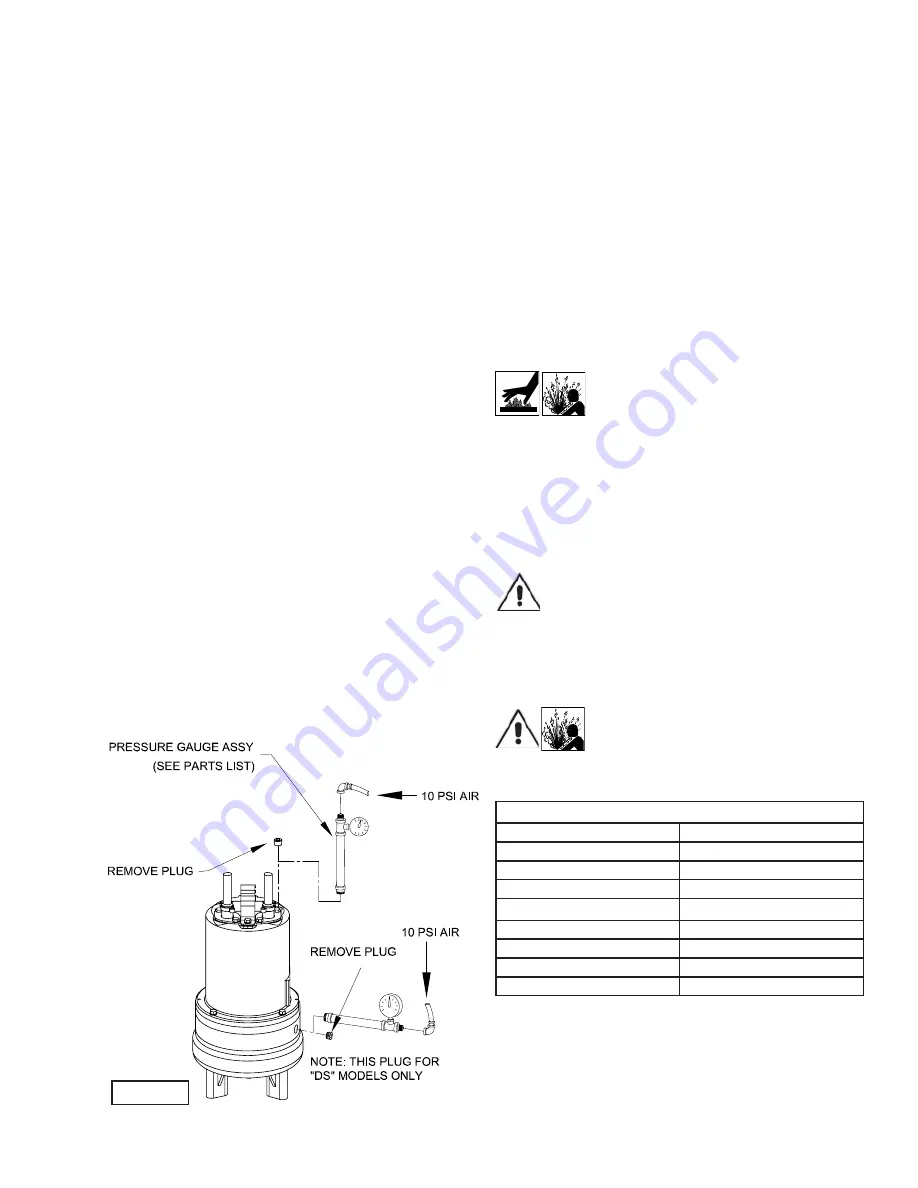
9
FIGURE 3
F-1.1) Checking Oil:
Motor Housing-
To check oil, set unit upright. Remove pipe
plug (39) from housing (6). With a fl ashlight, visually inspect the
oil in the motor housing (6) to make sure it is clean and clear,
light amber in color and free from suspended particles. Milky
white oil indicates the presence of water. Oil level should be just
above the motor when pump is in vertical position.
F-1.2) Testing Oil:
1.) Place pump on it’s side, remove pipe plug (39), from motor
housing (6) and drain oil into a clean, dry container.
2.) Check oil for contamination using an oil tester with a
range to 30 Kilovolts breakdown.
3.) If oil is found to be clean and uncontaminated (measuring
above 15 KV. breakdown), refi ll the motor housing as per
section F-1.4.
