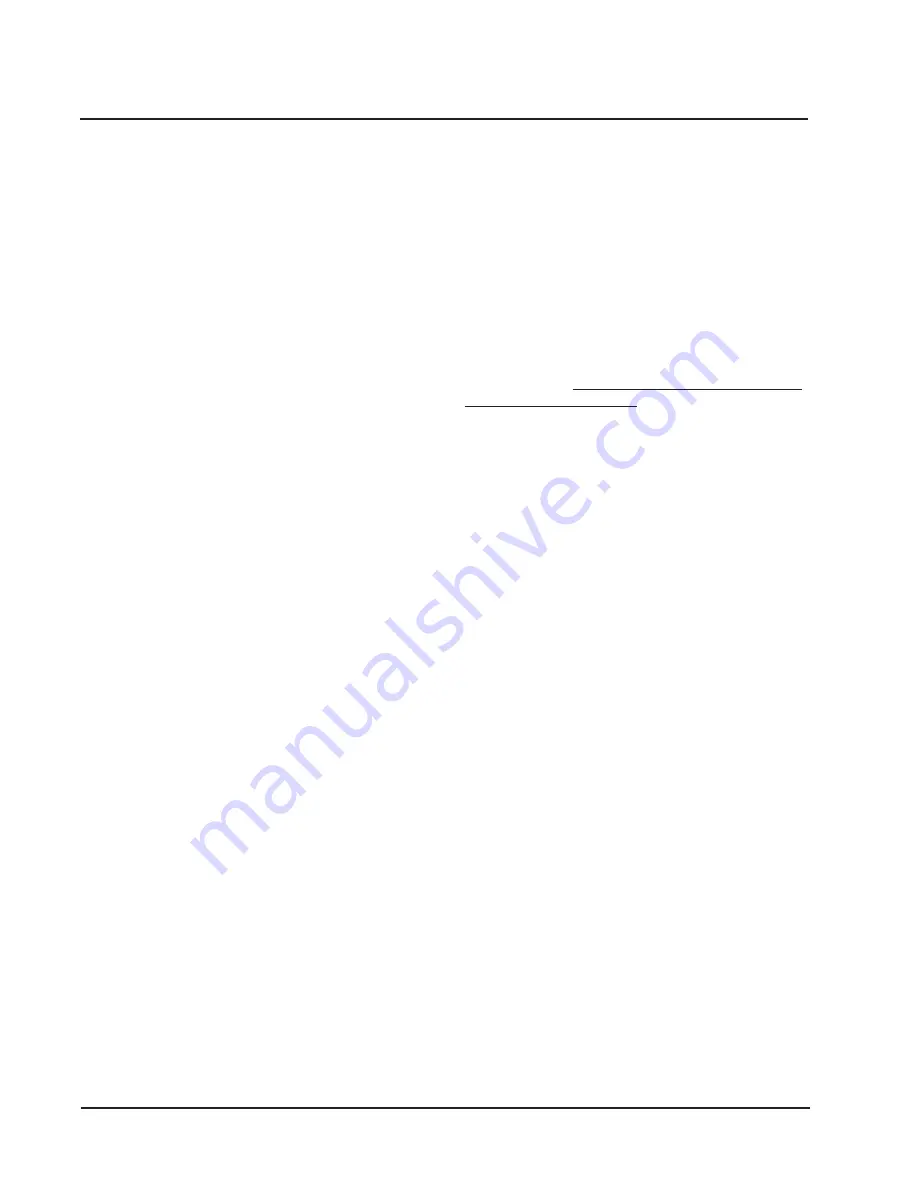
Manual 2100-519C
Page
28 of 42
START UP
DESCRIPTION OF STANDARD
EQUIPMENT
Solid State Electronic Heat Pump Control
Provides efficient 30-minute defrost cycle. A thermistor
sensor and speed up terminal for service along with a
10-minute defrost override are standard on the electronic
heat pump control.
High / Low Pressure Switch
Provides refrigerant circuit high pressure and loss of
charge protection. Includes lockout circuit that is
resettable from room thermostat.
