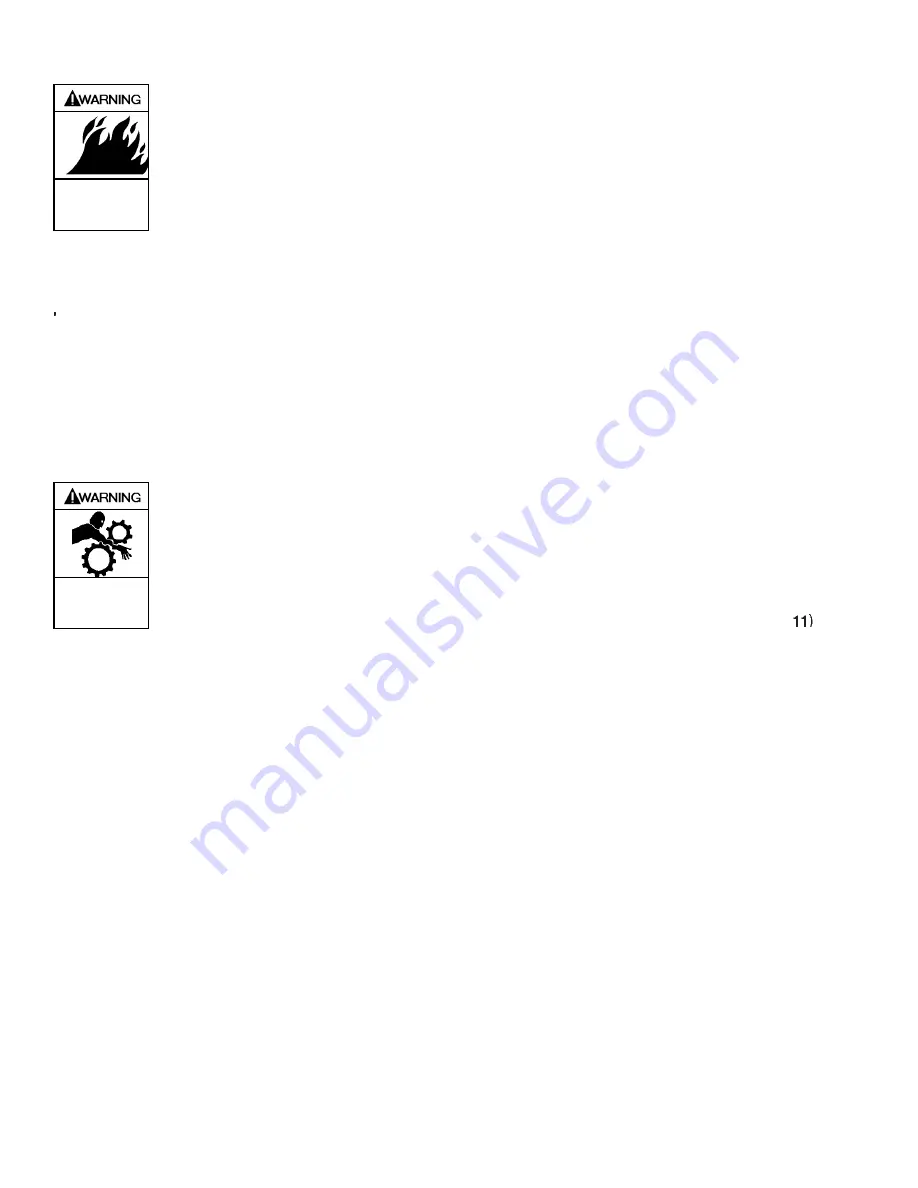
1301-C00 page 16/56
Install Mechanical Seal
See mechanical seal instructions.
Never operate the pump without liquid
supplied to the mechanical seal.
Running the mechanical seal dry, even
for short periods, can cause seal
damage and/or failure. Physical injury
can occur if mechanical seal fails.
Hazardous fluids can
cause fire, serious
personal injury or
property damage.
Lubricate the shaft with silicone lubricant. Slide the mechanical
seal assembly, including all O-rings and gaskets, over the
shaft (6).
Install Back Cover
1. Slide the back cover assembly (11) over the shaft and
fasten it to the frame adapter (71) with 2 nuts for Frame
SD, S, Frame A 8 in. and 10 in., and Frame M.
The Frame A 13 in. back cover requires 8 nuts.
Be sure to remove any paint or debris from the OD of the
frame adapter ring.
2. Lightly tighten the mechanical seal gland nuts. These will
be snugged later.
Install Impeller
Wear heavy work gloves when handling
impellers as sharp edges may cause
physical injury.
Hazardous
machinery can
cause serious
personal injury.
Treat the impeller thread with nickel anti-seize before
assembly to prevent galling. Fasten the impeller (2) with PTFE
O-ring (38) to the shaft (6).
Make sure the impeller hub is fastened hand-tight against
the shaft shoulder.
