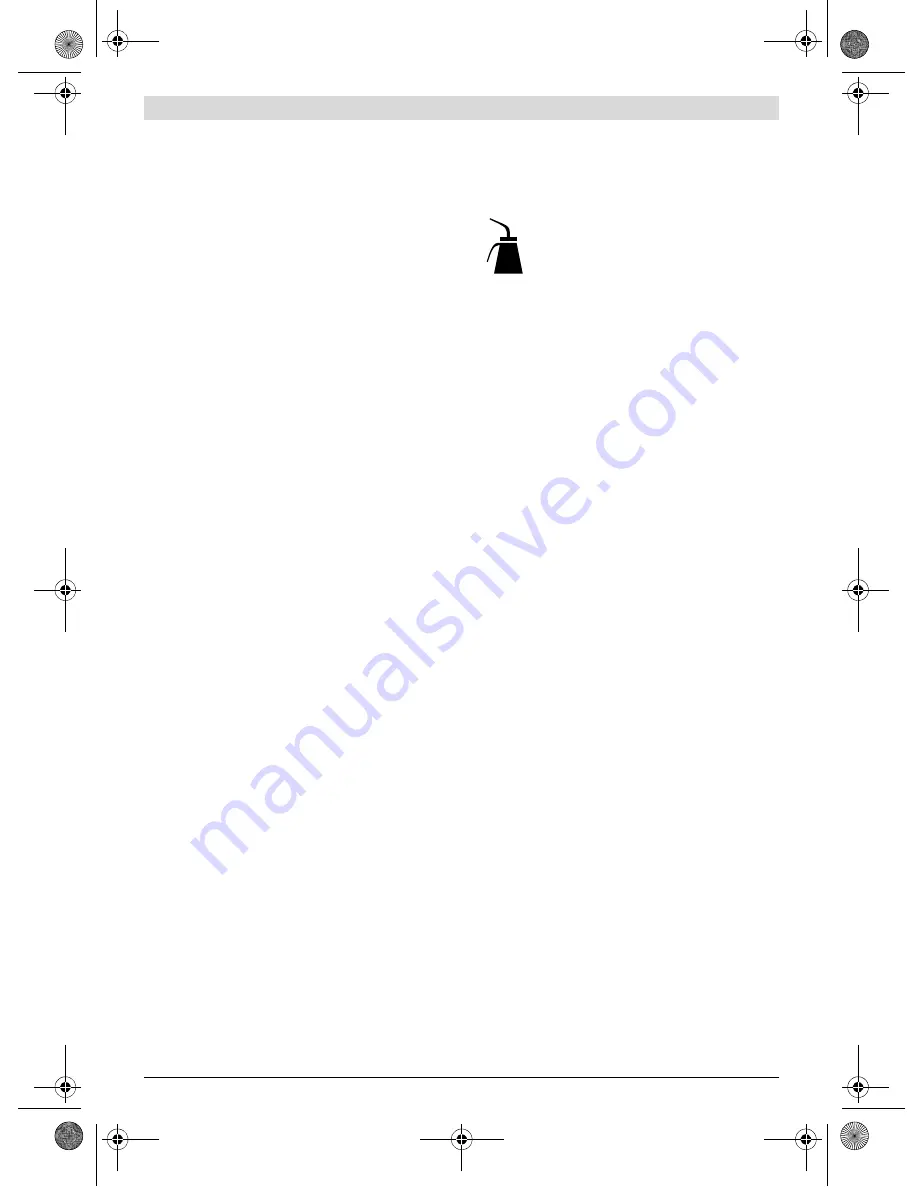
18
| English
3 609 929 C44 | (6.12.13)
Bosch Power Tools
Operate the rotational direction switch only when the
tool is not in use.
0 607 450 614
–
Right rotation: For screwing in bolts and nuts, turn the
rotational direction switch
4
in a clockwise direction to
1 (lowest torque), 2 or to the stop (highest torque).
–
Left rotation: For loosening bolts and nuts, turn the ro-
tational direction switch
4
in an anticlockwise direction.
0 607 450 615/... 616/... 618/... 619
–
Right rotation: For screwing in bolts and nuts, turn the
rotational direction switch
4
in an anticlockwise direc-
tion to 1 (lowest torque), 2 or to the stop to 3 (highest
torque).
