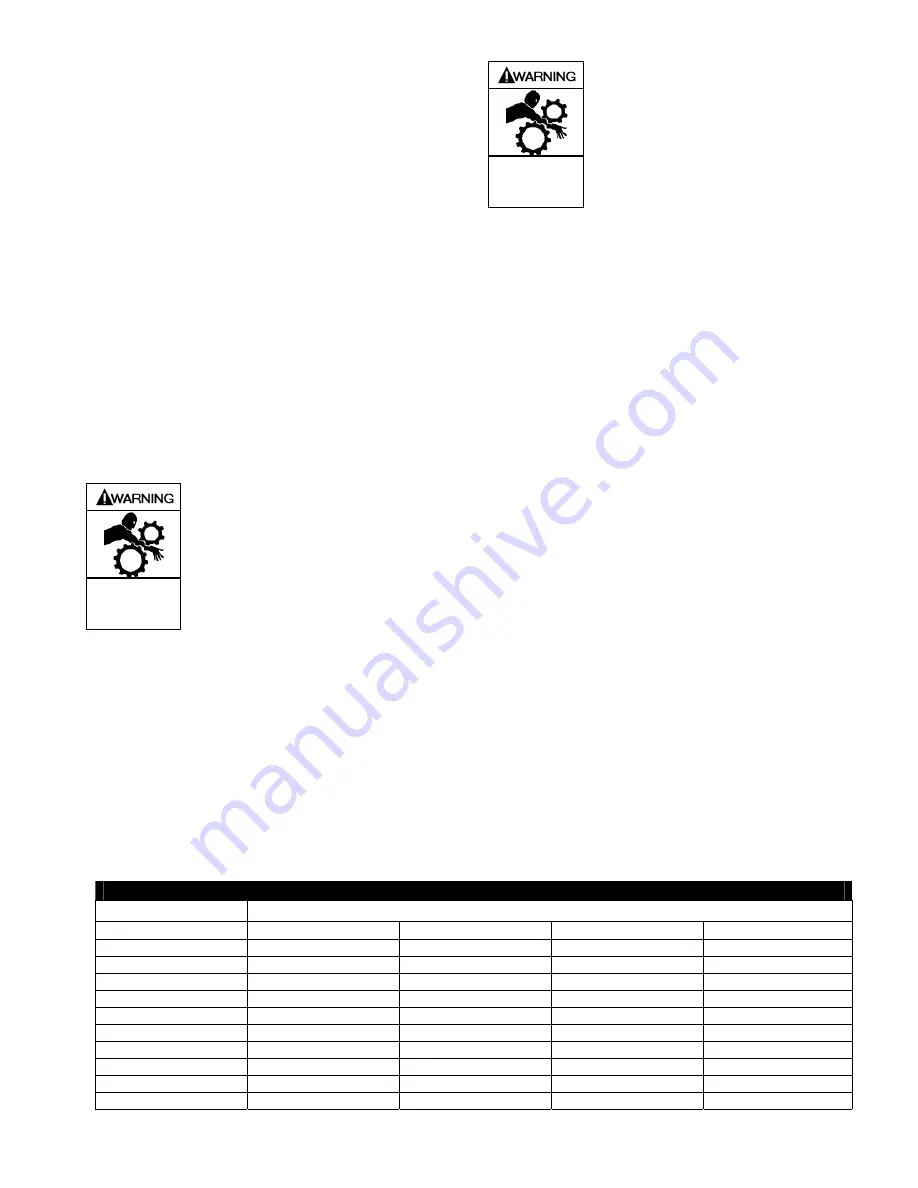
1301-C00 page 11/56
Seal Chamber
A water jacketed seal chamber is available for Frame SD, S,
A, and M pumps. The requirements for the jacket are based on
the type of mechanical seal and selection of elastomers.
Normally, a jacket should be considered for any application
over 350°F (177°C). Please consult the factory for specific
recommendations.
When a jacket is installed, ambient temperature water at 2 - 3
gallons per minute (0.45 to 0.68 m3/hr) will be required for
proper cooling of the seal chamber.
The cooling water must be turned on before the hot process
fluid is allowed to enter the pump.
Mechanical Seal
The seals may be cooled/heated from an external source or by
passing pump discharge fluid through a heat exchanger and
then into the seal flush connection.
A double seal may use cooled/heated barrier fluid from an
external source or convection system. Always follow seal
operating instructions as required by the instruction booklet
provided with the seal.
