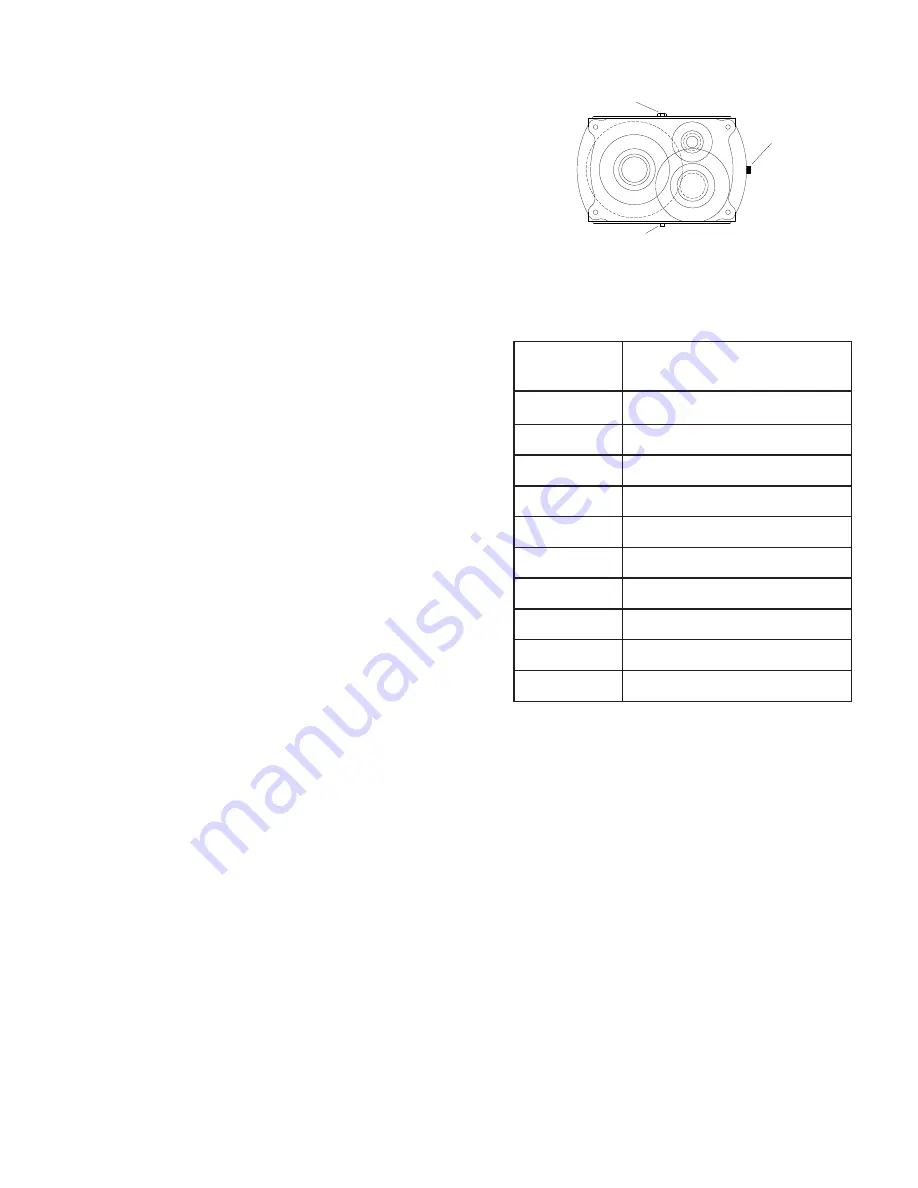
11
4. FOR DORRIS MIXER TRANSMISSION
(OBSOLETE -N/A) BEFORE SERIAL NO. 55665
DORRIS MIXER TRANSMISSION: Oil in the mixer
transmission should be changed after the first four (4) weeks
of operation. This is to remove the “run in” oil and also any
small metal shavings that may have been generated during
the initial mating of the gears. After the first oil change,
subsequent changes should be performed every six (6)
months. After draining the oil, refill the unit to the “level”
plug (1 qt.) at the center of the transmission with a
petroleum based rust and oxidation (R&O) inhibited gear
oil. Viscosity Range for 15-75° F (-9 - 24° C) is
AGMA Lube No. 3 or ISO Grade 100.
TO CHANGE OIL:
a. Unplug mixer/grinder from power source and perform
lockout/tagout procedures.
b. Remove rear drive cover.
c. Remove breather plug from top of transmission and oil
level plug from side of transmission.
d. With a container in place to catch old oil, remove the
magnetic drain plug from the bottom of the transmission.
e. When all oil has drained, clean the drain plug and
replace into the transmission.
f. Refill transmission with approx. one (1) quart of the
recommended gear oils or equivalent. Or until oil
appears at bottom of oil level sight hole.
g. Replace breather and oil level plugs.
h. Carefully turn mixer transmission pulley by hand to
lubricate internal gears.
i. Reinstall rear drive cover.
D. MIXER DRIVE BELT TENSION
1. Unplug mixer/grinder from power source and perform lockout/tagout procedures.
2. Remove rear drive cover.
3. Loosen the four bolts holding the 1HP motor to its mounting plate.
4. Slide 1HP motor away from mixer transmission.
5. When approximately
½” total belt flex has been attained, re-tighten motor bolts.
6. Reinstall rear drive cover.
E. MAIN DRIVE CHAIN AND SPROCKET LUBRICATION:
The main drive chain has been pre-lubricated at the factory to protect it against dirt and moisture. Chain life
will vary appreciably depending upon its lubrication. The better the lubrication, the longer the chain life.
Lubrication effectiveness will vary with the amount of lubricant and frequency of application. Ideally, a lubricant
film should always be present between the working parts. Manually lubricate the chain as often
as is needed
(possibly once a week).
NEVER
exceed three months without lubricating.
Lubricating just outside of the chain does little good. Apply lubrication on the inside of the chain span so that
it will work through the moving parts and joints by centrifugal force as the chain rotates and reach the area
where one surface “scrubs” another.
SUGGESTED POPULAR NAME BRANDS:
R & O GEAR OILS
(RUST & OXIDATION INHIBITED)
COMPANY
ISO VISCOSITY GRADE
100 (AGMA3)
AMOCO
American Ind’l Oil 100
CHEVRON
Machine Oil R & O ISO 100
CITGO
Pacemaker Oil 100
CONOCO
Dectol R & O Oil 100
EXXON
Teresstic 100
MOBIL
DTE Heavy
PHILLIPS
Magnus Oil ISO VG 100
SHELL
Morlina Oil 100
SUN
Sunvis 9100
TEXACO
Regal Oil R & O 100
BREATHER PLUG
MAGENTIC DRAIN PLUG
OIL
LEVEL
PLUG
Содержание AFMG-52
Страница 16: ...14 OPTIONAL EAGLE BELT DRIVE SYSTEM ...
Страница 28: ...26 TANDEM OPERATION ILLUSTRATION FOR 35 INLET ...
Страница 29: ...27 WIRING DIAGRAM ...