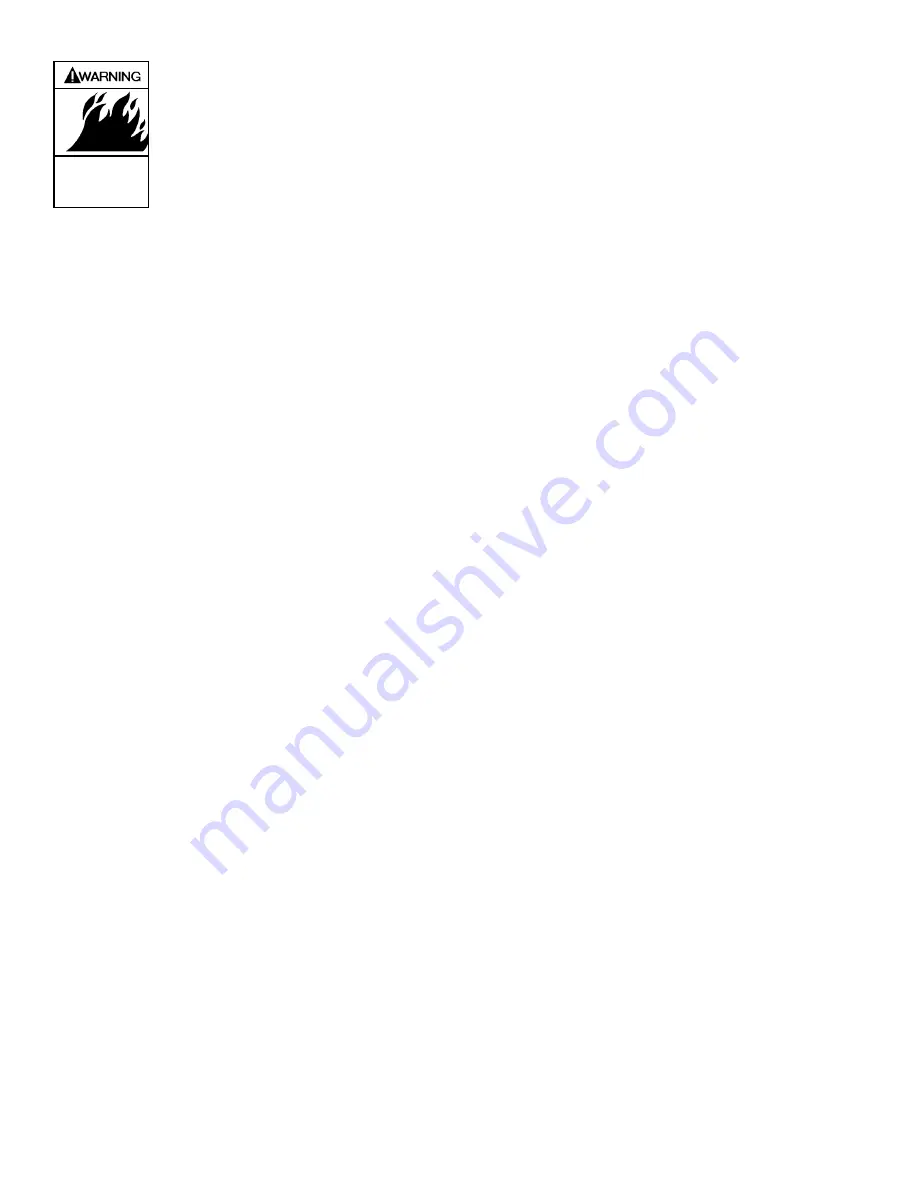
1301-C00 page 10/56
2.7 Mechanical Seal
Never operate the pump without liquid
supplied to the mechanical seal.
Running the mechanical seal dry, even
for short periods, can cause seal
damage and/or failure. Physical injury
can occur if mechanical seal fails.
Hazardous fluids can
cause fire, serious
personal injury or
property damage.
The mechanical seal is flushed and cooled by either the
pumped fluid or an external source. If the mechanical seal is
flushed from an external source, it is required that the media
be clean, solid free, and compatible to the pumped fluid.
Quench, vent, and/or drain ports are available on some seals.
Ensure proper connections are made when the application
requires it. Always follow all instructions provided with the seal
Prior to pump operation:
1. Be sure all set screws are tightened to the shaft.
2. Check that all centering clips are removed.
3. Ensure that all required mechanical seal auxiliary systems
are installed and properly connected.
Seal life is dependent on a number of factors including
cleanliness of process, operating conditions, etc. As such it is
difficult to predict actual seal life for a given application.
2.8 Lubrication
Bearing Oil Lube
The pump bearing frame must be filled with a high quality, anti-
foaming turbine oil containing rust and oxidation inhibitors.
Bearing temperatures should not exceed 180° F (82° C) thus
an ISO VG 68 oil should be used.
