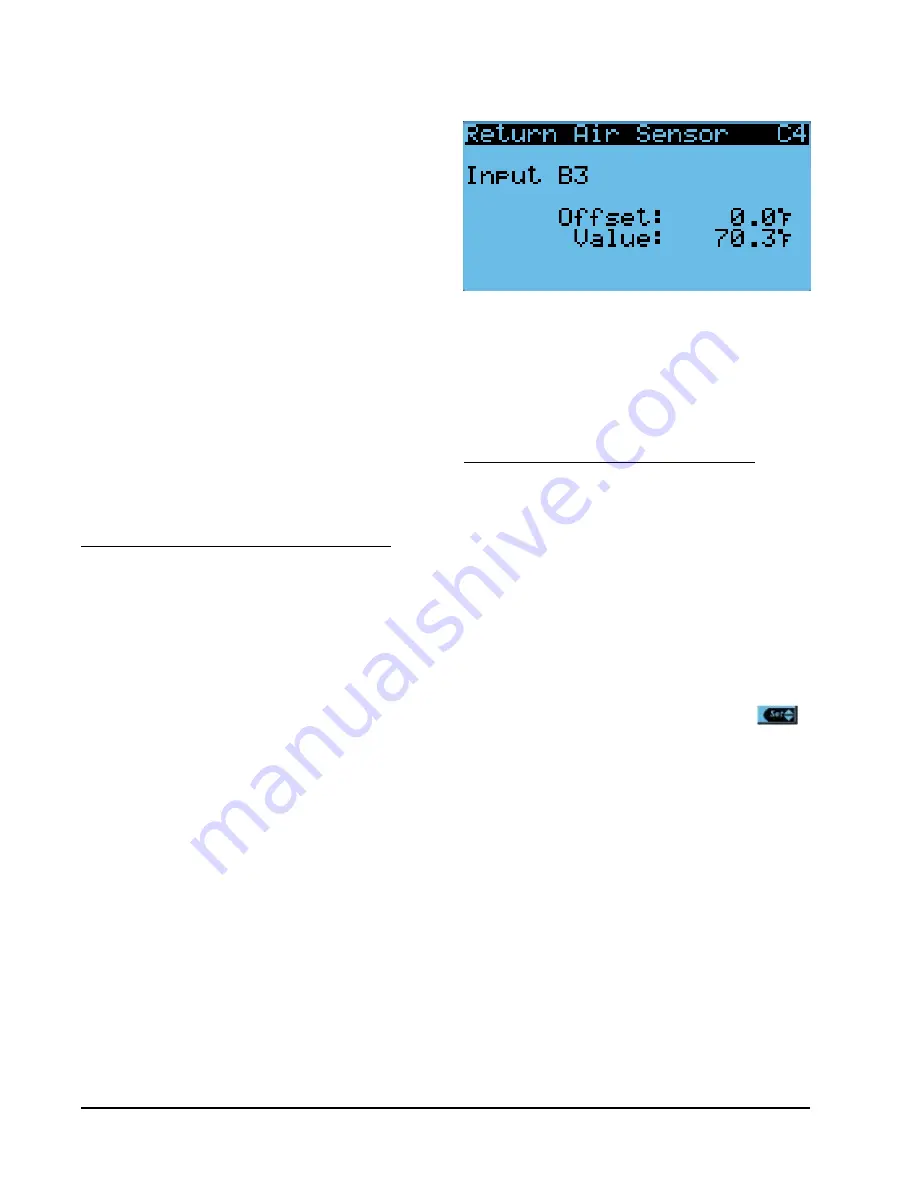
Manual 2100-694B
Page
14 of 62
mode, no auxiliary temperature measurement devices
are required for operation. The wall-mount unit
automatically uses a continuous blower setting to
circulate room air into the return air inlet and uses
the return air temperature sensor to control room
temperature.
To change default setpoints, refer to
Setpoints
on page 8.
During installation, the ability to run in orphan mode
allows deactivation of one of the existing, older wall-
mount units, while keeping the shelter cool with the
other unit still operating. Once the first of the Bard
FUSION-TEC HR Series wall-mount units is installed
and powered on, it will operate in orphan mode—
keeping the climate inside the shelter stable and
the installers comfortable while the remainder of the
older equipment is removed and the remaining Bard
FUSION-TEC HR Series wall-mount units and LV1000
controller are installed.
Additionally, should any or all of the FUSION-TEC HR
Series wall-mount units lose communication with the
LV1000 controller (such as during maintenance), they
will continue to serve the shelter’s needs until a repair
can be made.
Temperature/Humidity Control
Temperature/Humidity Control Components
Return Air Temperature Sensor
The unit is equipped with a return air temperature
sensor to monitor the space temperature when the unit
is in orphan mode. The return air sensor is located
in the upper part of the return opening in such a way
that it is exposed to the entering airstream. An alarm
signal will be sent to the LV controller if the return air
temperature sensor is disconnected. The temperature is
measured with a 10k ohm NTC thermistor.
This sensor can be verified and adjusted by:
1. Press MENU key to go to the Main Menu screen.
2. Press UP or DOWN keys and ENTER key to enter
TECHNICIAN password 1313.
3. Press UP or DOWN keys to scroll to
I/O Config
;
press ENTER key.
4. Press UP or DOWN keys to scroll to
Return Air
Sensor C4
; press ENTER key.
5. Verify the measurement displayed on screen is
accurate (see Figure 18).
6. If the measurement needs to be adjusted, apply an
offset value by pressing ENTER to scroll to
Offset
.
7. Press UP or DOWN keys to adjust the offset.
8. The update will not take effect until the cursor is
moved out of the
Offset
parameter.
9. Once adjusted, press the ESCAPE key several
times to return to Main Menu screen.
Return Air Temperature Alarm
When the return air temperature sensor value is out of
range (-41.0 to 303.0°F), the controller will generate
a sensor failure alarm to indicate the sensor is not
working properly.
This alarm is fixed and cannot be adjusted.
Temperature/Humidity Control Operation
The unit utilizes a PID control loop for space control.
This control will compare the space temperature to
the space setpoint. Based on how far away from the
setpoint the temperature is, the loop will output a
cooling or heating capacity number between 0 and
100%. The unit will then take all of the available
cooling methods and distribute them evenly across the
0-100% range. The stages are then brought on as the
heating or cooling capacity reaches the percentage that
brings the stages on or off.
There are separate setpoints
for cooling and heating.
To change or view the unit setpoint:
1. From the Status screen, press UP or DOWN key
until Quick Menu displays Setpoints icon ( ).
Press ENTER key.
2. Press ENTER key to scroll to
Cooling
or
Heating
(see Figure 4 on page 8).
3. Press UP or DOWN keys to change the value to
desired heating and/or cooling setpoint.
Cooling
The unit is equipped with 1 stage of freecooling and 2
stages of mechanical cooling (compressor and solenoid)
for a total of 3 cooling stages (see Figure 19).
Cooling w/No Economizer
The unit is equipped with 1 stage of freecooling and
2 stages of mechanical cooling (compressor and
solenoid). However, the outdoor conditions are not
favorable for economizer operation so there are a total
of 2 cooling stages (see Figure 20).
Heating
The unit is equipped with 1 stage of electric heat (see
Figure 21).
FIGURE 18
Adjusting Return Air Sensor