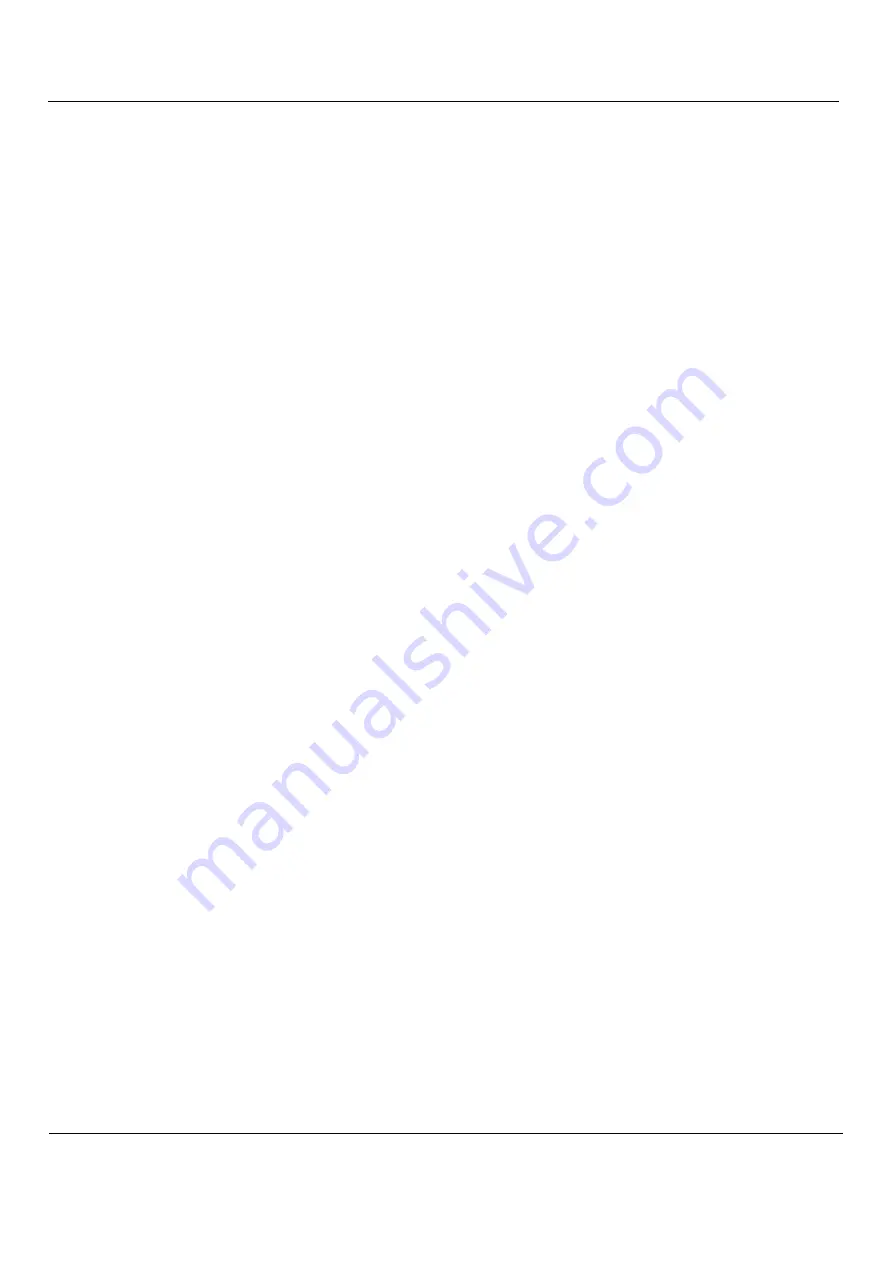
Benezan Electronics
Hard- and software development
Triple Beast Installation Guide
Nicolas Benezan, Stauffenbergstr. 26, 72108 Rottenburg
Phone: +49 (0) 7457/946365 0 benezan-electronics.de
Page
TripleBeast-NET Installation.docx22.09.2020
Assembly
The output stage is designed for mounting on a 35mm DIN rail ("top-hat rail") in a housing.
