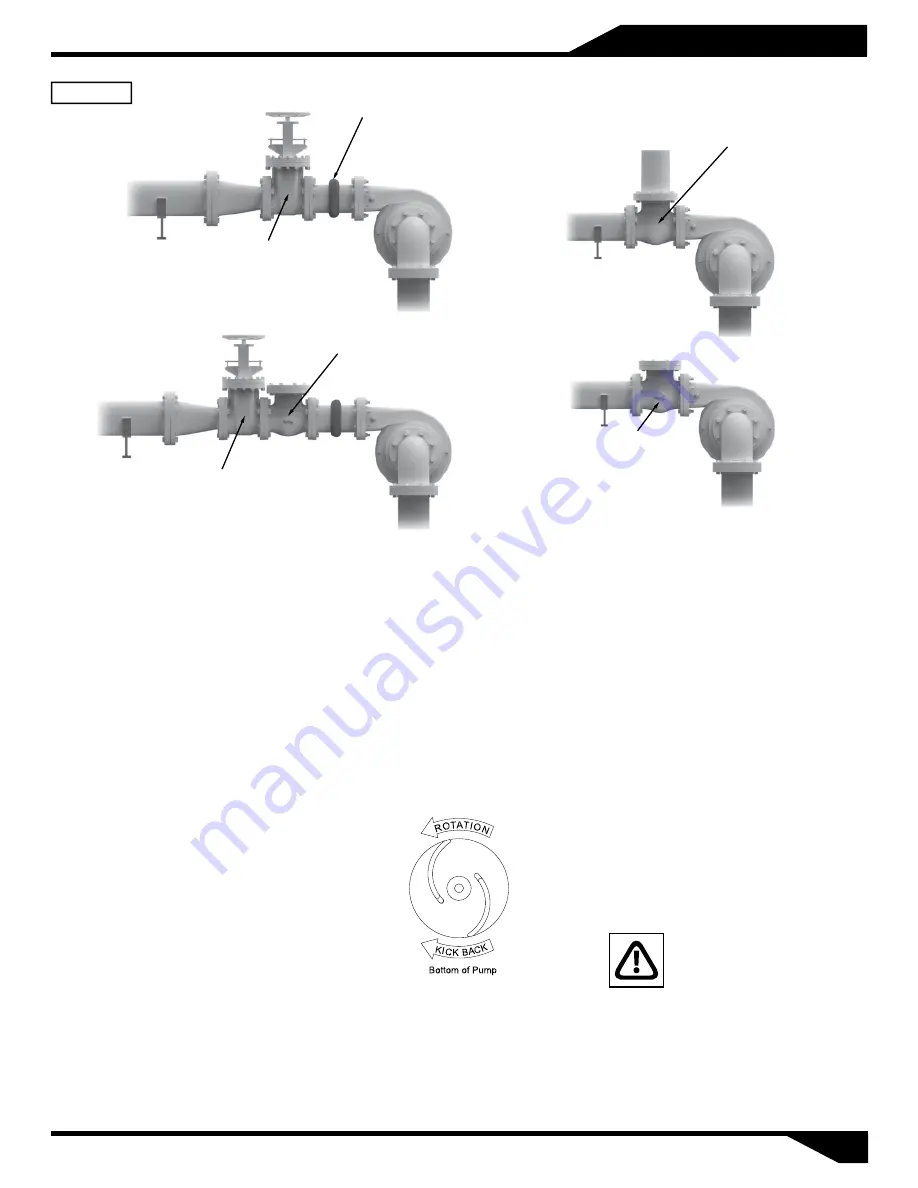
Due to the cost of energy or BHP
necessary to overcome the friction
generated by using a smaller
diameter pipe, a larger diameter
discharge pipe is commonly used
than the required by the volute or
body.
07
Installation & Operation
In order to determine the optimal
size of the piping, compare the total
cost of the equipment's operation
(cost
of
the
pump,
control
equipment, piping and energy
consumption). By increasing the
discharge diameter reasonably, it
reduces the required BHP due to the
low friction. Perform different tests
using several piping diameters until
you find the more convenient.
The pipe, valves, etc. should be
perfectly align with the volutes
suction and discharge centerlines,
this to avoid any excessive loads on
the pumps volute. If needed, install
new expansive joints to protect the
pump from excessive thermal or
pressure forces.
Safety shutoff
valve
Swing check valve
could cause a
“water hammer”
Expansive
joint
Service valve.
Service valve
Retarded action
check valve
INCORRECT
CORRECT
Figure 6
Discharge piping.
Install the foot valve at the suction
pipe (Figure 1) and fill with liquid the
superior part of the pump´s body.
Sometimes air is trapped inside the
body, to remove it you should uncap
the male plug until the liquids spills
out. Re-install the male plug using a
sealant.
IMPORTANT! - Do not
operate pump without
priming first. Operating dry
will damage seal.
Pre-Operation
1.
C
heck Voltage and Phase -
Compare the voltage and phase
information stamped on the
pump name plate.
2.
Check
Pump Rotation -
Improper
motor rotation can result in poor
pump performance and can
damage the motor and/or pump.
Check rotation on three phase
units by momentarily applying
power and observe the "kickback".
4.
P
riming -
Every centrifugal pump
must be primed (suction pipe and
pump´s body should have liquid),
before operating.
Kickback should always be in a
counter-clockwise
direction
as
viewed from motor end or opposite
to impeller rotation. Impeller rotation
is counter-clockwise as viewed from
bottom of pump.
3.
N
ame Plate -
Record the
information from the pump name
plate to drawing in front of manual
for future reference.
barmesapumps.com