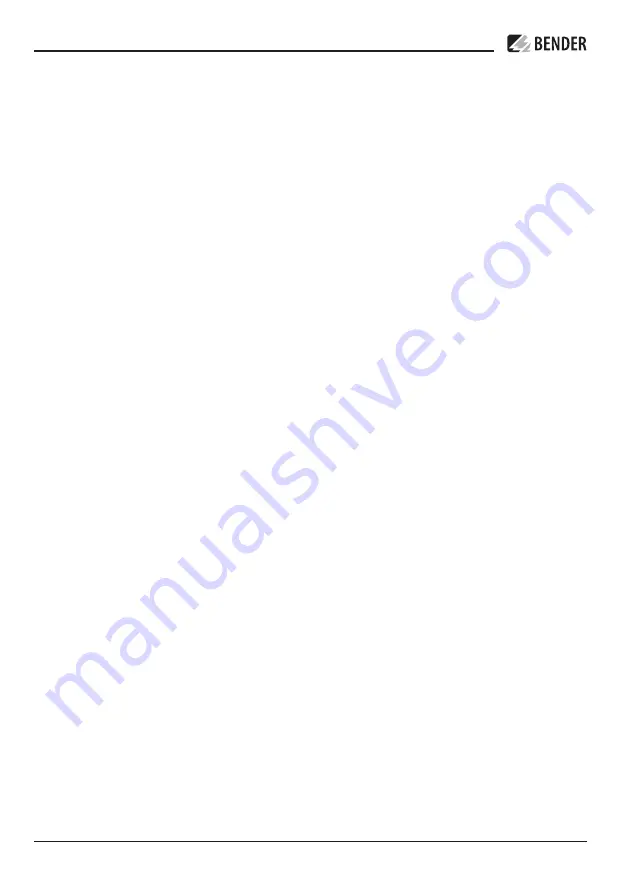
8 CC613_D00381_04_M_XXEN/11.2020
Function
2.3
Product description
The charge controller monitors the internal hardware of charging systems such as the meter, the user inter-
face module or the socket-outlet. It can be operated as an "always-on system" that is always connected to a
mobile network. The master variant supports 4G mobile networks.
Communication with a backend system is possible via the OCPP application protocol. All specified messages
in OCPP are supported as well as some vendor-specific extensions based on the DataTransfer message.
Integration tests with the backend implementations of providers (e.g. has-to-be, Virta and NewMotion) have
been carried out successfully.
Refer to "Ordering details" for product variants.
2.4
Functional description
The charging system consists of an RCD type A and a contactor. These are directly connected to a type 1 or
type 2 socket-outlet, or to an attached cable with a type 1 or type 2 plug (see chapter "Charging system with
type 2 socket-outlet").
2.4.1 General functions
• The charging system can be equipped with a meter. A Modbus meter is required for digital reading
of the energy consumption. The Modbus RTU wires are attached directly to the charge controller.
• A 12 V power supply is needed for operation.
• An RFID module can be used for easy user interaction.
• Power flow toward the vehicle is enabled by enabling the contactor via an integrated 230 V control
relay in the charge controller.
• Using a micro SIM card (not included in the scope of delivery):
The SIM card slot (available on data gateways with a 4G modem only) is located on the charge con-
troller front panel. The SIM card can have a PIN number which can be configured via the
Operator
tab. The APN settings for the SIM card can also be configured via the Operator tab.
• Data gateways with a 4G modem feature a socket for a 4G antenna on the front panel.
• For fault current detection in an AC charging system, the charge controller features an integrated
residual direct current monitoring module (RDC-M) which uses an externally connected current
transformer. With the integrated monitoring of the DC fault current, only an RCD type A is required
in the charging system.
• Data exchange between the electric vehicle and the charging system is possible via ISO 15118 com-
pliant Powerline Communication (PLC).
• Dynamic load management (DLM):
The charge controller comes with a DLM software, which is fully usable independent of a backend
connection. It detects which charging current is applied to which phase and thus avoids the occur-
rence of peak loads and unbalanced loads. Maximum number of charging points in a network: 250.
• Data management and control functionality of the charge controller:
– Termination of the charging process after tripping of the residual current device (RCD) due to a
residual current.
– Detection of critical fault currents by the RCM sensor. For the vehicle owner, this can be an early
warning, provided that the charge controller is connected to an energy management system
and that it supports this function.
• External Modbus interface for advanced control of the controller via an energy management sys-
tem, independent of a backend connection.