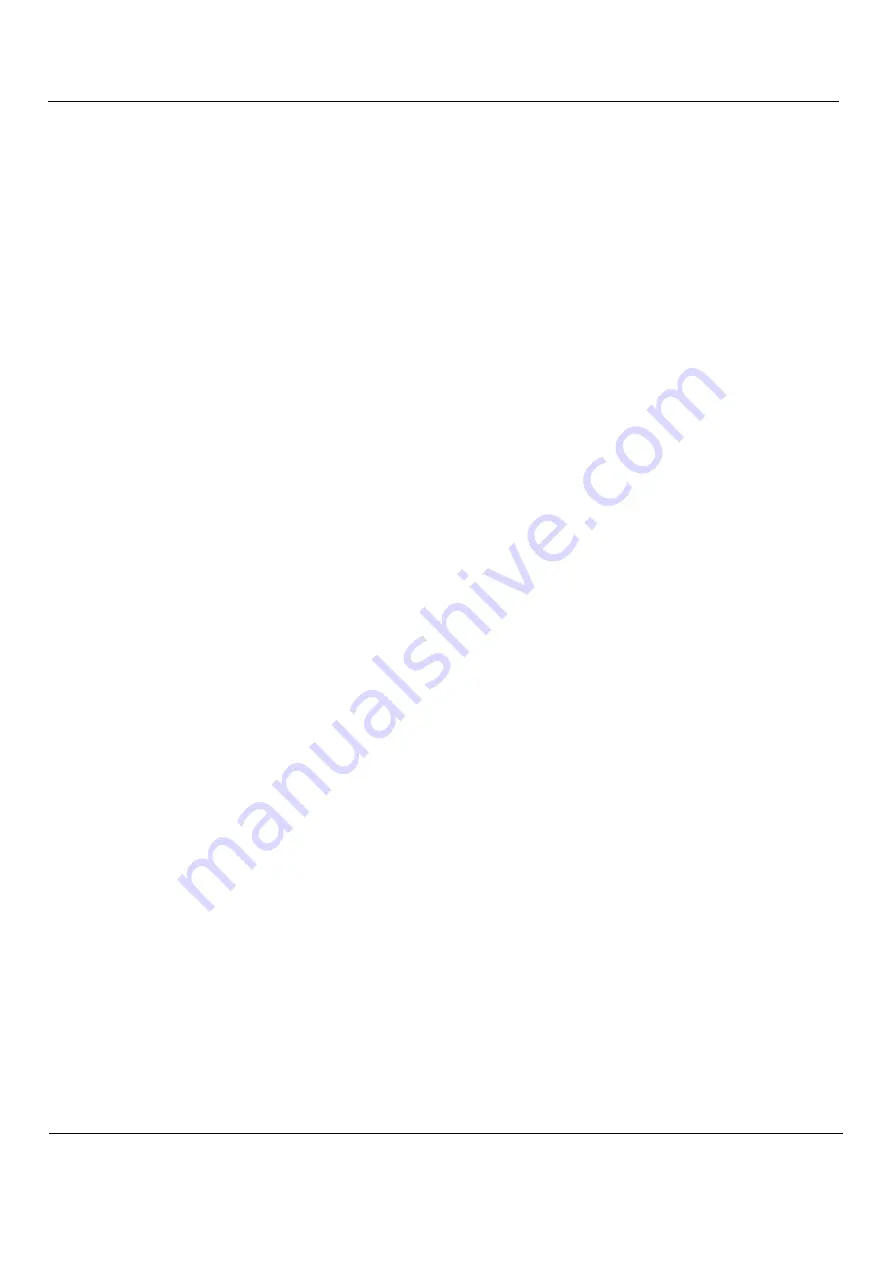
Benezan Electronics
Hard- and software development
Triple Beast Installation Guide
Nicolas Benezan, Stauffenbergstr. 26, 72108 Rottenburg
Phone: +49 (0) 7457/946365 0 benezan-electronics.de
Page
TripleBeast-NET Installation.docx22.09.2020
Emergency stop
The Triple BEAST has several independent functions that are used to stop the machine in case of problems:
1.
An emergency stop button (mushroom/panic button) must be connected to terminals X2.5 and X2.6. If the contact is
opened, relays 1 and 2 are forcibly switched off. A push-button emergency stop is indicated by the right LED (red,
LED4). Additionally, an emergency stop is reported to the PC
2.
If the status output of one or more output stages reports an error or if the line of the step/direction signal is interrupted, an
error signal (drive fault) is sent to the PC. The output stage error is indicated by the second LED from the right (red,
LED3).
3.
In case of missing or insufficient supply voltage, an emergency stop signal is sent to the PC, so that the software does not
continue to run uncontrolled.
4.
Relay outputs and step signals are only enabled if there is a valid connection with the PC software and the software
regularly sends ready messages. If the connection is interrupted, all outputs are deactivated after a few seconds for safety
reasons.
Speed control (analog output)
In order to be able to specify the speed for a frequency inverter, the Triple BEAST has an analog output 0..10V. A voltage
proportional to the duty cycle of the PWM signal is output. Here 0% (low) corresponds to a voltage of 0V, 10% corresponds to
1V, 20% corresponds to 2V etc. up to 100% and 10V. The frequency of the PWM signal should be at least 1kHz so that the ripple
of the analog signal is not too high.
The analog output is not galvanically isolated, but referred to the power supply ground. However, this is not a problem with all
modern frequency inverters because they have an isolated speed input. Care should be taken with old thyristor controllers whose
speed input is partially connected to the mains voltage. These must not be used. If in doubt, please refer to the data sheet of the
frequency inverter or speed controller.
Please note that a frequency inverter should not be controlled exclusively with the analog signal. Be sure to connect the digital
start/stop input to one of the relays as well. Otherwise it is possible that the motor does not stop completely at 0V, or that it starts
unexpectedly in case of malfunctions. Please note that mixed use of mains voltage (230V~) and low voltage (<=24V) at the relay
outputs is not permitted (see chapter "Relay outputs", above).
Holding brake
When using ball screws, smooth-running servomotors or very heavy Z-axes, an electromechanical holding brake must be provided
to prevent the vertical axis from moving down by itself when the drive is switched off. Such brakes are usually operated with 24V.
They are blocked when no voltage is applied and open when the voltage is switched on.
The Triple BEAST has a relay output for such a holding brake. The relay is controlled as a normal output via the software. If
no brake is required, the relay can also be used for other purposes, e.g. as a start/stop signal for a frequency converter. This has the
advantage that the signal is applied to the same terminal (X2), and the relay outputs 1 and 2 at terminal X4 then remain free for
other consumers with possibly different voltages.
The output has an integrated free-wheeling diode and is suitable for switching inductive loads. The output voltage is always
equal to the power supply voltage at terminal X1.5, i.e. for a 24V brake the board must then be supplied with a 24V power supply.
If the brake is to be operated pneumatically, hydraulically or with a voltage other than the power supply voltage, an external
contactor or solenoid valve is required.