Protect the unit from flying chips,
dust and cooling water
. Damage caused by metal chips or moisture will void the warranty. Hook the controller into the rail with
the motor connections facing up, then press the heat sink firmly onto the rail until it clicks into place. Alternatively, it can also be
fastened from the rear with self-tapping self-tapping self-tapping screws B3.5x10 or spacer bolts on a mounting plate. In this case
the clip for the DIN rail must be removed. Attention - never use a longer screw than the one supplied (M4x16) to screw on the
clip. Otherwise they could damage the power components mounted on the inside of the heat sink.
Since the output stage becomes more or less hot during operation depending on the motor current, the following rules must be
observed during installation:
Make sure that there is free air circulation. The distance to other devices, housing wall, cable ducts, etc. should be at least 2 cm
on all sides.
If possible, the heat sink should be mounted vertically with vertical fins.
For motor currents up to a maximum of 3 x 4.2A, natural convection is sufficient, i.e. a fan is not required if the air circulation
is not obstructed by a housing that is too small.
For motor currents from 3 x 5A or >13A in total, supported cooling with a fan is advisable. A small processor fan for PCs, for
example, can be used for this purpose. A 12V connection is provided for the power supply of the fan (X1 terminals 2+3), which
can supply up to 300mA.
Overheating cannot lead to the destruction of the controller, because an integrated overtemperature protection switches off the
motor current when the maximum temperature is exceeded. Nevertheless, it is advisable not to operate the output stage
permanently at the upper temperature limit, as this will reduce its service life.
Power supply connection
The supply voltage must be between 24 and 55V. For most applications a 48V switch mode power supply is ideal because
these power supplies are small, light, relatively inexpensive and easy to connect. They are also overload-proof and usually have
inrush current limiting and mains filter already integrated.
However, a stabilized power supply is not necessarily required; an unregulated power supply consisting of transformer, rectifier
and filter capacitor is also suitable. Please note, however, that the voltage range must be maintained even with mains and load
fluctuations (usually ±10%). Also make sure you have suitable fuse protection. If necessary, inrush current limitation and an
interference filter may be necessary.
The maximum current with which the power supply unit is loaded is approx. 2/3 of the motor current. However, the continuous
load load is lower in most applications. For the operation of 3 motors with 4A each, for example, a power supply unit with 3 x 4A
x 2/3 = 8A peak current and about 5A continuous load capacity is sufficient. An electrolytic capacitor with about 4700μF at the
power supply output is recommended to keep voltage fluctuations small due to fast load changes.
Connect the positive pole of the power supply unit to terminal "V" connection 1 (on the side, labelled +24..55V) and the
negative pole to connection 2 (labelled GND).
Attention,
wrong polarity can damage the power amplifier
, especially if the
power supply has no fast fuse or current limiter.
Never connect or disconnect the supply connection under load
.
Do not switch
the secondary side of the power supply (DC voltage) with switches
or fuses. The resulting arc can cause damage. Only switch
the power supply unit on and off on the primary side (mains AC voltage). The protection should also be provided on the primar y
side. Please note that the negative connection (Power Ground) is connected to the heat sink and thus automatically to the housing
(potential earth).
For most applications, the power supply unit that supplies the motor voltage can also be used to supply the PC interface
(terminal X1). Connect the positive pole to X1 terminal 5 and the negative pole to terminal 4. Only if you use inductive proximity
switches with 24V and the motor supply voltage is higher than 24V, an extra 24V power supply unit is required. For details please
refer to the chapter "Limit switches".
Motor connection
When using prefabricated cables for stepper motors from Benezan Electronics the connection of the motors is very easy. Connec t
the wires numbered 1..4 in sequence to terminals M1, M2 or M3. Connect the cable lug of the shield connection to the flat plug
next to the terminal. Plug the XLR connector of the motor into the female connector on the other side of the cable - ready.
For motors from other manufacturers you must consult the relevant data sheet to identify the wire colours of the coil
connections. For motors with 4 connections you can also use a continuity tester. Connected terminals belong to the same coil.
Connect the terminals of one coil to terminals 1 and 2 of the terminal, the terminals of the other coil to terminals 3 and 4.