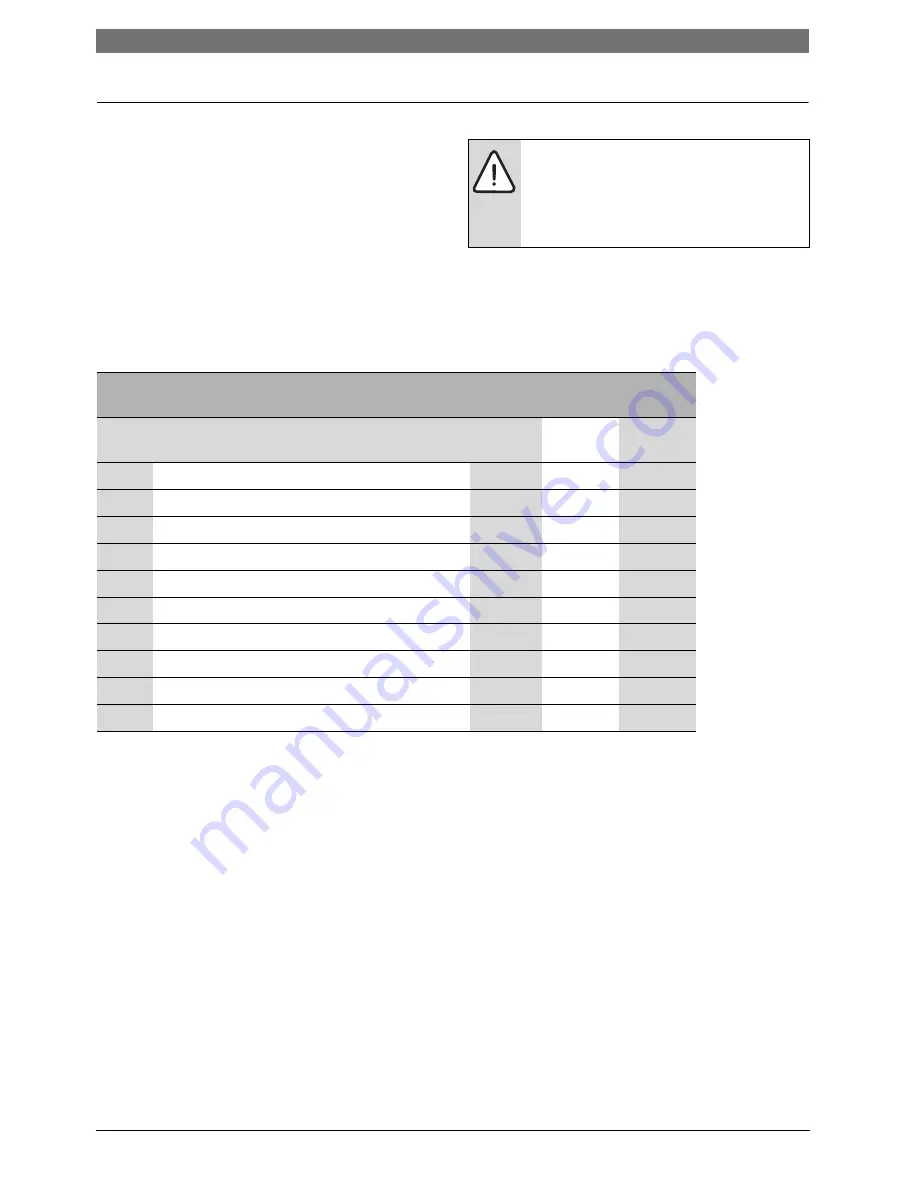
20
|
Pre-installation
AU/NZ
6 720 646 195a (2010/11)
3.8
Flue options
The Condens 5000W series has the option of three
horizontal RSF (60/100 telescopic, 60/100 extended
telescopic and 80/125) flue systems and two vertical
RSF (60/100 or 80/125) flue systems:
The flue systems have different maximum flue lengths
The page opposite shows some possible flue
configurations.
Table 19 below shows the maximum straight length of
flue available to the installer after the effective lengths
of the bends have been taken into account from each
flue option on the page opposite.
NOTE:
Effective flue lengths:
B
each 90° bend used is equivalent to
2 metres of straight flue
B
each 45° bend used is equivalent to
1 metre of straight flue
Maximum straight flue length
available (mm)
Flue type
Boiler
i System
60/100
80/125
1
Telescopic horizontal flue assembly
All
570
1,070
2
Horizontal flue extension
All
4,600
13,000
3
Horizontal flue with 1 x 90° bend
All
2,600
11,000
4
Horizontal flue with 2 x 90° bends
All
N/A
9,000
5
High level horizontal flue with 1 x 90° bend
All
2,600
11,000
6
High level horizontal flue with 2 x 90° bends
All
N/A
9,000
7
High level horizontal flue with 3 x 90° bends
All
N/A
7,000
8
Vertical balanced flue assembly
All
6,400
15,000
9
Vertical balanced flue with 2 x 90° bends
All
2,400
11,000
10
Vertical balanced flue with 2 x 45° bends
All
4,400
13,000
Tab. 19 Flue options