3.0 OPERATION
3.1 Operating Parameters and Limits
Never run the pump outside of the
operating limits as property damage or
physical injury could result.
Hazardous
machinery can
cause serious
personal injury.
1.
Shaft Speed:
3600 RPM maximum, except Frame M
which is limited to 1800 RPM maximum.
2.
Power Input
: Maximum allowable input power is shown in
Section 2.1 and is based on frame size and shaft material.
3.
Pressure —Temperature Limits:
The following table
shows maximum allowable pressures (gage) for given
temperatures and wet end materials. Values occurring
between those shown may be interpolated. At no time
should temperatures exceed 400°C (750°F).
4.
Sound level:
85 dBA maximum located 3ft (1 m) in front
of the pump and 5 ft (1.6 m) above the floor.
3.2 Start-Up Inspection
Lock-out driver to prevent accidental
start-up and physical injury.
Hazardous
machinery can
cause serious
personal injury.
1. Check Installation. Make certain the entire pump is
properly aligned, and all auxiliary systems are connected
and ready for implementation.
2. Check Direction of Rotation.
NOTICE:
Improper direction of pump rotation will damage the
pump.
When checking for proper direction of rotation, the
coupling must be completely disconnected from the pump
and driver. Run the driver independently to check for
proper direction of rotation. Direction of the pump rotation
is clockwise when viewed from the coupling end and is
indicated by an arrow on the front of the casing.
Once direction of rotation is confirmed, reconnect coupling
and confirm alignment.
3. Check Impeller Clearance.
NOTICE:
Pump units have impeller clearance pre-set prior to
shipment from factory.
NOTICE:
Setting impeller clearance is important for
maintaining maximum pump efficiency. For high
temperature applications, compensation for
additional thermal growth must be made.
Set impeller clearance.
a. Unfasten the mechanical seal from the shaft when
making adjustments.
b. Check total clearance and make certain it conforms
to the instructions given. (section 4.3).
c. Set the proper operating clearance on the suction
side of impeller (except Vortex type which is set off
the back cover). (section 4.4).
If the pumpage temperature, exceeds 100°F (38°C)
increase the clearance on the suction side of the impeller
per section 4.4 of this manual.
Pressure — Temperature Limits
Temperature
PRESSURE
Psig (Bar)
°F (°C)
D. I.
316 SS
CD4MCu
Alloy 20
-20 (-29)
250 (17.2)
275 (19.0)
290 (20)
230 (15.9)
100 (38)
250 (17.2)
275 (19.0)
290 (20)
230 (15.9)
200 (93)
235 (16.2)
235 (16.2)
260 (17.9)
200 (13.8)
300 (149)
215 (14.8)
215 (14.8)
230 (15.9)
180 (12.4)
400 (204)
200 (13.8)
200 (13.8)
200 (13.8)
160 (11.0)
500 (260)
170 (11.7)
170 (11.7)
170 (11.7)
150 (10.3)
600 (315)
140 (9.7)
140 (9.7)
140 (9.7)
140 (9.7)
650 (343)
125 (8.6)
125 (8.6)
125 (8.6)
DO NOT USE
700 (371)
DO NOT USE
110 (7.6)
110 (7.6)
DO NOT USE
750 (400)
DO NOT USE
95 (6.6)
95 (6.6)
DO NOT USE
Содержание SYSTEM ONE
Страница 26: ...1301 C00 page 25 56 8 0 PUMP ASSEMBLY DRAWINGS AND PARTS LIST 8 1 Pump Assembly Parts List Frame SD Horizontal ...
Страница 27: ...1301 C00 page 26 56 8 2 Pump Assembly Parts List Frame S Horizontal 6 1 ...
Страница 28: ...1301 C00 page 27 56 8 3 Pump Assembly Parts List Frame S Horizontal 8 ...
Страница 29: ...1301 C00 page 28 56 8 4 Pump Assembly Parts List Frame A and IPP Frame A ...
Страница 30: ...1301 C00 page 29 56 8 5 Pump Assembly Parts List LD17 and IPP LD17 ...
Страница 31: ...1301 C00 page 30 56 8 6 Pump Assembly Parts List Vortex Frame A and IPP Vortex Frame A ...
Страница 32: ...1301 C00 page 31 56 8 7 Pump Assembly Parts List Vortex LD17 and IPP Vortex LD17 ...
Страница 33: ...1301 C00 page 32 56 8 8 Pump Assembly Parts List Frame M ...
Страница 55: ...1301 C00 Page 54 56 notes ...
Страница 56: ...1301 C00 Page 55 56 notes ...