Some recommended oils are:
Texaco Regal R + O NO. 68
Mobil DTE Heavy Medium
Shell Turbo NO. T68
Shell Omala 68
Royal Purple Synfilm ISO VG 68 (synthetic)
The oil should be changed every 12 months with more
frequent changes under severe environmental conditions, such
as dust, moisture and corrosive atmospheres.
Lubricating Oil Properties:
ISO GRADE.VG ......................................................... 68
Approximate SSU at 100°F (40°C) ........................... 300
300 Kinematic Viscosity at 100°F (40°C) (cSt). ........... 68
Oil Level
The oil level in the bearing frame should be one-half (1/2) of
the way up the oil sight glass with the unit not operating.
If there is a slight loss of oil through the labryinth
seals:
1. Lower the oil level to approximately 1/3 sight glass height.
2. Check that the pump bearing frame is level.
3. Check that oil return groove in cartridge is at 6 o’clock
(“blackmer” should be across the top at 12 o’clock).
4. Check that radial labyrinth seal stator drain is at 6 o’clock
(Frame A and M only).
Bearing Frame Oil Volumes:
Frame SD
0.45 quarts (430 ml)
Frame S
0.22 quarts (208 ml)
Frame A
0.74 - 0.79 quarts (700 - 748 ml)
Frame M
1.26 - 1.34 quarts (1192 - 1268 ml)
Bearing Grease Lube
Use a premium quality lithium grease, having an NLGI 2 or 3
consistency and a base oil viscosity of 68 centistokes
minimum at 40°C. When reassembling a pump, the bearings
are best pre-greased after assembly onto the shaft. The
bearings should be packed full with grease and the bearing
housing adjacent to the bearings packed one third to one half
full.
NOTICE:
Never mix greases of different consistencies.
Please note that vertical pumps are all grease lubed and that
bearings are greased at the factory, thus no additional grease
at installation is required.
Some recommended greases are:
Chesterton #615
SKF LGMT2/LGMT3
Re-greasing Intervals:
For back to back angular contact, single and double row
bearings, add several shots of grease from a grease gun at
following intervals.
At 950 RPM, add grease every 5500 hours.
At 1180 RPM, add grease every 5000 hours.
At 1450 RPM, add grease every 5000 hours.
At 1750 RPM, add grease every 4000 hours.
At 2950 RPM, add grease every 3000 hours.
At 3550 RPM, add grease every 1250 hours.
At bearing temperatures above 150°F (66°C), the bearings
require re-greasing more often. Greasing intervals should be
halved for every 27°F (15°C) increase. Maximum grease
temperature should not exceed 185°F (85°C). Completely
replace the grease at every third re-greasing interval, or once
a year minimum.
NOTICE:
Over greasing is the most common cause of bearing
overheating and will contribute to premature bearing
failure.
Coupling Lubrication
The pump coupling may or may not require lubrication. For
information on lubrication, refer to the coupling manufacturer’s
instructions.
2.9 Temperature Control
NOTICE:
Normal operating oil temperature should be below
160°F (71°C) and should never exceed 180°F (82°C).
Bearing Frame
Bearing cooling may be needed to keep surface temperatures
within required temperature ratings.
Water cooling of the bearing frame is accomplished with the
optional cooling coil. The cooling coil is required only when the
pumped media temperature exceeds 400°F (204°C) at 1800
rpm or 300°F (149°C) at 3600 rpm. Under these conditions,
ambient temperature water at 1 - 3 gallons per minute (0.23 to
0.68 m3/hr) will be required for proper cooling of the oil. Higher
flows may be required to keep the oil temperature below the
maximum recommended.
The cooling water must be turned on before the hot process
fluid is allowed to enter the pump.
The optional System One Oil Temperature Monitor is
recommended for all applications, especially for high
temperature.
Содержание SYSTEM ONE
Страница 26: ...1301 C00 page 25 56 8 0 PUMP ASSEMBLY DRAWINGS AND PARTS LIST 8 1 Pump Assembly Parts List Frame SD Horizontal ...
Страница 27: ...1301 C00 page 26 56 8 2 Pump Assembly Parts List Frame S Horizontal 6 1 ...
Страница 28: ...1301 C00 page 27 56 8 3 Pump Assembly Parts List Frame S Horizontal 8 ...
Страница 29: ...1301 C00 page 28 56 8 4 Pump Assembly Parts List Frame A and IPP Frame A ...
Страница 30: ...1301 C00 page 29 56 8 5 Pump Assembly Parts List LD17 and IPP LD17 ...
Страница 31: ...1301 C00 page 30 56 8 6 Pump Assembly Parts List Vortex Frame A and IPP Vortex Frame A ...
Страница 32: ...1301 C00 page 31 56 8 7 Pump Assembly Parts List Vortex LD17 and IPP Vortex LD17 ...
Страница 33: ...1301 C00 page 32 56 8 8 Pump Assembly Parts List Frame M ...
Страница 55: ...1301 C00 Page 54 56 notes ...
Страница 56: ...1301 C00 Page 55 56 notes ...