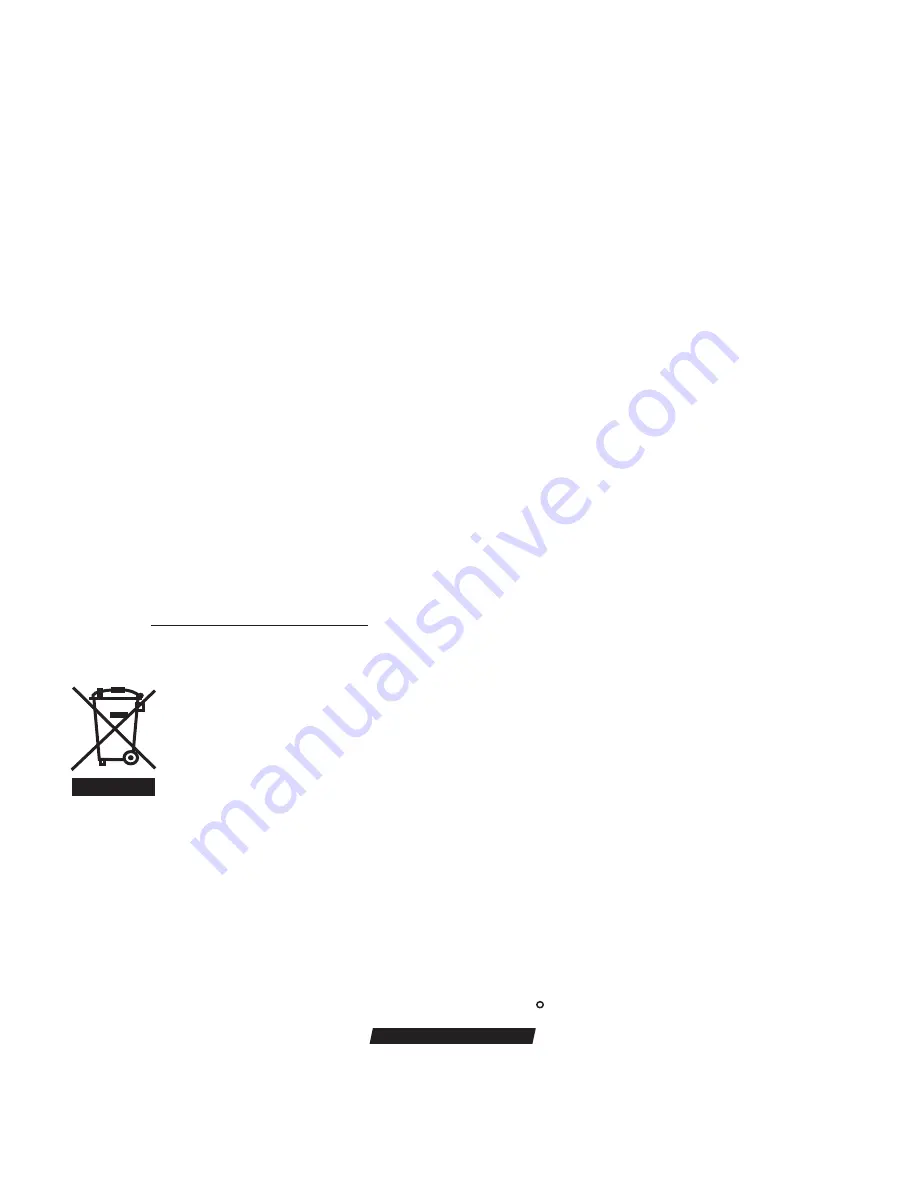
LIMITED WARRANTY
Your new Flex-Pro pump is a quality product and is warranted for 24 months from date of purchase (proof of purchase is required). The
pump will be repaired or replaced at our discretion. Pump Head and roller assembly is warrantied against damage from chemical
attack when proper TFD (Tube Failure Detection) system instructions and maintenance procedures are followed.
WHAT IS NOT COVERED
•
Pump Tube Assemblies and rubber components – They are perishable and require periodic replacement.
•
Pump removal, or re-installation, and any related labor charge.
•
Freight to the factory, or ProSeries service center.
•
Pumps that have been tampered with, or in pieces.
•
Damage to the pump that results from misuse, carelessness such as chemical spills on the enclosure, abuse, lack of
maintenance, or alteration which is out of our control.
•
Pumps damaged by faulty wiring, power surges or acts of nature.
Blue-White Industries does not assume responsibility for any loss, damage, or expense directly or indirectly related to or arising out of
the use of its products. Failure must have occurred due to defect in material or workmanship and not as a result of operation of the
product other than in normal operation as defined in the pump manual.
Warranty status is determined by the pump's serial label and the sales invoice or receipt. The serial label must be on the pump and
legible. The warranty status of the pump will be verified by Blue-White or a factory authorized service center.
OTHER IMPORTANT WARRANTY INFORMATION
Please be advised; injection and metering devices are not intended as a means of treating water to render it suitable for human
consumption. When used as hypochlorinators, they are meant to destroy bacteria and algae contamination, before its removal by
filtration. Acid and soda injectors are used for PH control (balance). Blue-White injectors are factory tested with water only for pressure
and performance. Installers and operators of these devices must be well informed and aware of the precautions to be taken when
injecting various chemicals -especially those considered hazardous or dangerous, eye protection must be worn when working around
this product or any other metering type of pump.
Should it become necessary to return the pump for repair or service, you must attach information regarding the chemical used as some
residue may be present within the unit which could be a hazard to service personnel.
Blue-White Industries will not be liable for any damage that may result by the use of chemicals with their injectors and its components.
Thank you.
PROCEDURE FOR IN WARRANTY REPAIR
Contact the factory to obtain a RMA (Return Material Authorization) number. Carefully pack the pump to be repaired. It is recommended
to include foot strainer and injection/check valve fitting since these devices may be clogged and part of the problem. Please enclose a
brief description of the problem as well as the original invoice or sales receipt, or copy showing the date of purchase. Prepay all
shipping costs. COD shipments will not be accepted. Warranty service must be performed by the factory or an authorized ProSeries
service center. Damage caused by improper packaging is the responsibility of the sender. When In-Warranty repair or replacement is
completed, the factory pays for return shipping to the dealer or customer.
Users of electrical and electronic equipment (EEE) with the WEEE marking per Annex IV of the WEEE Directive must not
dispose of end of life EEE as unsorted municipal waste, but use the collection framework available to them for the return,
recycle, recovery of WEEE and minimize any potential effects of EEE on the environment and human health due to the
presence of hazardous substances. The WEEE marking applies only to countries within the European Union (EU) and Norway.
Appliances are labeled in accordance with European Directive 2002/96/EC.
Contact your local waste recovery agency for a
Designated Collection Facility
in your area.
P.N. 80000-419
Rev. 41 20210309
5300 Business Drive, Huntington Beach, CA 92649 USA
Phone:
714-893-8529
FAX:
714-894-9492
E mail:
or
URL:
www.blue-white.com
ProSeries
by Blue-White Ind.
TMR