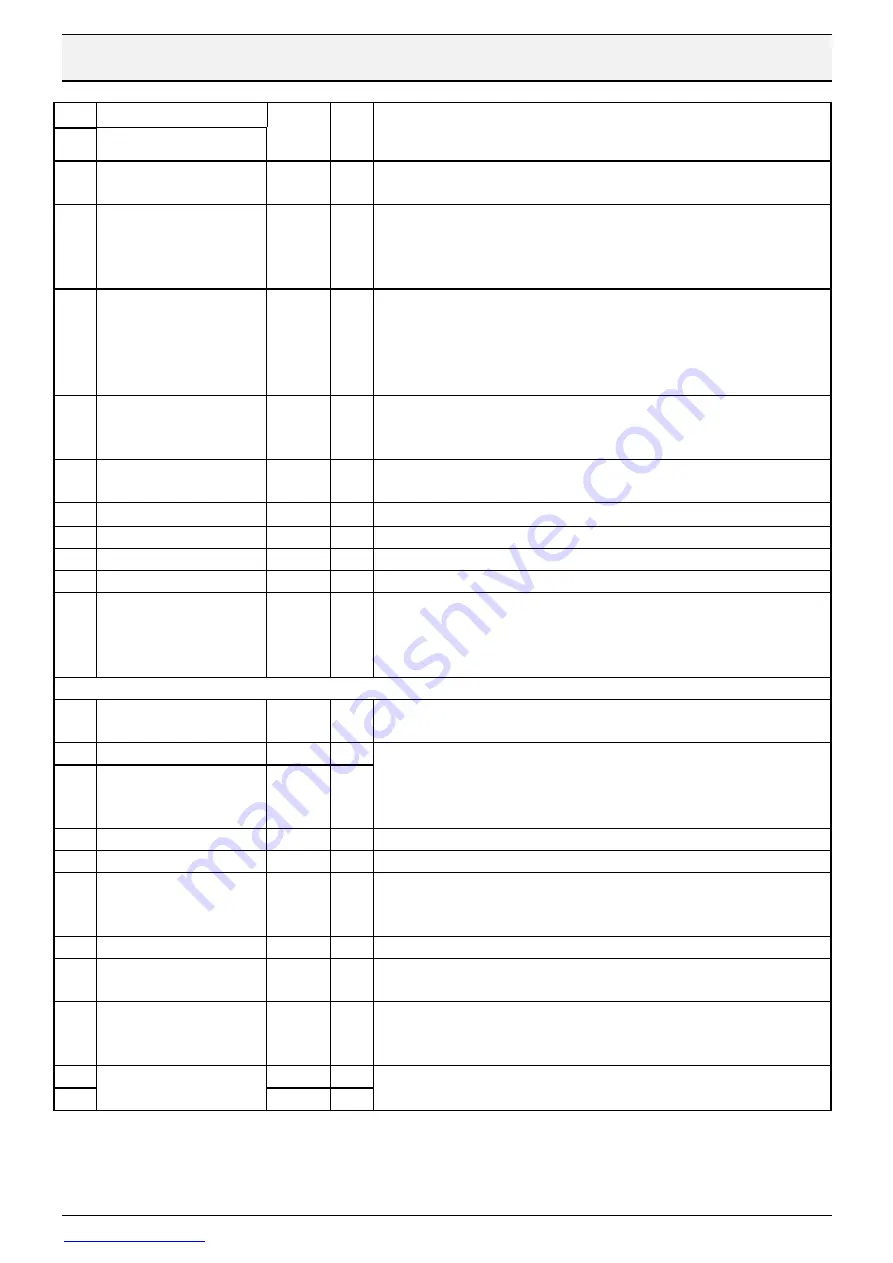
Beijer Electronics Frequency Inverter BFI-H3
KI00363D 2021-07
21 (32)
P2-30 Analog Input 1, AI1
0
0: 0-10 V 3: 0-20 mA 4: t 4-20 mA, trip if signal is below 3 mA
5: r 4-20 mA, ramp to Preset Speed4, P2-04, if signal is below 3 mA.
P2-33 Analog Input 2, AI2
P3-01 PID Proportional Gain
1,0
(Setpoint value
–Feedback value) of PID controller multiplied by P3-01 to
produce output from PID controller.High value cause instability.
P3-02 PID Integral Time
1,0
Accumulated error in the PID control between (Setpoint value
–Feedback
value) to influence the output from PID controller. P3-02 is time constant.
Larger values provide damped response. Lower values result in a faster
system response but may result in instability. 0= Turned off
P3-03 PID Differential Time
0
0
The Differential time constant references the rate of change of the
feedback signal over time and works to slow the rate of change of the PID
controller, particularly as it approached the set-point. Shorter time will
decrease overshoot but slow down response and may lead to instability.
0= Turned off.
P3-04 PID Operating Mode
0
0: Direct Operation. Increase of motor speed increase feedback signal
1: Inverse Operation. Increase in motor speed should decrease feedback
signal
P3-05
PID Digital Reference
source
0
0: PID-reference in P3-06
1: Analog reference on terminal 6
P3-06 PID Digital Reference
0,0 %
PID
–reference: 0-100 % of PID-feedback signal if P3-06=0
P3-07 PID Output Upper Limit
100 %
Maximum output frequency in % of P1-01
P3-08 PID Output Low Limit
0 %
Minimum output frequency in % of P1-01
P3-10 PID Feedback Source
0
0
0 : Analog Input 2 (Terminal 10)
P3-11 PID Error to Enable Ramp
0 %
0: Internal ramps are always used.
0,1-100: When PID-error is less than setting internal ramps are not used
and PID
–controller ramps output frequency. Drive can react quickly to
small errors.
Extra special PID functions
P3-12 Feedback Display Scaling
0
Scaling factor of displayed PID feedback. If analog input is 0
–10 V(=0-
100%) and is equal to 0-10 bar pressure setting is 0,1.
P3-14 Standby Activation Speed
0 Hz
PID Sleep mode parameters. P3-14 defines output frequency at which the
drive will enter standby mode (stop). Drive enters standby mode if motor
speed remains below level in P3-14 for time period in P2-27. Display will
show
Standby
. Function disabled if P2-27=0.
P2-27 Standby Mode Enable
20 sec
P3-13 Feedback Wake Up Level
0 %
PID Wake up level. When PID error > P3-13 drive will restart motor.
P3-15 2nd PID Digital Reference
0 %
Second PID reference activated by a digital signal.
P3-16 Pump Prime Time
0 sec
≠ 0: Burst pipe protection function enabled.
If PID feedback, when starting motor, is not > P3-17 within time P3-16 the
drive will trip with "Pr-Lo" (pressure low trip).
P3-17 Burst Pipe Threshold
0 %
% of PID feedback signal. See P3-16.
P3-19
Burst Pipe Detection Trip
Delay
0 sec
Delay/filtering false trip due to overshoot or undershoot of sensor signal.
For instance pressure shocks due to valves going on and off.
P3-18 PID Reset Control
0
0: PID loop will continue running as long as P gain (P3-
01) ≠ 0.
1: PID loop will only run when drive is enabled. If drive is not running, PID
output will reset to 0 (Including integral result).
P2-07
Boost function at start
0 Hz
Drive can be started with speed in P2-07 without PID active. When time
from start in P6-11 has elapsed the drive enters automaticall PID-control.
P6-11
0 sec
If PID-control is to be performed by serial, Fieldbus or Ethernet, contact Beijer Electronics.