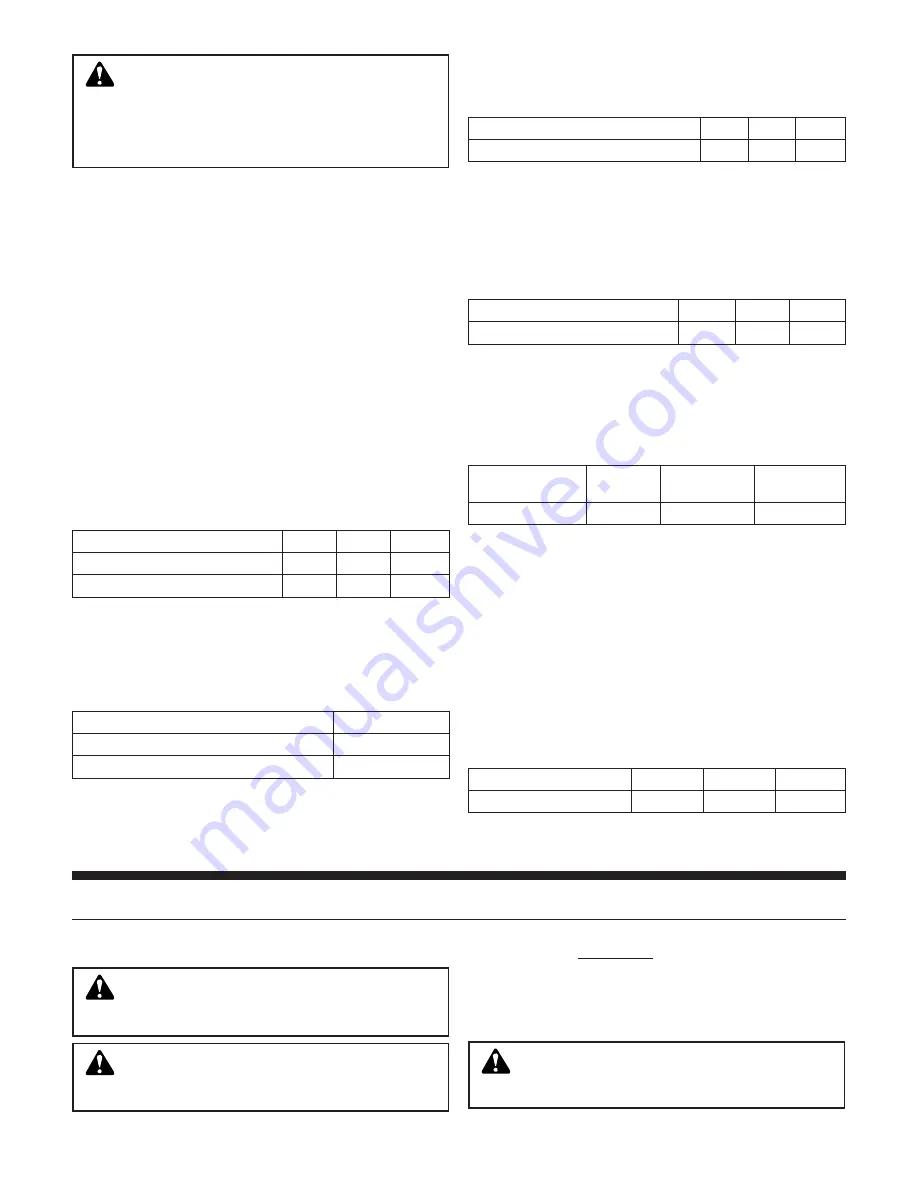
8
2.7
WIRING
2.7.1
POWER WIRING
The 70E/70M Pump Control Panel can be set up to
operate across a broad range of voltages. It was fac-
tory set to operate on the voltage shown on the
nameplate. Verify proper transformer primary wiring
per the job-specific wiring diagram. Check power
leads in accordance with wiring diagram enclosed in
control cabinet. The voltage tolerance is +10%/-10%.
2.7.2
ANALOG SIGNAL WIRING
If installing the panel on an existing system, shielded
cable (#22 AWG, Belden type 8762, Alpha #2411 or
equal) should be installed for the DC control wiring.
The shield must be terminated in the 70E/70M con-
trol panel. Do not connect the shield at the other end
of the cable! Insulate the shield so that no electrical
connection is made at the other end of the cable. A
twisted pair of #22 AWG conductors (Belden 8442 or
equal) can be used in place of shielded cable. The
cable length must be limited to 3000 feet for #22
AWG wire.
