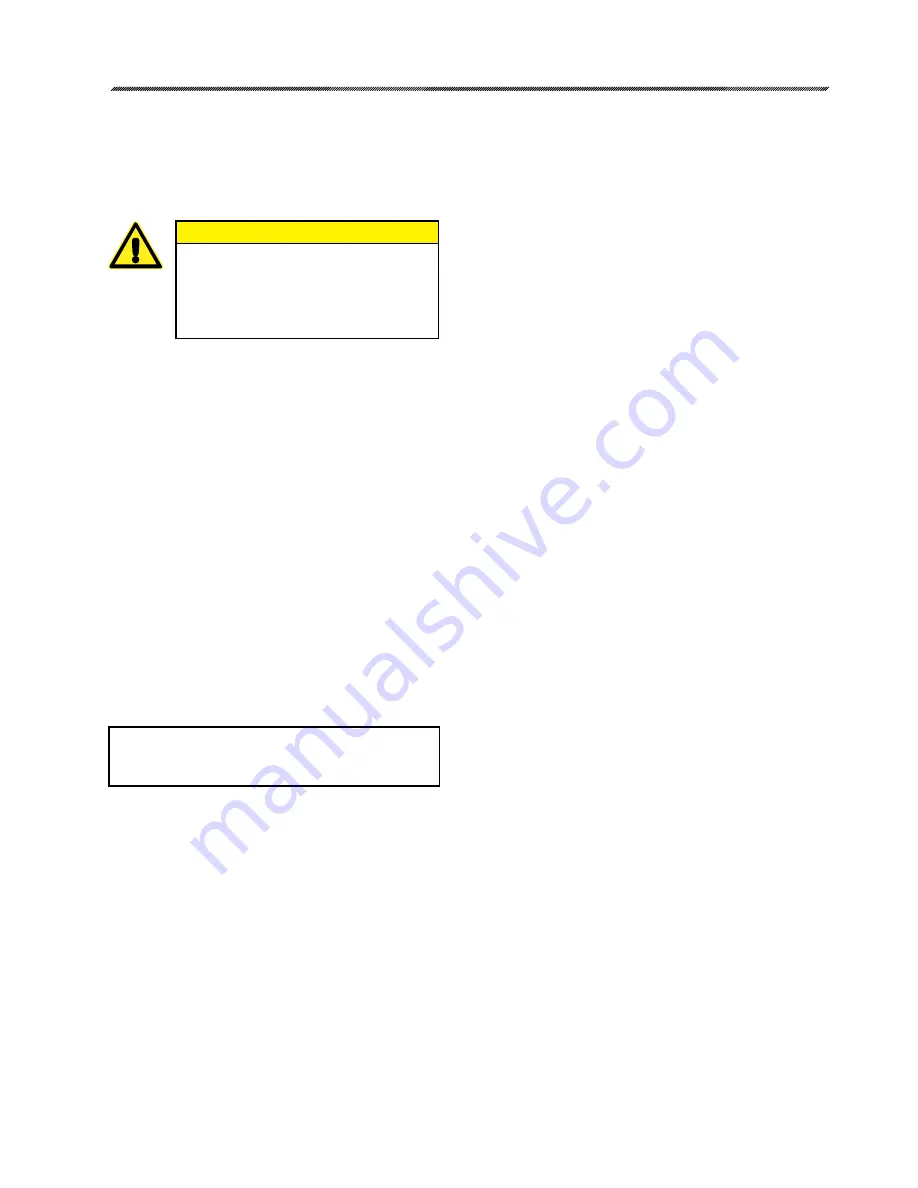
80
80-1403-01, Rev. 3
MOTOR
The control motor is not field-repairable.
Dis assembly of the motor will result in a loss of
torque that can only be restored by returning the
motor to the factory for remagnetizing.
CAUTION
Before removing the motor
assembly, while the process is
running, block the valve stem to
prevent the gear train from moving
when the motor is removed.
