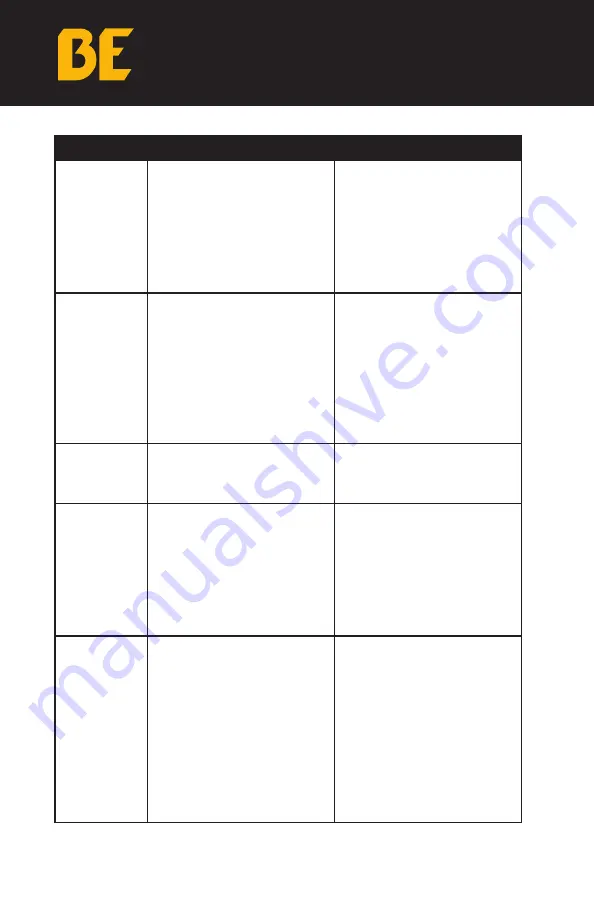
26
Problem
Possible Cause
Solutions
Excessive oil
discharge in air
(All Compres-
sors have a
small amount of
oil carry over in
compression
1. Worn piston rings or cylinder
2. Restricted air intake
3. Oil level to high
4. Compressor has exceeded it
duty cycle
1. Clean or replace air filters
2. Reduce oil level to recom-
mended amount
3. Reduce compressor duty cycle
(repair leaks or add another unit to
handle the excess demand)
Compressor
Overheating
1. Poor ventilation
2. Dirty cooling surfaces
3. Compressor is out of its operat-
ing duty cycle
1. Relocate compressor to any
area with better ventilation (at
least 18 inches from the nearest
wall)
2. Clean all cooling surfaces
3. Reduce compressor duty cycle
(repair leaks or add another unit to
handle the excess demand)
Excessive Belt
Wear
1. Pulley out of alignment
2. Improper belt tension
3. Pulley damaged of loose
1. Realign pulley with flywheel
2. Re adjust belt tension
Compressor
wont start in
cold weather
1. Bad check valve
2. Compressor has wrong grade oil
3. Control lines frozen
1. Use IS 100 (30W) compressor
oil for cold weather conditions
2. Move compressor to a warmer
location
3. Put a heat lamp on compres-
sor to maintain above freezing
temperatures
Compressor
Motor Hums
wont start
1. Fuse or Breaker blown in main
panel (or fuse in fused disconnect
if applicable)
2. Low voltage to compressor
3. Compressor starting with head
pressure
4. Power leads in motor or mag-
netic starter loose
5. Starter or Pressure switch
contacts corroded or broken
1. Re-set breaker or replace blown
fuse
2. Inspect check valve for proper
operation
3. Check all power wire lead to
solid connection
4. Replace starter and Pressure
switch
troubleshooting
Содержание 120 GALLON HORIZONTAL
Страница 1: ...User Manual 120 GALLON HORIZONTAL AIR COMPRESSOR BEPOWEREQUIPMENT COM ...
Страница 2: ...2 ...