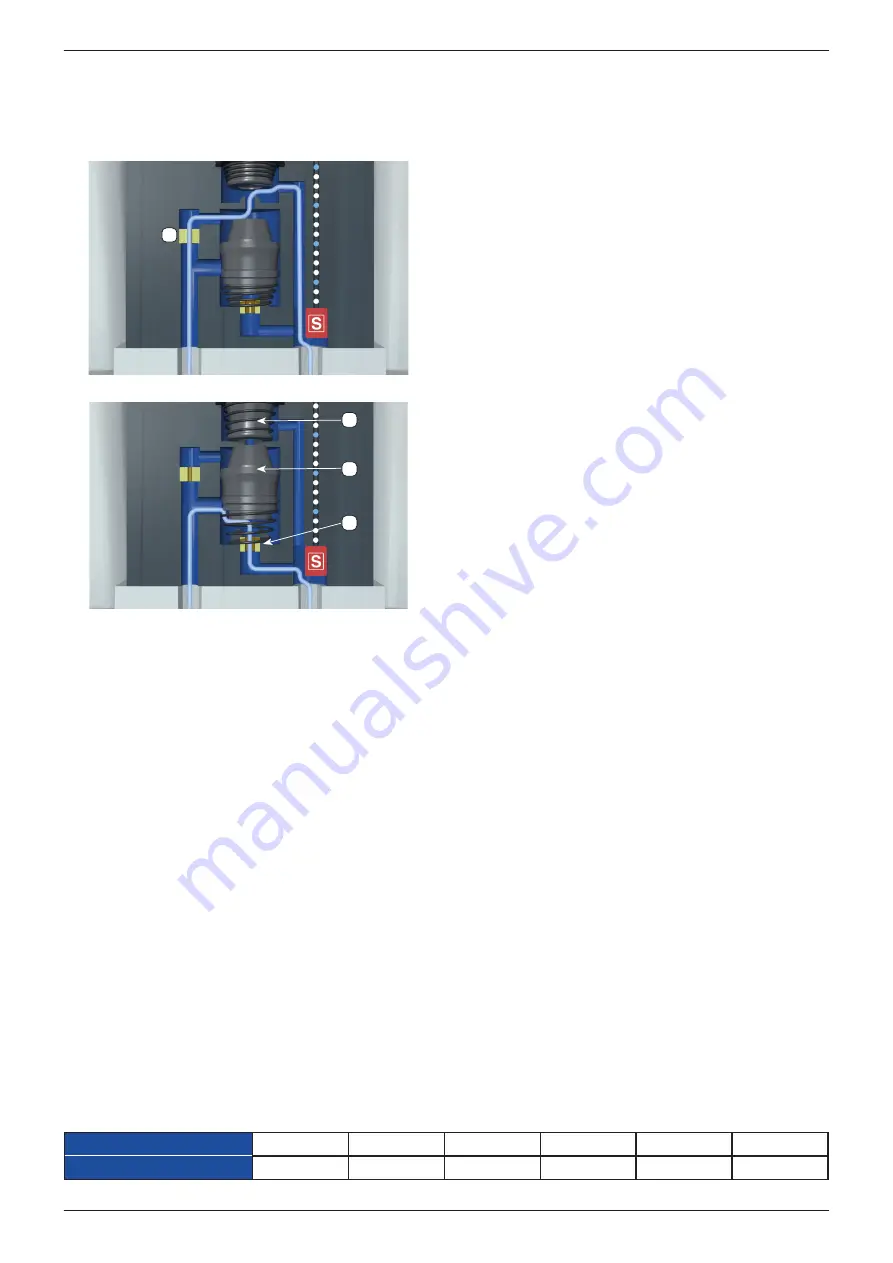
EN
Installation and operating manual
DRYPOINT
®
M eco control
13
The control software decides in defined cycles on the basis of the measurement results whether, and for how long, the
complete purge air volume must be supplied in order to achieve and stabilise the required degree of drying. This process is
implemented via a targeted cycling of a solenoid valve. The duration for both subsequent described process steps therefore
varies in every cycle to retain the degree of drying within the specified tolerance range.
Function: Measuring gas flows
A very small partial flow of the dried compressed air
(measuring gas) flows continuously through the internal
duct guide past a temperature and damp sensor (S) to the
measuring gas jet (1). This sensor continuously specifies the
degree of drying for the compressed air in the measuring gas
and notifies the result to the control system.
Function: Purge air flows
The control system continuously compares the measured
degree of drying of the measuring gas with the individual
specified set point at the
DRYPOINT
®
M eco control
. The
valve unit is actuated with deviations: The solenoid core (2)
and piston (3) close the valve seat so that the compressed air
flows through the purge air nozzle (4) to the membrane dryer.
The drying process commences immediately.
2.4.2. Operating mode
Constant mode (-10 °C; factory-set as default) -
Setting for a constant outlet pressure dew point:
In this mode, the
DRYPOINT
®
M eco control
keeps the pressure dew point set at the outlet constant b10 and
–26 °C. If the set pressure dew point is < 5K (kelvin) below the compressed-air temperature, then the set point pressure dew
point is reduced by one stage (maximum. -26 °C). As soon as the minimum difference of 5K is retained, then the system
returns to normal mode.
Dynamic mode -
constant difference between compressed air temperature and outlet pressure dew point:
In this operating mode, the pressure dew point is reduced relative to the compressed air temperature by a specified
difference between 10 and 55 K. If the compressed air temperature alters, then the pressure dew point will automatically
follow suit. For programme-technical reasons, an increase in the compressed air temperature is limited to 2 °C/h in order to
reduce short-term alterations in the ambient conditions at the installation and/or assembly location.
Note on setting dynamic mode:
• The membrane dryer must always reach a degree of drying that safely prevents the formation of condensation in the
pipes to and at the place of installation of the compressed air consumer: DTP
Outlet
[°C]< T
Ambient
[°C].
• A well ventilated compressor chamber and a low compressed air temperature contribute to ensuring a good degree of
drying.
Measure the temperature at the compressor's place of installation and in the environment around the compressed air
consumer.
Recommended settings on the basis of the temperature difference ΔT between compressor chamber and compressed air
consumer:
Δ T in [K]
10
15
20
25
30
35
Setting “dynamic mode”
30
35
40
45
50
55
1
3
2
4