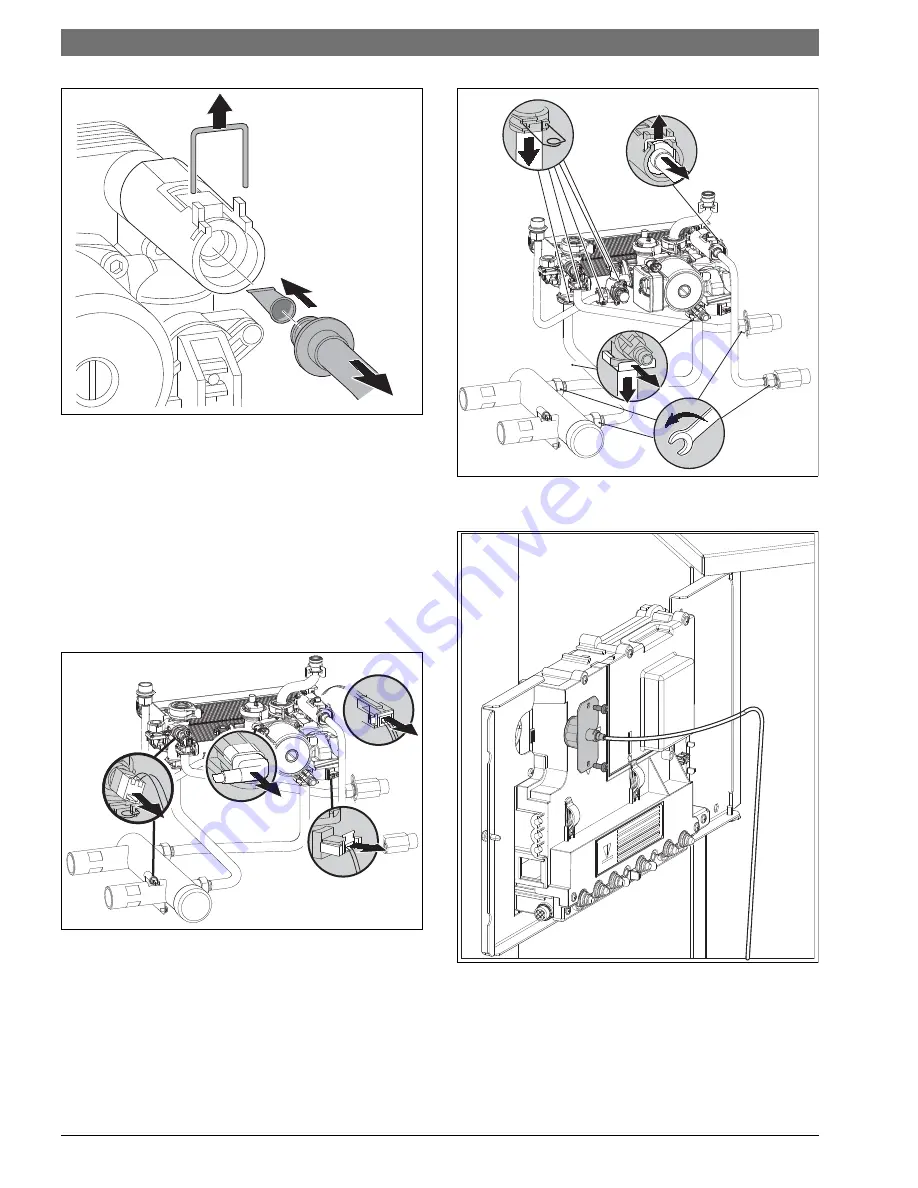
66
|
Inspection and maintenance
Greenstar FS
6 720 810 590 (2015/05)
Fig. 77 Filter in fresh water pipe (combi boiler KWB.-3A only)
15.1.3 Plate type heat exchanger (only combi boiler KWB..-3A)
If the DHW output on the combi boiler is significantly reduced:
▶ Check filter in the cold water pipe for contamination (
Fig. 65).
▶ Depressurize the appliance.
▶ Remove the plate type heat exchanger and replace with a new unit.
-or-
▶ Descale with descaling agent approved for stainless steel (Grade
316-1.4401).
To remove the plate type heat exchanger:
▶ Unplug electrical connections.
▶ Remove hose from safety relief valve.
Fig. 78 Unplugging electrical connections / removing hose from PRV
▶ Loosen/remove pipe connections.
Fig. 79 Removing pipe connections
▶ Remove the boiler pressure gauge from the Heatronic boiler control.
Fig. 80 Removing the boiler pressure gauge
▶ Loosen the quick releases (steps 1 and 2) and remove the hydraulic
assembly in its entirety (step 3).
6 720 641 933-92.1o
1
2
3
6720810590-41.1Wo
6720810590-42.1Wo
6720810590-32.1W
o
Содержание KBR16-3
Страница 81: ...Spare parts 81 6 720 810 590 2015 05 Greenstar FS Fig 94 Group 1 Sheet metal Greenstar 6720810590 73 1Wo ...
Страница 85: ...Spare parts 85 6 720 810 590 2015 05 Greenstar FS Fig 96 Group 3 Gas valve Greenstar 6720810590 75 1Wo ...
Страница 91: ...Spare parts 91 6 720 810 590 2015 05 Greenstar FS Fig 99 Group 6 Control box Greenstar 6720810590 78 1Wo ...
Страница 98: ...98 Greenstar FS 6 720 810 590 2015 05 Notes ...
Страница 99: ... 99 6 720 810 590 2015 05 Greenstar FS Notes ...