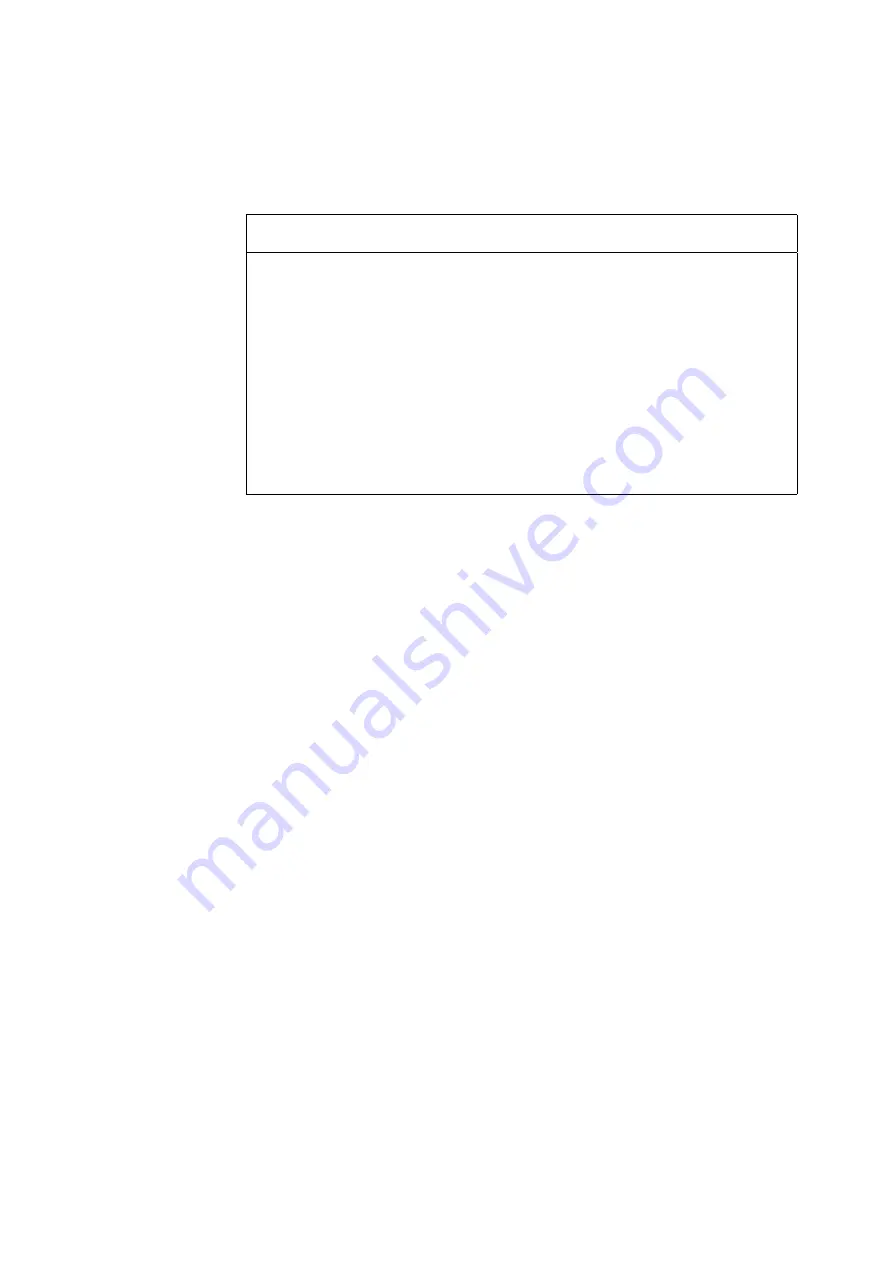
56/68
Maintenance and repair
Bosch Rexroth Mellansel AB
,
Installation and maintenance manual , Hägglunds CB, RE 15302-WA/05.2019
10 Maintenance and repair
10.1 Cleaning and care
NOTICE
Damage to surface!
Aggressive solvents and detergents may damage the seals on the hydraulic motor
and cause them to age faster.
▶
Never use solvents or aggressive detergents.
▶
If in doubt, check the compatibility of the detergent with the seal type (Nitrile or
Viton) specified in the hydraulic motor.
Damage to the hydraulic system and the seals!
Using a high-pressure cleaner could damage the speed sensor and the seals of the
hydraulic motor.
▶
Do not point the high-pressure cleaner at sensitive components, e. g. shaft seals,
seals in general, electrical connections, speed sensors and valves.
For cleaning and care of the hydraulic motor, observe the following:
1. Plug all openings with suitable protective caps/devices.
2.
Check whether all plugs and plug seals are securely seated to ensure that no
moisture can penetrate into the hydraulic motor during cleaning.
3.
Use only water and, if necessary, a mild detergent to clean the hydraulic motor.
4. Remove coarse dirt from the outside of the motor and keep sensitive and
important components, such as sensors and valve blocks clean.
10.2 Inspections
10.2.1 Oil inspection
Purpose of taking oil sample
The purpose of oil sampling is to check the condition of the hydraulic fluid.
With scheduled oil analysis, wear products can be identified and corrective action
can be taken before failure occurs. Oil analysis can indicate when an oil change is
required, point out shortcomings in maintenance and keep repair cost to a minimum.
Using oil analysis can create a “window of opportunity”, allowing the user to
schedule overhauls, maintenance or repairs, thus saving money on equipment repairs
and unplanned downtime.
The most used method is to take samples in a clean sample bottle and send it to a
fluid laboratory for an analysis. The laboratory should deliver a report following a
specific international standard.
The analysis should at a minimum cover viscosity, oxidation, water content and
particle counting (possibly including element analysis of particles). Another method
is to install an inline particle counter direct in your hydraulic system which provides
the contamination level according to international standards. The disadvantage with
this method is that you only get the contamination level in the oil.