–
Left rotation: For loosening bolts and nuts, turn the ro-
tational direction switch
4
in a clockwise direction.
Switching On and Off
To save energy, only switch the pneumatic tool on when you
are using it.
Note:
When the pneumatic tool does not start, for example af-
ter a longer rest period, disconnect the air supply, and turn
the motor by the tool holder
10
several times through. This re-
moves the adhesive forces.
– To
switch on
the pneumatic tool, press the On/Off switch
9
.
– To
switch off
the pneumatic tool, release the On/Off
switch
9
.
Note:
The required torque adjustment and the duration of the
driving-in procedure depend on the type of screw connection
and can be best determined by practical trials. Check the trial
screwings with an electronic torque measurer or a torque
wrench. Once the optimal torque setting and driving-in dura-
tion are determined, you should always press the On/Off switch
9
for the same duration for the same driving-in procedures.
Working Advice
Place the application tool onto the nut/screw only
when the screwdriver is switched off.
Rotating applica-
tion tools can slide off the nut/screw.
In case of an interruption of the air supply or reduced
operating pressure, switch the pneumatic tool off.
Check the operating pressure and start again when the op-
erating pressure is optimal.
Sudden loads cause a sharp drop in speed or a complete stop,
yet do not cause damage to the motor.
Maintenance and Service
Maintenance and Cleaning
Have maintenance and repair work carried out only
through qualified persons.
This will ensure that the safe-
ty of the pneumatic tool is maintained.
After each service, check the speed with a speed-measuring
device and check the pneumatic tool for increased vibrations.
An authorized Bosch after-sales service agent will carry out
this work quickly and reliably.
Use only original Bosch spare parts.
Regular Cleaning (see figure C)
– Clean the sieve at the air intake of the pneumatic tool regu-
larly. For this, unscrew the hose fitting
7
and remove any
dust and debris from the sieve. Afterwards, retighten the
hose fitting again.
Water and debris particles in the compressed
air cause rust and lead to wear of plates, valves
etc. To prevent this, fill several drops of engine
oil into the air intake
5
. Reconnect the pneu-
matic tool to the air supply (see “Connecting
the Air Supply”, page 17) and run it for 5 –10 seconds, while
catching/picking up the escaping oil with a cloth.
Always car-
ry out this procedure when not using the pneumatic tool
for a longer period of time.
Scheduled Maintenance
The motor plates should be checked regularly by specialised
personnel and replaced, if required.
Lubricating the Pneumatic Tool
For direct lubrication of the pneumatic tool or admixtures to
the service unit, use SAE 10 or SAE 20 engine oil.
After approximately 100,000 screwing operations, the strik-
ing mechanism must be relubricated. For this, turn the impact
wrench so that the handle faces upward. Unscrew the locking
screw
15
in an anticlockwise direction using a suitable Allen
key (see “Technical Data”). Drain the waste oil in an environ-
mental-friendly manner. Fill engine oil into the striking mech-
anism through the opening of the locking screw. The quantity
of engine oil to be refilled can be found in the chart row on en-
gine oil (see “Technical Data”). Remove any excess oil using a
soft cloth. Screw in the locking screw
15
in a clockwise direc-
tion and tighten.
Lubrication of Pneumatic Tools that do not belong to the
CLEAN Product Line
For all Bosch pneumatic tools that do not belong to the CLEAN
product line (these have a special type of compressed-air motor
that functions with oil-free compressed air), oil mist should be
added continuously to the flowing-through compressed air. The
compressed-air oiler required for this is included in the com-
pressed-air service unit on the line side of the pneumatic tool (for
more details, please refer to the compressor manufacturer).
Accessories
For more information on the complete quality accessories
program, please refer to the Internet under
www.bosch-pt.com or contact your specialist shop.
After-sales Service and Application Service
In all correspondence and spare parts orders, please always
include the 10-digit article number given on the type plate of
the pneumatic tool.
Our after-sales service responds to your questions concern-
ing maintenance and repair of your product as well as spare
parts. Exploded views and information on spare parts can al-
so be found under:
www.bosch-pt.com
Bosch’s application service team will gladly answer questions
concerning our products and their accessories.
OBJ_BUCH-275-003.book Page 18 Friday, December 6, 2013 3:12 PM