2.7.2.1
PRESSURE TRANSMITTER WIRING
(4-20 mA Analog Signals)
2.7.2.2
TEMPERATURE SENSOR WIRING
(Analog Resistance Input)
The 70E/70M uses resistance temperature detectors
(RTDs) to sense the suction and discharge water
temperatures. These devices change their resistance
as the water temperature changes.
2.7.2.3
FLOW SENSOR/TRANSMITTER WIRING AND
INSTALLATION (4-20 mA Analog Signal) (Optional)
The flow sensor should be installed at an angle no
greater than 45 degrees from top dead center in a
horizontal installation (see manufacturer’s IOM). See
the Bell & Gossett drawing for installation instruc-
tions. The signal wiring should be terminated in the
70E/70M panel at the terminals below.
2.7.3
DIGITAL SIGNAL WIRING
2.7.3.1
DIFFERENTIAL PRESSURE SWITCH PIPING
AND WIRING (Digital Signal) (Optional)
Differential pressure switches installed to sense the
increase in pressure between the pump suction and
discharge gauge taps are used to determine whether
a pump is running. Each switch should be wired from
the normally closed contact to the terminals below.
2.7.3.2
LOW LEVEL CONTROL WIRING
(Digital Signal) (Optional)
The low water level control option is utilized when
drawing water from a tank. In this control circuit, two
electrodes sense the water level inside of a water
tank. When the water level drops below its minimum
level, the pressure booster will shut down.
2.7.3.3
REMOTE START-STOP (Digital)
Install a non-powered dry contact digital input to ter-
minals J4-1 and J4-2. With the LOCAL-REMOTE-
OFF switch in the REMOTE position this contact
closure will provide the start signal.
2.7.3.4
REMOTE ALARM INDICATION (Digital Signal)
A digital output dry contact rated 2 Amps at 115V is
supplied on terminals J5-7 and J5-8. This output
closes to indicate that an alarm condition exists.
2.7.3.5
PUMP ON/OFF REMOTE SIGNAL (Digital Signal)
A digital output dry contact (one per pump) rated 2
Amps at 115V is provided for remote monitoring of
pump On/Off status. This contact closes when a
pump is running.
Terminals (J3)
+
-
Shield
Suction Pressure
3
2
4
System (discharge) Pressure
3
6
4
Temperature Sensor (RTD) Wiring
Terminals (J3)
Low Temperature Sensor (suction)
13, 14
High Temperature Sensor (discharge)
16, 17
Optional Flow Sensor/Transmitter
+
-
Shield
Terminals (J3)
9
8
10
Pump #
1
2
3
Terminals (J4)
9, 8
10, 11
11, 12
Pump On
Pump Off
Ground
Electrode
Electrode
Terminals (J4)
66
67
68
Pump On/Off Signal
Pump #1
Pump #2
Pump #3
Terminals (J5)
9, 10
11, 12
13, 14
3.0
PUTTING THE UNIT INTO SERVICE
3.1
PUMP ROTATION, 3 PHASE MOTORS ONLY
With the disconnect switch engaged to the “ON”
position, momentarily start and stop each motor with
the pump motor key on the key pad. See Paragraph
5.3 on page 16. Observe the pump shaft rotation.
3.2
If incorrect, turn the main disconnect off and inter-
change any two wire leads leaving the starter over-
load block and going to the motor.
3.3
Unit is now ready for operation (factory assembled
tested units only).
SECTION 3 – START UP
WARNING: Rotating shafts can catch loose cloth-
ing. Do not operate the pump without all guards in
place. Failure to follow these instructions could result in
serious personal injury, death, and/or property damage.
CAUTION: Seal Damage may occur. Do not run
pumps dry. Fill and vent the pump volute prior to
operation. Failure to follow these instructions could re-
sult in property damage and/or moderate personal injury.
DANGER: High Voltage 3 phase power can kill.
Disconnect and lockout power prior to servicing
unit. Failure to follow these instructions could result in
serious personal injury, death, and/or property damage.
DANGER: Electrical shock hazard. Inspect all elec-
trical connections prior to powering the unit. Wiring
connections must be made by a qualified electrician in
accordance with all applicable codes, ordinances, and
good practices. Failure to follow these instructions
could result in serious personal injury, death, and/or
property damage.