per channel)
MTTF
d
Mean Time to Dangerous Fai‐
lure
Meant time to dangerous failure
(per channel)
DC
Diagnostic Coverage
Diagnostic of failures
PL
Performance Level
Ability of safety-related parts to
perform a safety function under
predictable conditions to meet
the expected risk reduction
PFH
Probability of Failure per Hour
Probability of failure per hour
SIL
Safety Integrated Level
Safety integrated level
Tab.4-24:
Abbreviations
Selection of Performance Level
(PL) and Safety Categories ac‐
cording to EN ISO 13849-1
The Machinery Directive (MD) demands that a fault in control circuit logic, or
an interference or damage thereto, must not lead to a hazardous situation.
This general approach is substantiated in EN ISO 13849-1 "Safety of machi‐
nery - safety related parts of control systems", which defines Performance
Levels (PL a to e) for control parts that are relevant to safety. The PL de‐
pends on the safety category, the MTTF
d
value and the degree of coverage
of diagnosis (DC
avg
) of the corresponding safety circuit.
As in the preceding standard EN 954-1, the safety category describes the
structure of the safety function. The Performance Level (PL), which describes
the conditional probability of failure and the defect discernability of the safety
function, has been added.
The manufacturer of a machine has to select the PL depending on the real
risk potential. The risk potential will be determined from a risk and hazard
analysis. In case of hazards that can cause irreversible injury or death usually
a Performance Level not less than PL "d" is required. The category of the
Performance Level determines if
●
the system has been built in 1-circuit technology, which means that a
failure will lead to a loss of safety, although the availability of compo‐
nents and parts is high (category 1)
●
the system has been built in 1-circuit technology, which means that a
failure will lead to a loss of safety, but the failure will be detected by the
system and will be displayed somehow or other (category 2)
●
the system has been built in 2-circuit technology and that a fault will not
lead to loss of safety (category 3)
DC also means direct current.
Bosch Rexroth AG
DOK-SUPPL*-VEH*30.2***-PR03-EN-P
Rexroth IndraControl VEH 30.2 Hand-Held Terminal
36/109
Technical Data
Содержание REXROTH IndraControl VEH 30.2
Страница 12: ...Bosch Rexroth AG DOK SUPPL VEH 30 2 PR03 EN P Rexroth IndraControl VEH 30 2 Hand Held Terminal 10 109 ...
Страница 52: ...Bosch Rexroth AG DOK SUPPL VEH 30 2 PR03 EN P Rexroth IndraControl VEH 30 2 Hand Held Terminal 50 109 ...
Страница 58: ...Bosch Rexroth AG DOK SUPPL VEH 30 2 PR03 EN P Rexroth IndraControl VEH 30 2 Hand Held Terminal 56 109 ...
Страница 82: ...Bosch Rexroth AG DOK SUPPL VEH 30 2 PR03 EN P Rexroth IndraControl VEH 30 2 Hand Held Terminal 80 109 ...
Страница 96: ...Bosch Rexroth AG DOK SUPPL VEH 30 2 PR03 EN P Rexroth IndraControl VEH 30 2 Hand Held Terminal 94 109 ...
Страница 102: ...Bosch Rexroth AG DOK SUPPL VEH 30 2 PR03 EN P Rexroth IndraControl VEH 30 2 Hand Held Terminal 100 109 ...
Страница 104: ...Bosch Rexroth AG DOK SUPPL VEH 30 2 PR03 EN P Rexroth IndraControl VEH 30 2 Hand Held Terminal 102 109 ...
Страница 110: ...Bosch Rexroth AG DOK SUPPL VEH 30 2 PR03 EN P Rexroth IndraControl VEH 30 2 Hand Held Terminal 108 109 ...
Страница 111: ...Notes DOK SUPPL VEH 30 2 PR03 EN P Rexroth IndraControl VEH 30 2 Hand Held Terminal Bosch Rexroth AG 109 109 ...