To remove the motor, first disconnect the
motor wires in the terminal compartment of the
actuator. The wiring is under the terminal board.
Remove the black wire from the terminal post, cut
the green motor wire near the green-yellow-red
butt joint and disconnect the red wire from the
re-green-blue butt connection. Remove the
hardware that secures the motor (model 14-10_
has three 10-32 socket head cap screws and
model 14-20_ has four 1/4-20 hex head bolts).
Carefully slide the motor out of the actuator body.
To install the motor, insert the three-wire
sleeve through the wire hole in the motor mount
and into the terminal compartment. Carefully
slide the motor into the actuator body, rotate the
motor shaft if necessary to engage the pinion with
the first combination gear. Install motor mounting
hardware (10-32 screws at 20 lb-in (2.26 N•m) or
1/4-20 bolts at 6 lb-ft (8.13 N•m)). Reconnect the
motor wires.
NOTE: 14-100 models with 4 and 8 second
timing have a spacer between the motor and
gear module.
MOTOR RESISTOR AND
CAPACITOR
The motor resistor assembly and capacitor
are located in the top compartment beside
the Calibar. To replace a resistor or capacitor,
remove the top cover (15/16” bolt head). Remove
the existing part and transfer the wires one at a
time to the replacement part. Inspect the top
cover gasket and replace if necessary. Replace
the top cover. Tighten the top cover bolt just
enough to compress the O-ring seal.
OVER-TRAVEL LIMIT AND
AUXILIARY SWITCHES
Complete switch assemblies may be
replaced. It is not possible to replace individual
switches. To replace switch assemblies, remove
the top cover (15/16” bolt head). Remove the
#6-32 socket head cap screws holding the switch
assembly to the plate.
Transfer the wires one at a time to the
replacement assembly using the push-on lugs
provided. Install the replacement assembly and
note that it rotates around one screw to permit
an adjustment of the cam-to-roller spacing and
switch operating point. To properly set the switch,
use a .030” (.76 mm) shim between the cam and
switch lever and loosely position the switch
assembly so that the switch is just actuated. The
switch lever should be on the low or minimum
radius portion of the cam when setting the
switches. DO NOT overstress the switch lever.
Tighten both screws to 10 Ib-in (1.13 N•m) torque
and remove the shim. When properly adjusted,
the switch lever should remain in contact with the
cam throughout the actuator travel.
ADDING SWITCHES
It is possible to add two additional switches to
an actuator in the field. Consult the factory, giving
the actuator model and serial number so that a
correct list of parts required may be supplied to you.
Remove the top cover (15/16” bolt head).
Install wiring onto the switch push-on lugs and
route the wires into the actuator terminal area.
Remove the terminal cover and solder wires to the
underside of the terminal assembly according to
the wiring diagram included with the new switch
assembly. Install the new switch assembly and
adjust according to the instructions above. See
table on page 83 for switch assembly part numbers.
SELF-LOCKING MECHANISM
(SLM)
In normal service, the SLM friction surface
should not require replacement; however, a
combination of excessive modulation and load
can cause wear to the SLM mechanism. If
the SLM has been damaged, rebuild kits are
available (see table at right).
SLM Rebuild Kits typically consist of a spring,
spring pin, thrust bearing, pinion, steel balls,
locking disc, steel shims, control motor gasket,
terminal joints, and instruction sheet.
See the figure at right for identification of
typical SLM components.
MAINTENANCE
Component Replacement
Содержание 14-100
Страница 85: ...85 80 1403 01 Rev 3 17 18 2 1 6 5 8 6 3 4 9 14 15 25 7 16 CONTROL ASSEMBLY AND DRIVE TRAIN...
Страница 87: ...87 80 1403 01 Rev 3 14 15 17 18 2 1 6 5 8 6 3 4 9 14 15 25 7 16 CONTROL ASSEMBLY AND DRIVE TRAIN...
Страница 90: ...90 80 1403 01 Rev 3 NOTES...
Страница 91: ...91 80 1403 01 Rev 3...