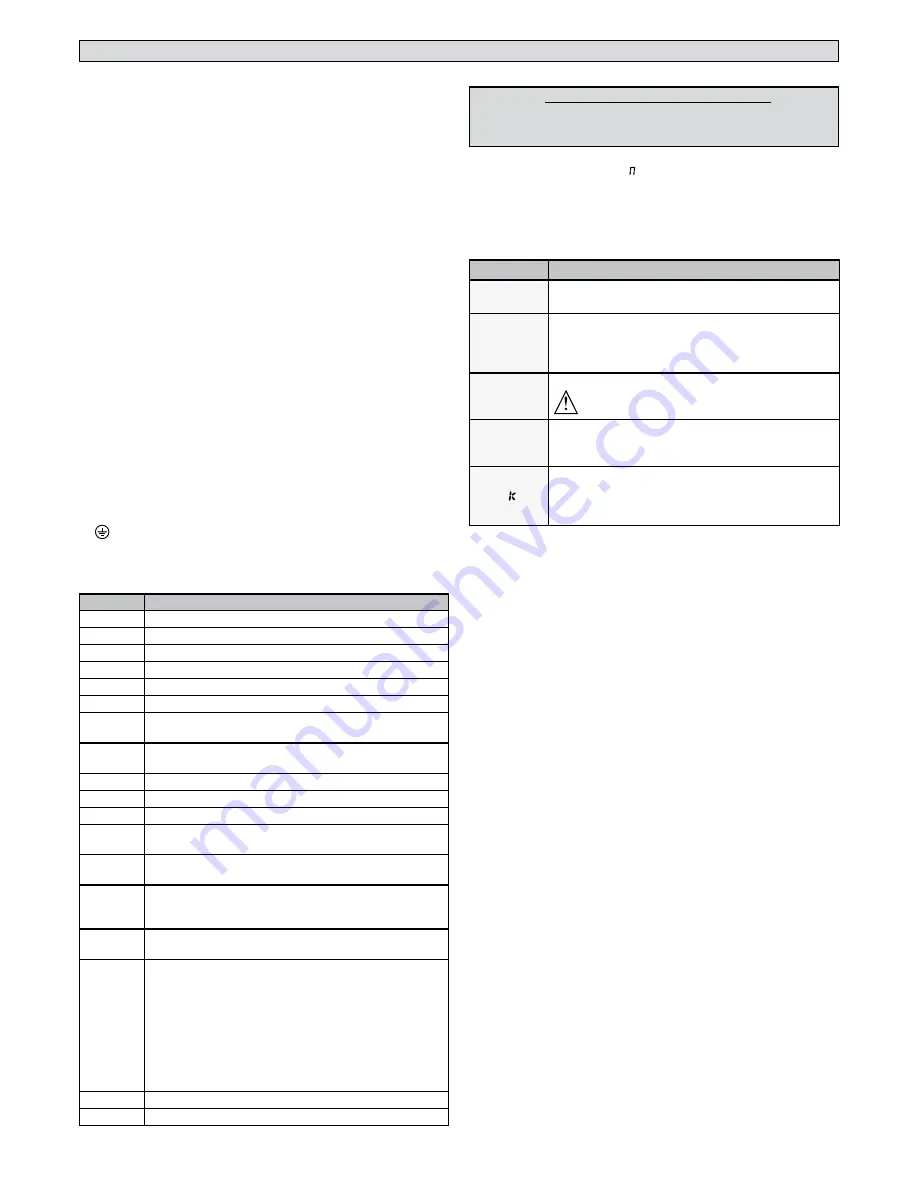
QR)
Control panel and incorporated receiver.
S)
Key selector.
AL)
Blinker
M)
Actuators.
A)
Bar.
F)
Rest fork.
CS)
Electric edge.
Ft,Fr) Pair of photocells.
CF)
Photocell post.
T)
1-2-4 channel transmitter.
RMM) Inductive metal mass detector.
LOOP) Mass detector loops.
11) CONNECTION (FIg. H-I)
WARNING: The electrical connections must be carried out workmanlike by
qualified experienced personnel, in conformity with all the current standards
and with the use of appropriate materials.
Lay out the electrical installation with reference to the current electrical
standards.
Keep the mains supply connections clearly separated from the service con-
nections.
In the initial section of the electrical installation, fit a circuit breaker with a
contact opening distance equal to or greater than 3,5 mm, provided with
magnetothermal protection and a differential switch having adequate capac-
ity for the appliance consumption. For the wiring, only use cables conforming
to the harmonised or national standards, having a cross section correspond-
ing to the initial protection, the appliance consumption and the installation
conditions, for example a 3x1.5 sq mm (H 05 VV-F) cable.
Proceed as explained below:
1. Remove the transformer cover.
2. Unscrew the screw which locks the cap (Fig. I Rif. 1) and take the cap out.
3. Fix the cables to the terminal bar (Fig. I Rif. 2)
L PHASE
N NEUTRAL
EARTH
4. To close the cap, reverse the actions in step 2.
5. Refit the transformer cover and secure in place by means of the slots
located on top of the transformer (Fig. I Rif. 3-4).
