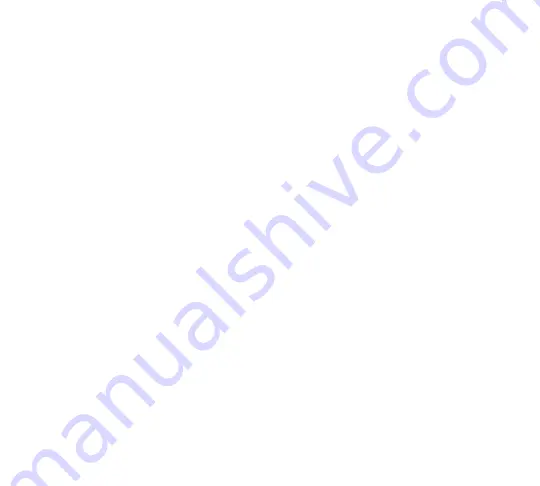
1.3
AC Line Fusing –
It is recommended that a fuse(s) or circuit breaker be installed in the AC
line. Fuse each conductor that is not at ground potential. For the recommended fuse size, see
Table 1, on page 14. Also see Section 10, on page 35.
1.4
Motor Connection –
Wire the motor to quick-connect Terminals “U”, “V”, “W”, as shown in
Figure 16, on page 31. (Special reactors may be required for cable lengths over 100 ft. (30 m)
– consult our Sales Department.) See Section 9.3, on page 31.
Note:
The drive is programmed to operate 3-phase AC induction motors. For PSC motors,
optional software is required – contact our Sales Department.
1.5
60 Hz and 50 Hz Motor Operation (Jumpers J1 and J2 On the Lower PC Board) –
The
drive is factory set for 60 Hz motor operation (Jumper J1 set to the “60Hz” position and
Jumper J2 set to the “X1” position). For 50 Hz motor operation, set Jumper J1 to the “50Hz”
position and be sure Jumper J2 is set to the “X1” position. See Section 6.2.1, on page 26.
1.6
Trimpot Settings –
All trimpots have been factory set for most applications, as shown in
Figure 4, on page 20. Some applications require adjustment of the trimpots in order to tailor
the drive for a specific requirement. See Section 13, on pages 38 – 43.
1.7
Main Speed Potentiometer Connection –
For unidirectional speed operation, wire the 5 k
Ω
potentiometer (supplied) to Terminals “P1” (low), “P2” (wiper), “P3” (high). See Section 9.4, on
pages 31 and 32.
1.8
Voltage Following –
An
isolated*
0 – 5 Volt DC analog signal input can be used to control
motor speed in lieu of the Main Speed Potentiometer. The drive output will linearly follow the
analog signal input. Connect the signal input positive lead (+) to Terminal “P2” and the nega-
tive lead (–) to Terminal “P1”. See Section 9.5, on pages 32 and 33.
*If a non-isolated signal is used, install the SIVFR — Signal Isolator. The SIVFR accepts volt-
age (0 to ±2.5 thru 0 to ±25 Volts DC) or current (4 – 20 mA DC) signal inputs. See Section
3.5, on page 13.
7