Five Minute Compressor Time Delay
Provides short cycle protection for the compressor
which extends compressor life. Built into the electronic
heat pump control as standard.
Service Light
One service light indicates when service is required.
• Check System – detects high or low pressure
switch operation for compressor protection.
OPTIONAL CFM (Q36H1, Q42H1, Q48H1
AND Q60H1 ONLY)
These units are shipped from the factory set to operate at
the optional CFM level shown in Table 9. This provides
lower operating sound levels for non-ducted, free
discharge applications. This CFM level will reduce the
system capacity performance by approximately 2% at
the same energy efficiency.
Rated CFM is required for ducted applications for
maximum performance rating. To obtain full CFM on
these models, connect jumper wire as follows:
1. Disconnect all power to the unit. Failure to do so
may result in damage to the motor.
2. Open return air service panel
3. Open inner control panel cover
4. Locate low voltage terminal strip. There is a pink
jumper wire with both ends attached to terminal
marked “G2”. Move one end of this jumper to
terminal “Y”.
5. Reverse steps to reassemble.
IMPORTANT INSTALLER NOTE
For improved start-up performance, wash the indoor coil
with a dishwasher detergent.
PHASE MONITOR
All units with three phase scroll compressors are
equipped with a 3 phase line monitor to prevent
compressor damage due to phase reversal.
The phase monitor in this unit is equipped with two
LEDs. If the Y signal is present at the phase monitor
and phases are correct the green LED will light and the
compressor contactor is allowed to energize.
If phases are reversed, the red fault LED will be lit and
compressor operation is inhibited.
If a fault condition occurs, reverse two of the supply
leads to the unit. Do not reverse any of the unit factory
wires as damage may occur.
THREE PHASE SCROLL COMPRESSOR
START UP INFORMATION
Scroll compressors, like several other types of
compressors, will only compress in one rotational
direction. Direction of rotation is not an issue with
single phase compressors since they will always start
and run in the proper direction.
However, three phase compressors will rotate in either
direction depending upon phasing of the power. Since
there is a 50-50 chance of connecting power in such a
way as to cause rotation in the reverse direction,
verification of proper rotation must be made.
Verification of proper rotation direction is made by
observing that suction pressure drops and discharge
pressure rises when the compressor is energized.
Reverse rotation also results in an elevated sound level
over that with correct rotation, as well as, substantially
reduced current draw compared to tabulated values.
Verification of proper rotation must be made at the
time the equipment is put into service. If improper
rotation is corrected at this time there will be no
negative impact on the durability of the compressor.
However, reverse operation for even one hour may
have a negative impact on the bearing due to oil pump
out.
All three phase scroll compressors used in the QT
EC
series are wired identically internally. As a result, once
the correct phasing is determined for a specific system
or installation, connecting properly phased power leads
to the same Fusite terminal should maintain proper
rotation direction. The direction of rotation of the motor
may be changed by reversing any two line connections
to the unit.
Содержание Q-TEC Q24H1
Страница 6: ...Manual 2100 519C Page 6 of 42 FIGURE 1 UNIT DIMENSIONS Q24H1 Q30H1 Q36H1 Q42H1 Q48H1 Q60H1...
Страница 9: ...Manual 2100 519C Page 9 of 42 FIGURE 6 DUCTEDAPPLICATION FIGURE 5 INSTALLATION WITH FREE BLOW PLENUM...
Страница 13: ...Manual 2100 519C Page 13 of 42 MIS 2469 DRAIN BOX WALL SLEEVE OVERFLOW TUBE CAULK AROUND TUBE FIGURE 12A...
Страница 15: ...Manual 2100 519C Page 15 of 42 REMOVE KNOCK OUT FOR INDOOR DRAIN HOSE CONNECTOR MIS 2471 FIGURE 12C If Used...
Страница 31: ...Manual 2100 519C Page 31 of 42 FIGURE 21 FRESH AIR DAMPER REMOVAL MOUNTING SCREW...