TERMINAL DESCRIPTION
1-2
Control for cooling fan
3-4
Not used
6-7
Motor connections
15-5
Motor connections, closing reference
15-8
Motor connections, opening reference
9-10
Blinker connection (24 V~, 25W)
11-12
24 V~ 180mA max output – power supply for photocells or
other devices (11+,12-).
13-14
24 V~ 180mA max output – power supply for photocell
transmitters with check (Vsafe 13+, 14-).
15-16
START button (N.O.)
15-17
STOP button (N.C.). If not used, leave the jumper bridged
15-18
Photocell input (N.C.). If not used, leave the jumper bridged
19
Photocell FAULT input (N.O.) for photocells provided with
N.O. check contact
15-20
Safety edge input (N.C.). If not used, leave the jumper
bridged
21-22
Barrier-open warning light output (N.O. contact, 24V~/ 3W max)
or, in alternative, alarm output (see configuration paragraph)
and Connection To Parky Car-Park Management System
23-24-
25-26
Encoder inputs
15-27
Open button (OPEN N.O.). If the TIMER logic on OPEN is enabled
and the input remains engaged for over 3 sec., it commutes
to clock input (TIMER N.O.).
The TIMER input opens and keeps the barrier open when
engaged; on disengagement, after waiting for the time set
in the Automatic Closing Time parameter, it starts the closing
movement (regardless of the TCA Logic status). If the com-
mand is interrupted by the STOP button being pressed or
by the safety devices being triggered, it can be reset using
the START input
15-28
Close button (CLOSE N.O.)
JP8-JP6
Board power supply (24V~) (JP8 +,JP6-)
12) ADJUSTMENTS
RECOMMENDED ADJUSTMENT SEQUENCE:
Adjusting the limit switches (See reference section) FIG.M
Programming remote controls (Fig. O)
Setting of parameters/logic, where necessary
13) PARAMETERS MENU (
para
)
(TABLE “A” PARAMETERS)
14) LOGIC MENU (
logic
)
(TABLE “B” LOGIC)
15) RADIO MENU (
RADIO
)
Logic
Description
add start
Add Start Key
associates the desired key with the Start command
read
Read
Checks a key of a receiver and, if memorized, returns the
number of the receiver in the memory location (from 01
to 64) and number of the key (T1-T2-T3 or T4).
erase 64
Erase List
WARNING! Erases all memorized remote controls
from the receiver’s memory.
cod RX
Read receiver code
Displays receiver code required for cloning remote
controls.
v
ON = Enables remote programming of cards via a previously me-
morized W LINK transmitter. It remains enabled for 3 minutes
from the time the W LINK remote control is last pressed.
OFF=W LINK programming disabled.
- IMPORTANT NOTE: THE FIRST TRANSMITTER MEMORIZED MUST BE
IDENTIFIED BY ATTACHING THE KEY LABEL (MASTER).
In the event of manual programming, the first transmitter assigns the RE-
CEIVER’S KEY CODE: this code is required to subsequently clone the radio
transmitters.
The Clonix built-in on-board receiver also has a number of important ad-
vanced features:
• Cloning of master transmitter (rolling code or fixed code)
• Cloning to replace transmitters already entered in receiver
• Transmitter database management
• Receiver community management
To use these advanced features, refer to the universal handheld programmer’s
instructions and to the CLONIX Programming Guide, which come with the
universal handheld programmer device.
16) LANGUAGE MENU (
language
)
Used to set the programmer’s language on the display.
17) DEFAULT MENU (
default
)
Restores the controller’s default factory settings.
18) CONNECTION TO PARKY CAR-PARK MANAGEMENT SYSTEM
The board can be configured in order to make an output available for con-
trolling the barrier status. When the SCA Alarm logic is disabled (OFF) and
the Alarm Time parameter is set to 0 s, the SCA contact (21-22) is configured
as follows (Fig. H Rif. 6):
- contact closed between terminals 21-22 with the barrier lowered
- contact open between terminals 21-22 with the barrier lifted
19) LIMIT SWITCH SETTING
WARNING: before opening the door, the spring must be unloaded (vertical
boom). The barrier is provided with programmable electronic limit switches
and mechanical stop devices. There must be a rotation margin (about 1°) on
closing and opening between the electrical limit switches and mechanical
stop devices (Fig. N). The adjustment is carried out as follows:
The end-of-stroke opening and closing positions must be set by modifying
the parameters of the control panel for Opening value Calibration and Clos-
ing value Calibration: if the value is increased, the end-of-stroke positions
move towards the opening direction. The extent of the movement depends
on the effective boom length: in the case of a 6-m boom, a unit change (1.0)
entails a movement of about 4,4 cm which, proportionally, becomes about
5,8 cm for an 8-m boom.
The effective closing value also depends, in part, on the manoeuvring speed.
It is therefore convenient to proceed to end-of-stroke calibration only after
having set the other opening parameters.
INSTALLATION MANUAL
26
-
MICHELANGELO
D811528 00100_03
Содержание MCL 40
Страница 2: ...2 MICHELANGELO D811528 00100_03 ...
Страница 13: ...4 5 6 30 mm AD 19 13 MICHELANGELO 13 D811528 00100_03 ...