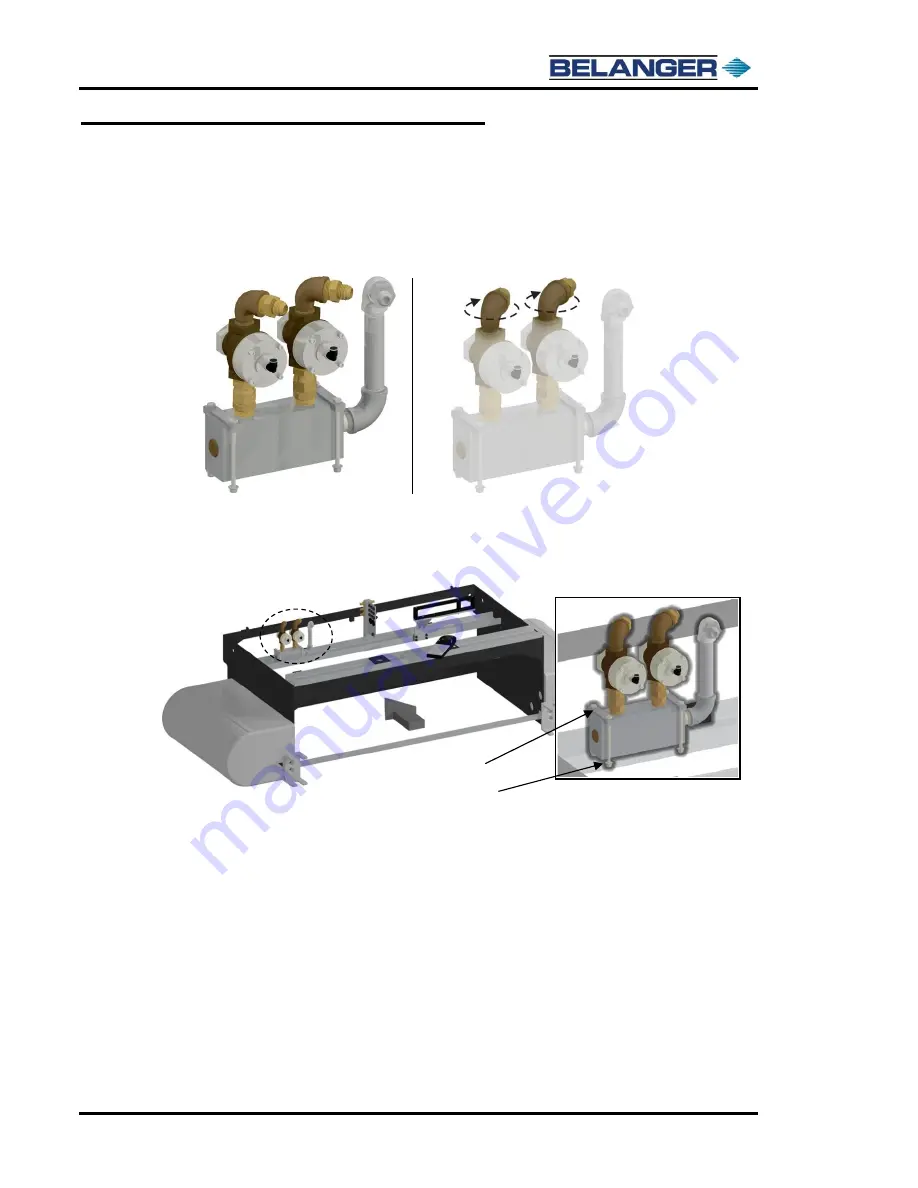
INSTALLATION AND STARTUP
4-28
Belanger, Inc.® * PO BOX 5470. * Northville, MI 48167-5470 * Ph (248) 349-7010 * Fax (248) 380-9681
1MANUL220
Chapter 4 Frame and Carriage Assembly
Passenger Side Boom Install
Optional HydroBlade®/ Wheel Cleaner
Lexair™ Distribution Manifold
5)
Tighten the
Lexair™ Valves into plac
e as shown below. Be sure that the fittings are facing in the shown
orientation.
