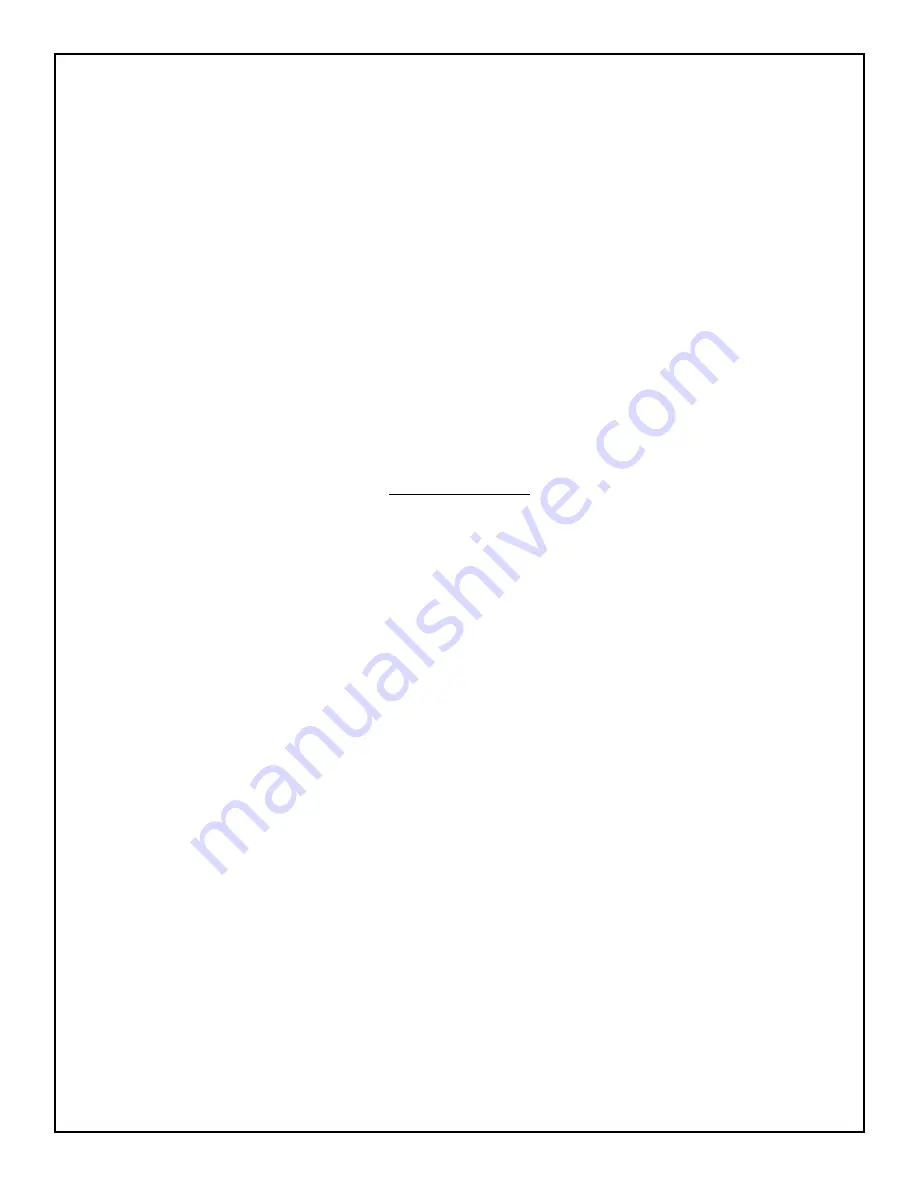
33
LIFT LOWERS SLOWLY OR NOT AT ALL
possible cause
1. Cylinders binding, (1)
2. Release valve clogged, (5,4,2,3)
3. Pressure fitting too long, (6)
remedy
insTrucTion
1. See Installation Manual . . . . . . . . . . . . . . . . . . . . . . . . . . . Contact BendPak Customer Support.
2. Replace with new part . . . . . . . . . . . . . . . . . . . . . . . . . . . . Replace with new part.
3. Return for repair . . . . . . . . . . . . . . . . . . . . . . . . . . . . . . . . . Return for repair.
4. Check oil. . . . . . . . . . . . . . . . . . . . . . . . . . . . . . . . . . . . . . Use clean AW32 hydraulic oil only. If oil is contaminated,
replace with clean hydraulic oil and flush entire system.
5. Clean release valve . . . . . . . . . . . . . . . . . . . . . . . . . . . . . . . . Wash release valve in solvent and blow out with air.
6. Replace fitting with short thread lead . . . . . . . . . . . . . . . . . . . Replace fitting with short thread lead.
IMPORTANT
If vehicle becomes stranded in the air, follow all operation instructions as shown on pages 25 and preceding
Troubleshooting sections. If after observing that all mechanical locks are released and the lift still fails move following all
standard operating procedures, immediately stop using the lift and contact factory or factory approved service center for
further instructions.