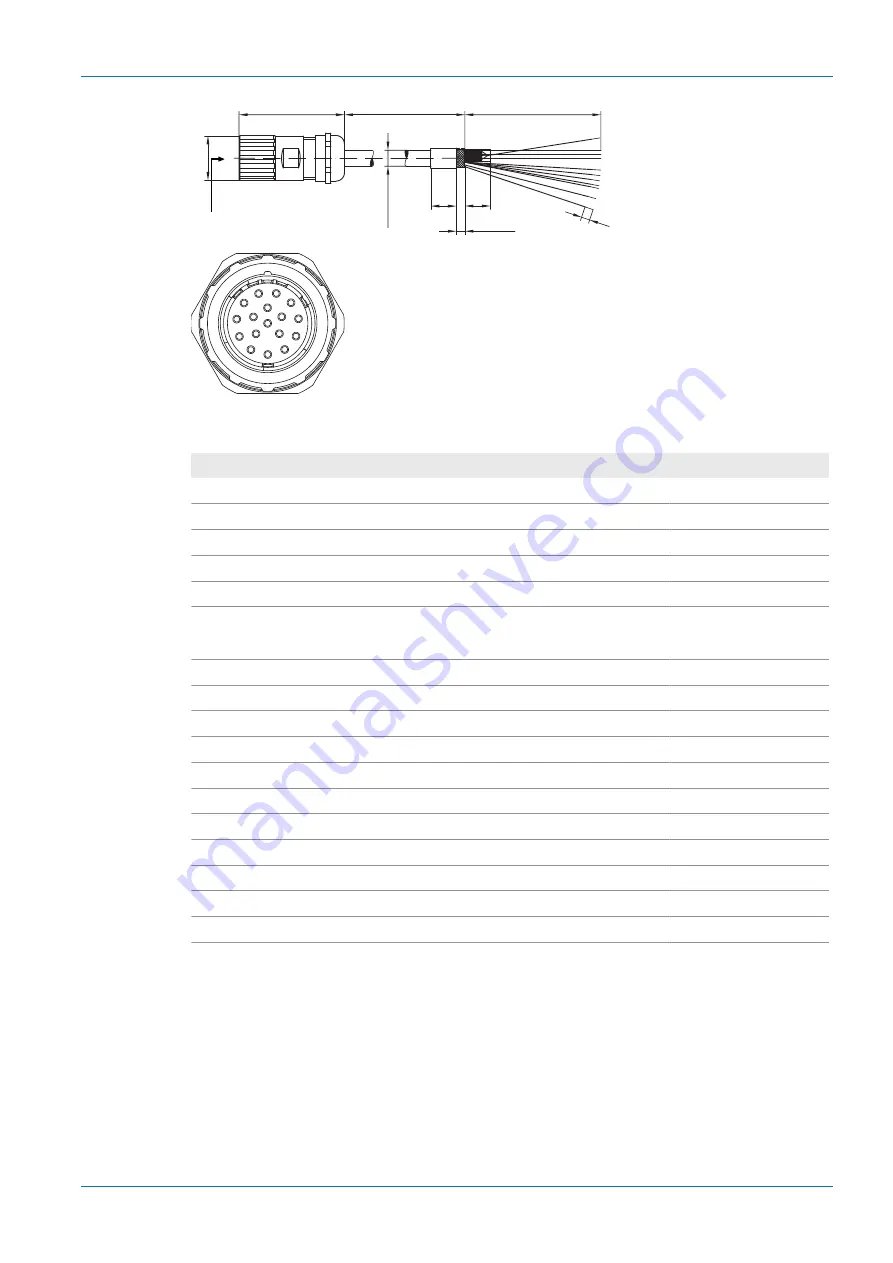
Baumer Hübner
Electrical installation
|
6
V1, T1 | HMG10 & HMG10P SSI
Operating Manual
39
X
ø
2
6
.2
mm
ø
9
.4
mm
62 mm
L ±0.5%
80 ±5 mm
~15 mm
~15 mm
~5 mm
5 mm
8
7
6
5
4
3
2
1
9
17
13
16
14
15
10
11
View X
17-pin
PIN
Core color
Core cross-section
Assignment HMG10
1
---
---
---
2
White/yellow
0,14 mm
2
DIR
3
Black
0,14 mm
2
SB
I
4
---
---
---
5
White/black
0,14 mm
2
PRE
6
Brown
0,14 mm
2
SA
I
7
Brown/red
0,5 mm
2
Ub
8
Green/red
0,22 mm
2
C+
9
Green/black
0,22 mm
2
C−
10
Brown/blue
0,5 mm
2
0V
11
II
Black
0,5 mm
2
---
12
---
---
---
13
---
---
---
14
Brown/yellow
0,22 mm
2
D+
15
---
---
---
16
---
---
---
17
Brown/green
0,22 mm
2
D−
I
Programming interface (programmable product variant only)
II
Internal shield, interconnected with each internal shield
Also see about this
2