6)
Take the manifold assembly back up to the carriage and tighten it into place on the Driver side of the carriage
using the 5/16-18 fasteners, washers, Nylo
ck™ nuts, and the clamps as shown below.
Verify that the valve orientations match the image below.
The following 2 pages show the other components related to this Distribution
Manifold that also need to have their orientation changes.
Before
After
5/16-18 fasteners, flat washers,
Nylock
™
nuts (4) of each
Clamp (2)
Содержание FreeStyler
Страница 1: ...FreeStyler Installation Startup FreeStyler Installation Startup 1MANUAL220 Rev14 ...
Страница 2: ......
Страница 4: ......
Страница 12: ......
Страница 13: ... Chapter 1 Introduction Chapter 1 Introduction ...
Страница 14: ......
Страница 26: ......
Страница 27: ... Chapter 2 Recommended Installation Sequence Checklist Chapter 2 Recommended Installation Sequence Checklist ...
Страница 28: ......
Страница 31: ... Chapter 3 Getting Started Chapter 3 Getting Started ...
Страница 32: ......
Страница 52: ......
Страница 53: ... Chapter 4 Frame and Carriage Assembly Chapter 4 Frame and Carriage Assembly ...
Страница 54: ......
Страница 123: ... Chapter 5 Entrance and Exit Photo Eyes Chapter 5 Entrance and Exit Photo Eyes ...
Страница 124: ......
Страница 135: ... Chapter 6 Treadle Assembly Chapter 6 Treadle Assembly ...
Страница 136: ......
Страница 142: ......
Страница 143: ... Chapter 7 Chemical Delivery and Pumping Station Chapter 7 Chemical Delivery and Pumping Station ...
Страница 144: ......
Страница 151: ... Chapter 8 MixStir Options Chapter 8 MixStir Options Triple Foam and High Pressure Wax ...
Страница 152: ......
Страница 163: ... Chapter 9 Reclaim Water Adapter Kit Option Chapter 9 Reclaim Water Adapter Kit Option ...
Страница 164: ......
Страница 167: ... Chapter 10 Booster Pump Assembly Option Chapter 10 Booster Pump Assembly Option ...
Страница 168: ......
Страница 174: ......
Страница 175: ... Chapter 11 Bug Spray Applicator Option Chapter 11 Bug Spray Applicator Option ...
Страница 176: ......
Страница 183: ... Chapter 12 Undercarriage Options Chapter 12 Undercarriage Options ...
Страница 184: ......
Страница 191: ... Chapter 13 Water Softener Option Chapter 13 Water Softener Option ...
Страница 192: ......
Страница 205: ... Chapter 14 HydroBlade Assembly Option Chapter 14 HydroBlade Assembly Option ...
Страница 206: ......
Страница 226: ......
Страница 249: ... Chapter 16 Signage Options Chapter 16 Signage Options ...
Страница 250: ......
Страница 253: ... Chapter 17 Onboard Dryer Option Chapter 17 Onboard Dryer Option ...
Страница 254: ......
Страница 258: ......
Страница 259: ... Chapter 18 Spot Free Rinse R O Option Chapter 18 Spot Free Rinse R O Option ...
Страница 260: ......
Страница 264: ......
Страница 265: ... Chapter 19 Trades Chapter 19 Trades ...
Страница 266: ......
Страница 270: ......
Страница 271: ... Chapter 20 Electrical Chapter 20 Electrical ...
Страница 272: ......
Страница 282: ......
Страница 283: ... Chapter 21 Pneumatic and Hydraulic Connections Chapter 21 Pneumatic and Hydraulic Connections ...
Страница 284: ......
Страница 293: ... Chapter 22 Initial Startup Chapter 22 Initial Startup ...
Страница 294: ......
Страница 320: ......
Страница 321: ......