4.) If oil is found to be dirty or contaminated (or measures
below 15 KV. breakdown), the the pump must be carefully
inspected for leaks at the shaft seal (28), cable assemblies
(16) and (56 if used), square ring (27) and pipe plug (39),
before
refi lling with oil. To locate the leak, perform a
pressure test as per section F-1.3. After leak is repaired,
dispose of old oil properly, and refi ll with new oil
as per section F-1.4.
F-1.3) Pressure Test:
Pumps that have been disassembled, Motor Housing-
If the
pump has been disassembled, the oil should be drained before
a pressure test, as described in section F-1.1. Remove pipe
plug (39) from motor housing (6). Apply pipe sealant to pressure
gauge assembly and tighten into hole (See Figure 3). Pressurize
motor housing to 10 P.S.I. Use soap solution around the sealed
areas and inspect joints for “air bubbles”.
If, after fi ve minutes, the pressure is still holding constant, and no
“bubbles” are observed, slowly bleed the pressure and remove
the gauge assembly. Replace oil as described in section F-1.4.
If the pressure does not hold, then the leak must be located and
repaired.
Pumps that have NOT been disassembled, Motor Housing
-
The pressure test may be done with the oil at its normal level.
Remove pipe plug (39) from motor housing (6). Apply pipe
sealant to pressure gauge assembly and tighten into hole (see
Figure 3). Pressurize motor housing to 10 P.S.I. Use soap
solution around the sealed areas above the oil level and inspect
joints for “air bubbles”. For sealed areas below the oil level,
leaks will seep oil.
If, after fi ve minutes, the pressure is still holding constant, and
no “bubbles”/oil seepage is observed, slowly bleed the pressure
and remove the gauge assembly. If the pressure does not hold,
then the leak must be located and repaired.
Seal Chamber (DS Units Only)-
Set unit on its side with fi ll
plug (44) downward, remove plug (44) and drain all oil from
seal chamber. Apply pipe sealant to pressure gauge assembly
and tighten into hole in outer seal plate (29). Pressurize seal
chamber to 10 P.S.I. and check for leaks as outlined above.
CAUTION ! - Pressure builds up extremely
fast, increase pressure by “TAPPING” air
nozzle. Too much pressure will damage
seal. DO NOT exceed 10 P.S.I.
F-1.4) Replacing Oil:
Motor Housing-
Set unit upright and refi ll with new cooling oil
as per Table 1 (see parts list for amount). Fill to just above motor
as an air space must remain in the top of the motor housing to
compensate for oil expansion (see Figures 15 & 17). Apply pipe
thread compound to threads of pipe plug (39) then assemble to
motor housing (6).
IMPORTANT! - For single phase units, oil level
should be below capacitor.
Seal Chamber (DS Units Only)-
Set unit on its side, with plug
(44) upward, and refi ll with new oil as per Table 1 (see parts
list for amount). Apply pipe thread compound to threads of pipe
plug (44) and assemble to outer seal plate (29).
WARNING ! - DO NOT overfi ll oil.
Overfi lling of motor housing with oil can
create excessive and dangerous hydraulic
pressure which can destroy the pump and
create a hazard. Overfi lling oil voids warranty.
TABLE 1 - COOLING OIL - Dielectric
SUPPLIER
GRADE
BP
Enerpar SE100
Conoco
Pale Paraffi n 22
Mobile
D.T.E. Oil Light
G & G Oil
Circulating 22
Imperial Oil
Voltesso-35
Shell Canada
Transformer-10
Texaco
Diala-Oil-AX
Woco
Premium 100
F-2) Impeller and Volute Service:
F-2.1) Disassembly and Inspection:
To clean out volute (1) or replace impeller (33), disconnect
power, remove hex bolts (26), and lockwasher (12), vertically
lift motor and seal plate assembly from volute (1) see Figure
4.
Содержание 4SE-DS series
Страница 14: ...14 FIGURE 13 CONTIUED...
Страница 16: ...16 FIGURE 15 4SE L Series Single Seal...
Страница 17: ...17 FIGURE 16 4SE L Series Single Seal...
Страница 18: ...18 FIGURE 17 4SE DS Series Double Seal...
Страница 19: ...19 FIGURE 18 4SE DS Series Double Seal...