Apply silicone grease to the impeller hub if the pump is an
LD17 where the mechanical seal O-ring rides on the impeller
hub.
Install Casing
1. Mount the casing (1) to the frame adapter (71). Be sure to
insert the gasket (73A) between the casing (1) and the
back cover (11). Tighten the casing studs in a crisscross
pattern.
2. The 13 in. Frame A/LD17 casing bolts directly to the back
cover.
3. Install both feet on the Frame A casing.
4. Mount the entire pump assembly onto the baseplate and
securely fasten all the hold down bolts.
5. Attach the suction and discharge piping to the casing (1)
while ensuring no strain is imparted to the pump.
NOTE:
The vortex pump has a separate suction cover that can be
replaced if necessary.
4.3 Impeller Total Clearance
See Pump Assembly Drawings section 8.0.
It is important to determine whether there is sufficient total
impeller clearance within the assembled wet end which
includes the casing (1), impeller (2), back cover (11), and
suction cover, if applicable.
This procedure is not necessary for the vortex pumps.
1. Loosen all three (Frame SD, S A), or four (Frame M)
micrometer nuts (66) and lock nuts (404).
2. Tighten the cartridge lock nuts (404) alternately until the
impeller (2) just begins to scrape the suction side of the
casing (1). By turning the shaft (6) manually, clockwise
facing the coupling, you will hear the impeller scrape the
casing bowl. Turn the shaft (6) clockwise only and in
complete revolutions between adjustments.
3. Tighten the micrometer nuts (66) alternately, so that they
are flush against the cartridge (33). Back off the lock nuts.
(404).
4. Turn the micrometer nuts (66) alternately, counting the
number of radial lines moving along a fixed point on the
cartridge flange. By turning the set of micrometer nuts (66)
from one radial line to the next, the impeller (2) will move
away from the suction side of the casing (1) by 0.003 in.
(0.08 mm). Continue to do this while rotating the shaft (6)
clockwise until the back of the impeller (2) begins to rub
the back cover (11).
5. Use the following equation to find the total clearance:
No. of radial lines x 0.003 in. (0.08 mm)
= total clearance
The total clearance should fall between .
0.040 in. -0.070 in. (1.02 mm -1.78 mm).
6. If the total clearance needs to be adjusted, proceed as
follows:
Change the thickness of the casing gasket (73A) that is
located between the casing (1) and the back cover (
).
Increasing the gasket thickness will increase the total
clearance. If no thicker gasket is on-hand, a second
gasket may be installed.
4.4 Impeller Operating Clearance
See Pump Assembly Drawings section 8.0.
The impeller operating clearance is the gap between the
impeller blades and the casing bowl. This gap is important in
achieving proper performance from the pump.
After the total impeller clearance has been established, set the
impeller operating clearance within the pump wet end
assembly as follows:
1. Loosen the micrometer nuts (66). For vortex pumps,
loosen the cartridge lock nuts (404).
2. Tighten the cartridge lock nuts (404) alternately until the
impeller (2) just begins to scrape the casing (1) bowl.
Manually turn the shaft (6) clockwise (from coupling end)
a complete revolution between adjustments and listen for
a scraping sound.
NOTE:
For vortex pumps, the impeller is set off the back cover.
Tighten the micrometer nuts evenly until the impeller back
vanes just begin to scrape the back cover. The shaft position
is set to the opposite face from the standard centrifugal pump
instructions indicated above.
3. Tighten the micrometer nuts (66) alternately so that they
are flush against the cartridge. Back off the three lock nuts
(404) by at least 0.12 in. (3 mm).
NOTE:
For vortex pumps, tighten the cartridge lock nuts (404).
Содержание SYSTEM ONE
Страница 26: ...1301 C00 page 25 56 8 0 PUMP ASSEMBLY DRAWINGS AND PARTS LIST 8 1 Pump Assembly Parts List Frame SD Horizontal ...
Страница 27: ...1301 C00 page 26 56 8 2 Pump Assembly Parts List Frame S Horizontal 6 1 ...
Страница 28: ...1301 C00 page 27 56 8 3 Pump Assembly Parts List Frame S Horizontal 8 ...
Страница 29: ...1301 C00 page 28 56 8 4 Pump Assembly Parts List Frame A and IPP Frame A ...
Страница 30: ...1301 C00 page 29 56 8 5 Pump Assembly Parts List LD17 and IPP LD17 ...
Страница 31: ...1301 C00 page 30 56 8 6 Pump Assembly Parts List Vortex Frame A and IPP Vortex Frame A ...
Страница 32: ...1301 C00 page 31 56 8 7 Pump Assembly Parts List Vortex LD17 and IPP Vortex LD17 ...
Страница 33: ...1301 C00 page 32 56 8 8 Pump Assembly Parts List Frame M ...
Страница 55: ...1301 C00 Page 54 56 notes ...
Страница 56: ...1301 C00 Page 55 56 notes ...