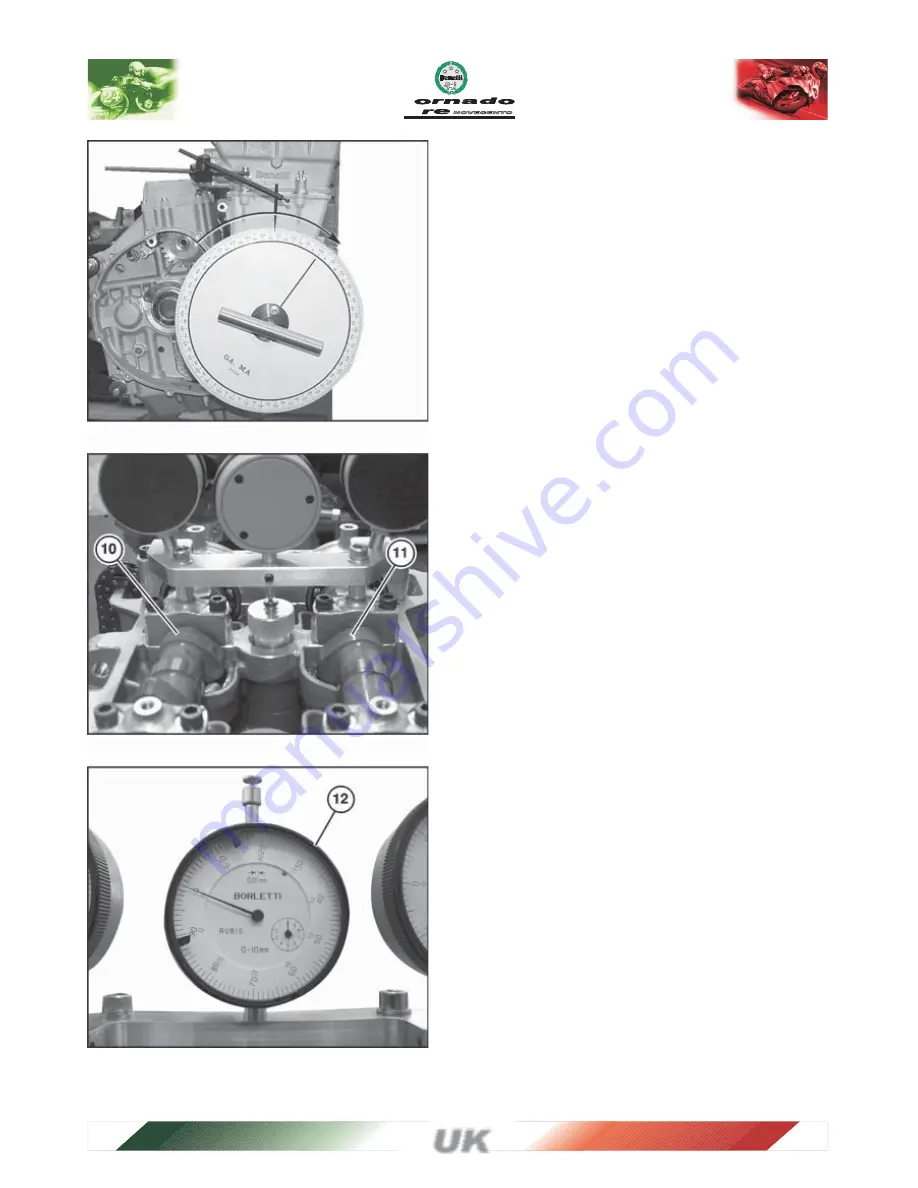
UK
66
MF9_UK
T
T
T
T
L
I
M
I
T
E
D
E
D
I
T
I
O
N
Turn the goniomenter drive clockwise until finding the upper
dead centre.
The olives of the two eccentric shafts on the first piston should
be turned towards each other.
Once the u.d.c. (upper dead centre) is found, position the
crown (12) at zero on the central test indicator.
Содержание Tornado Tre Novicento 903
Страница 1: ...UK 1 MF9_UK T T T T L I M I T E D E D I T I O N COPERTINA ...
Страница 2: ...UK 2 MF9_UK T T T T L I M I T E D E D I T I O N ...
Страница 35: ...UK 35 MF9_UK T T T T L I M I T E D E D I T I O N ...
Страница 36: ...UK 36 MF9_UK T T T T L I M I T E D E D I T I O N ...
Страница 37: ...UK 37 MF9_UK T T T T L I M I T E D E D I T I O N ...
Страница 38: ...UK 38 MF9_UK T T T T L I M I T E D E D I T I O N ...
Страница 39: ...UK 39 MF9_UK T T T T L I M I T E D E D I T I O N ...
Страница 40: ...UK 40 MF9_UK T T T T L I M I T E D E D I T I O N ...
Страница 41: ...UK 41 MF9_UK T T T T L I M I T E D E D I T I O N ...
Страница 42: ...UK 42 MF9_UK T T T T L I M I T E D E D I T I O N ...
Страница 43: ...UK 43 MF9_UK T T T T L I M I T E D E D I T I O N ...
Страница 44: ...UK 44 MF9_UK T T T T L I M I T E D E D I T I O N ...
Страница 45: ...UK 45 MF9_UK T T T T L I M I T E D E D I T I O N ...
Страница 46: ...UK 46 MF9_UK T T T T L I M I T E D E D I T I O N ...
Страница 47: ...UK 47 MF9_UK T T T T L I M I T E D E D I T I O N ...
Страница 48: ...UK 48 MF9_UK T T T T L I M I T E D E D I T I O N ...
Страница 176: ...UK 176 MF9_UK T T T T L I M I T E D E D I T I O N Remove the five screws 6 Remove screw 7 Remove the two screws 8 ...
Страница 177: ...UK 177 MF9_UK T T T T L I M I T E D E D I T I O N Remove screw 9 Remove the two screws 10 Loosen and remove screw 11 ...
Страница 224: ...UK 224 MF9_UK T T T T L I M I T E D E D I T I O N ...
Страница 301: ...UK 301 MF9_UK T T T T L I M I T E D E D I T I O N E E E E Electrical P P P P Plant 9 ELECTRICAL PLANT ...
Страница 318: ...UK 318 MF9_UK T T T T L I M I T E D E D I T I O N ...
Страница 328: ...UK 328 MF9_UK T T T T L I M I T E D E D I T I O N ...
Страница 333: ...UK 333 MF9_UK T T T T L I M I T E D E D I T I O N ...
Страница 334: ...UK 334 MF9_UK T T T T L I M I T E D E D I T I O N ...
Страница 335: ...UK 335 MF9_UK T T T T L I M I T E D E D I T I O N ...
Страница 336: ...UK 336 MF9_UK T T T T L I M I T E D E D I T I O N ...