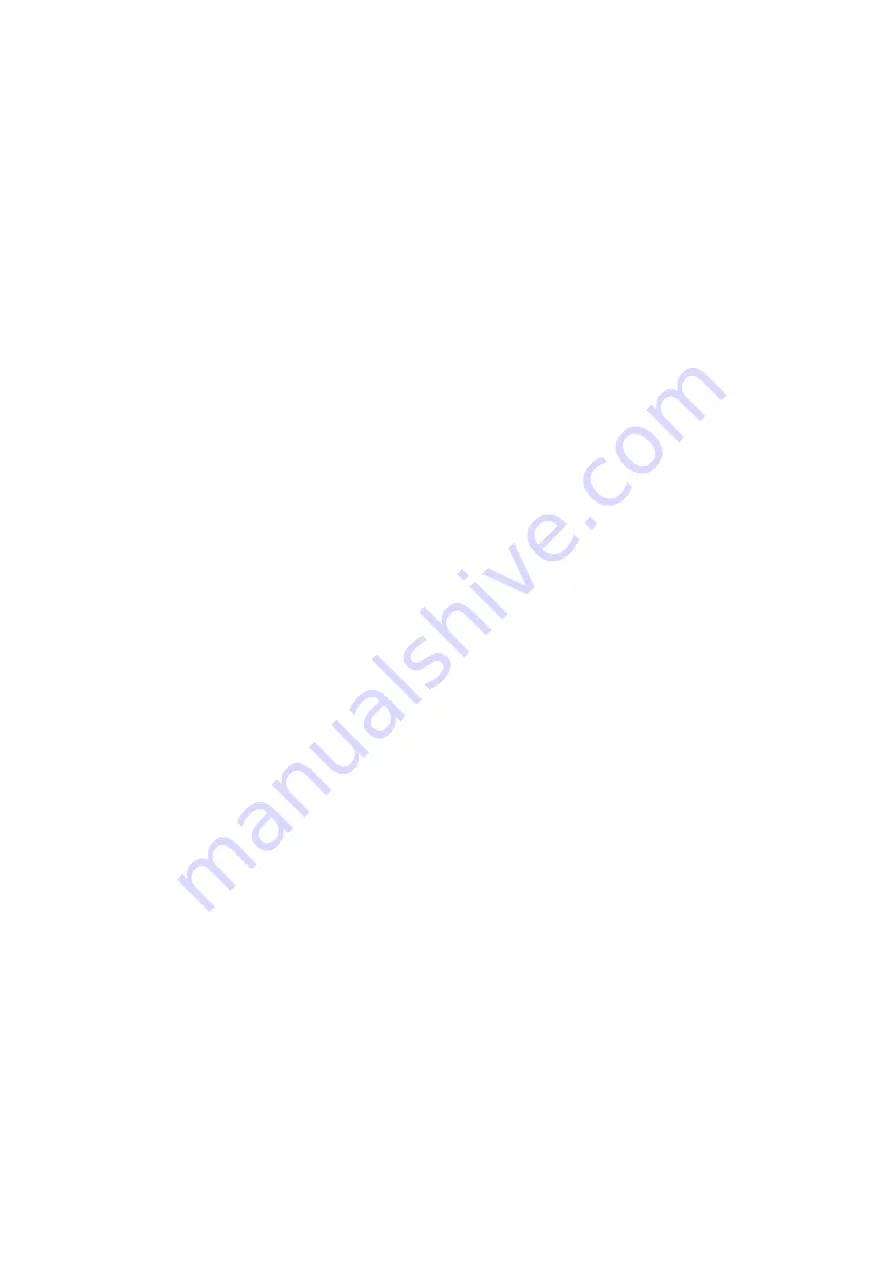
Page
6
of
37
Blueprint Lab Confidential Proprietary Information not to be reproduced or made available to third parties without prior consent from
Blueprint Lab and not to be used in any unauthorised way. © Blueprint Lab Pty Ltd 2021
Any additional rectification work required will be assessed and quoted during the servicing process.
1.6 OBSTACLE SETUP
Ensure that the manipulator is setup correctly using the bench test and platform integration procedures shown
elsewhere in this manual. In particular, care should be taken to ensure that permanent obstacles in the
workspace are correctly defined to avoid collision between the manipulator and other equipment. The
manipulator arrives with a ‘floor’ obstacle installed to avoid collision with the bench/test platform.
1.7 EMERGANCY STOP
It is strongly recommended that an ESTOP button is included in the power circuit when bench level testing the
manipulator. Additionally, a digital ESTOP is included in the Reach Control software.
1.8 ELECTRICAL INSTALLATION
For bench level testing, it is strongly recommended to use a controlled power supply with a current limiting
circuit and/or a Residual Current Device (RCD) mechanism.
1.9 PHYSICAL INSTALLATION
Prior to operation, ensure that the manipulator is firmly secured using the supplied mounting kit, or an
alternative solution with the appropriate specifications.
1.10 OPERATING ENVIRONMENT
1.10.1 OPERATING AND STORAGE TEMPERATURE
The manipulator system is specified for use from -10°C to 40°C (operating) and up to 80°C storage.
1.10.2 PRESSURE
The Reach Bravo is Depth Rated to operate at the equivalent of 300MSW.
1.10.3 EXPLOSIVE ENVIRONMENTS
Reach Bravo manipulators are not designed to meet explosion-proof specifications. Do not use the robot and
controller in environments containing inflammable gas, gasoline or solvent. Explosions or fire may otherwise
result.