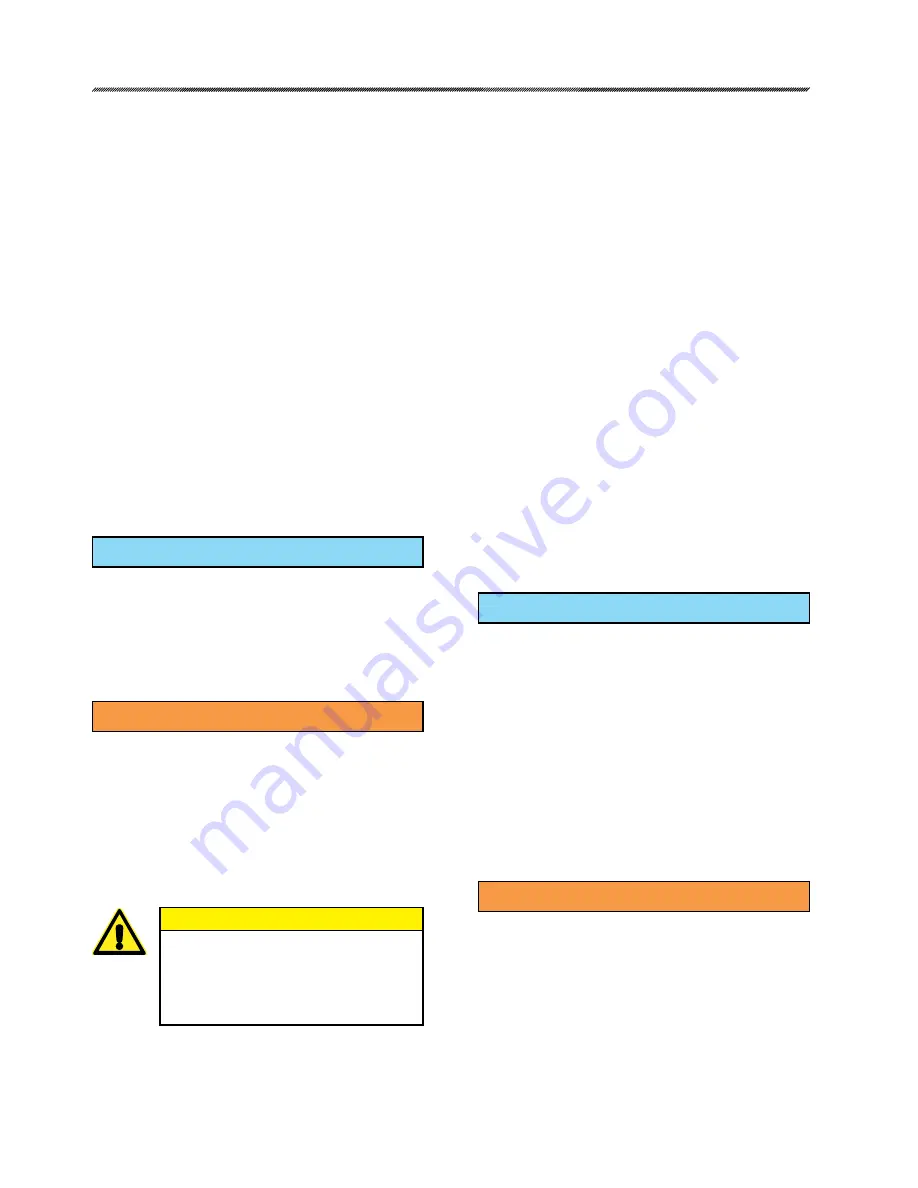
80-4280-10, Rev. 4
33
STEP SIZE
Step size represents the minimum amount
that the Demand signal must change to initiate a
change in actuator position.
When the actuator is in AUTO mode, the
DCM-2 runs the motor until the output shaft
position matches the Demand signal. When they
match, power is removed from the motor. The
Demand signal must change by at least the step
size before power is returned to the motor.
The step size is factory set at 0.15% of
span unless otherwise specified at the time of
order. The step size is adjustable from 0.1% to
2.5% when the actuator is configured for 100
degrees of travel, but adjustment is typically not
required. The minimum step size regardless of
travel is 0.1°. It may be advantageous in certain
applications where noise or other problems
exist, to increase the step size slightly to prevent
excessive modulation.
The step size can be changed using the
following methods.
HART
method
HART DD Menu Location: MENU 5A
Functions> Configuration> General Setup
Command: Step Size
Enter the step size as a decimal percentage of
span and transmit the data to the DCM-2 to
execute the change.
SERIAL
command method
Command: stepsize
Arguments:
#.##%
: Enter the stepsize as a
percentage of travel span. (e.g.: “stepsize 0.15%”
for 0.15% of travel span OR “stepsize 0.15” for
0.15 degrees of travel span)
Note: If the percent (%) symbol is left off of the
command, the DCM-2 will consider the unit to be
degrees instead of percent.
CAUTION
The following procedures could
cause the actuator to reposition,
which can adversely affect the
process and cause potentially
dangerous conditions.
STALL PROTECTION
The DCM-2 board provides protection of
the actuator motor and gearing in the event of a
stall condition. A stall condition occurs when the
actuator is attempting but is unable to move to a
desired position for a defined period of time due to
a mechanical impediment or excessive load.
The DCM-2 senses that the actuator is unable
to balance by monitoring the current applied to the
motor windings. If the current is continuously applied
to one motor winding longer than the configured
“stall time”, the actuator shuts off motor power and
prevents further actuator movement. When this
occurs, the STAT and STALL LEDs will illuminate.
Resetting the actuator and restoring normal
operation is achieved by reversing the Demand
signal to the drive, submitting a reset command via
HART or Serial port, or cycling the actuator power.
The stall protection feature can be enabled
or disabled and the stall time may be configured
between 30 and 300 seconds. This feature is factory
enabled and set for 300 seconds. If reconfiguring,
it is advisable to configure the stall timer with a
value greater than the maximum stroke time to
avoid false stall alarms. The following methods are
available to configure the stall protection feature.
HART
method
HART DD Menu Location: MENU 5A
Functions> Configuration> General Setup
Command: StallProt
Selections:
Enabled -
Select to enable stall protection.
Disabled -
Select to disable stall protection.
Command: Stall Time
Enter the stall time in seconds as an integer. Valid
stall times are between 30 - 300 seconds.
HART DD Menu Location: MENU 7
Functions> Manual Operation
Command: Reset Stall
Running this function will reset a stall condition.
SERIAL
command method
Command: stallprot
Arguments:
0:
Disabled (Motor continues to run if stalled.)
1:
Enabled (Power removed from motor if stalled.)
(e.g.: “stallprot 1” enables stall protection)
Command: stalltime
Arguments:
###: Enter the stall time in seconds
as an integer. Valid stall times are between 30 -
300 seconds. (e.g.: “stalltime 45”)
Command: unstall
- resets a stall condition.