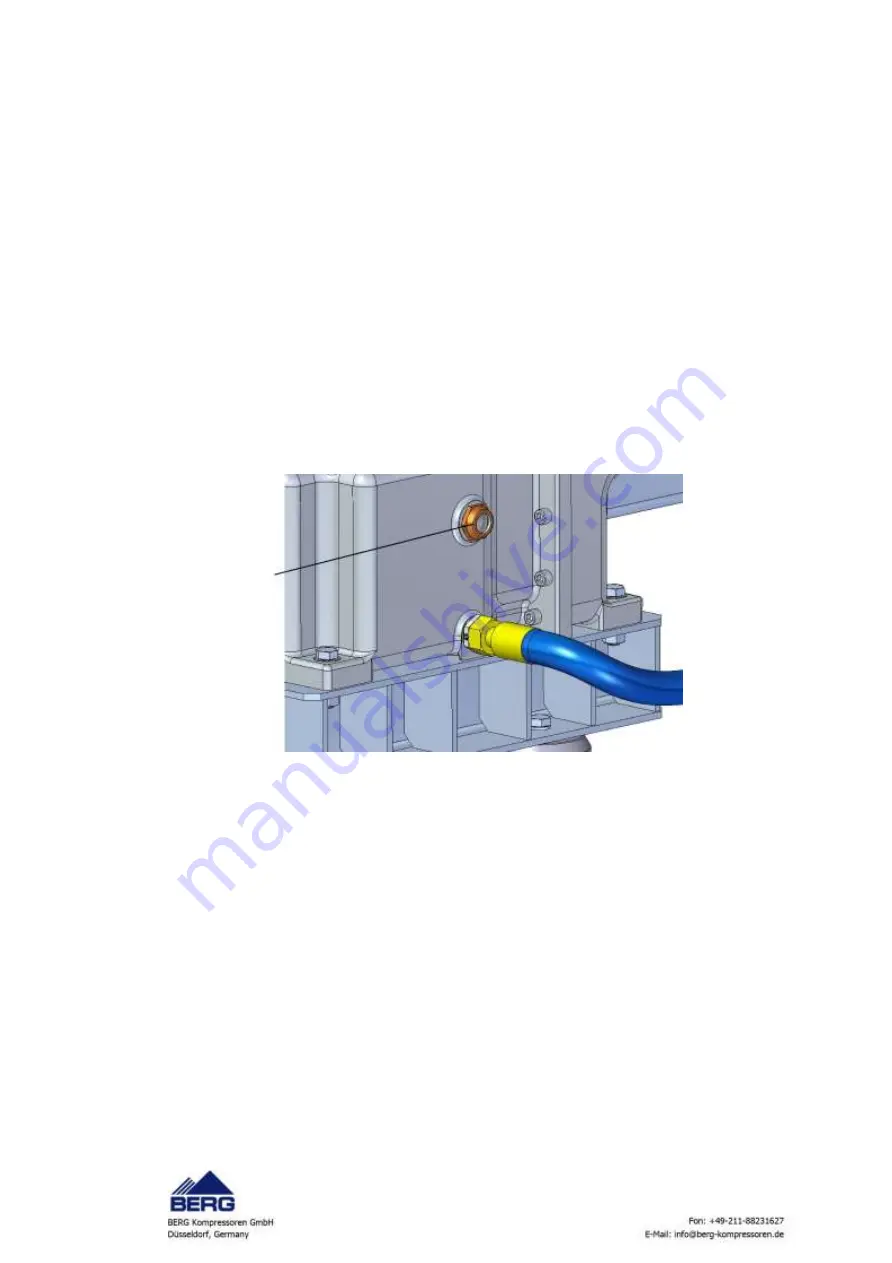
27
-
Rub some oil onto the gasket of the new filter before screwing it in. Fill the new filter, held
vertically, with the same type of oil as that in the separator tank. Then screw the filter in by hand,
without using any tool.
-
Start the compressor and check for leaks.
7.3.4. Oil level
Sufficient oil level in the oil receiver is of critical importance for trouble-free performance of
the compressor.
Oil check intervals:
-
after prolonged compressor off-time,
-
every 100 hours.
Procedure:
-
check oil level after 1 minute from the compressor stop,
-
the oil should be above the middle line of the sight glass (during normal use when the cooler is full
of oil at all times).
Oil level indicator
7.3.5 Changing oil
The oil can be changed only when the compressor is stopped and completely depressurised. The machine
should be heated up to the operating temperature (oil temperature between 50 and 60°C).
Maintenance procedure:
-
Stop the compressor and wait until the overpressure in the screw assembly body and oil system reaches the
atmospheric pressure (look at the microprocessor controller).
-
Safeguard the compressor from restarting by an unauthorized person, e.g. by cutting power supply off.
-
Start the options for manually opening of the oil control solenoid valves in the radiator (see the controller
operating instructions).
-
Unscrew the compressor crankcase ventilation hose on the compressor stage body (see Fig. 11).
-
Place a suitable container and carefully unscrew the oil drain plug located under the oil reservoir on the hose.
-
Drain the oil from the stage body completely and screw in the drain plug again.
-
Pour new oil through the filler neck to the max.level Close the bleeder hose.
-
Switch on the screw compressor and leave it working for approx. three minutes (the oil cooler should be
completely full).
-
Check the oil level: top up with the missing amount of oil up to max.
-
Used oil should be disposed of in accordance with applicable regulations.
Oil dedicated for oil free screw compressors has been used.