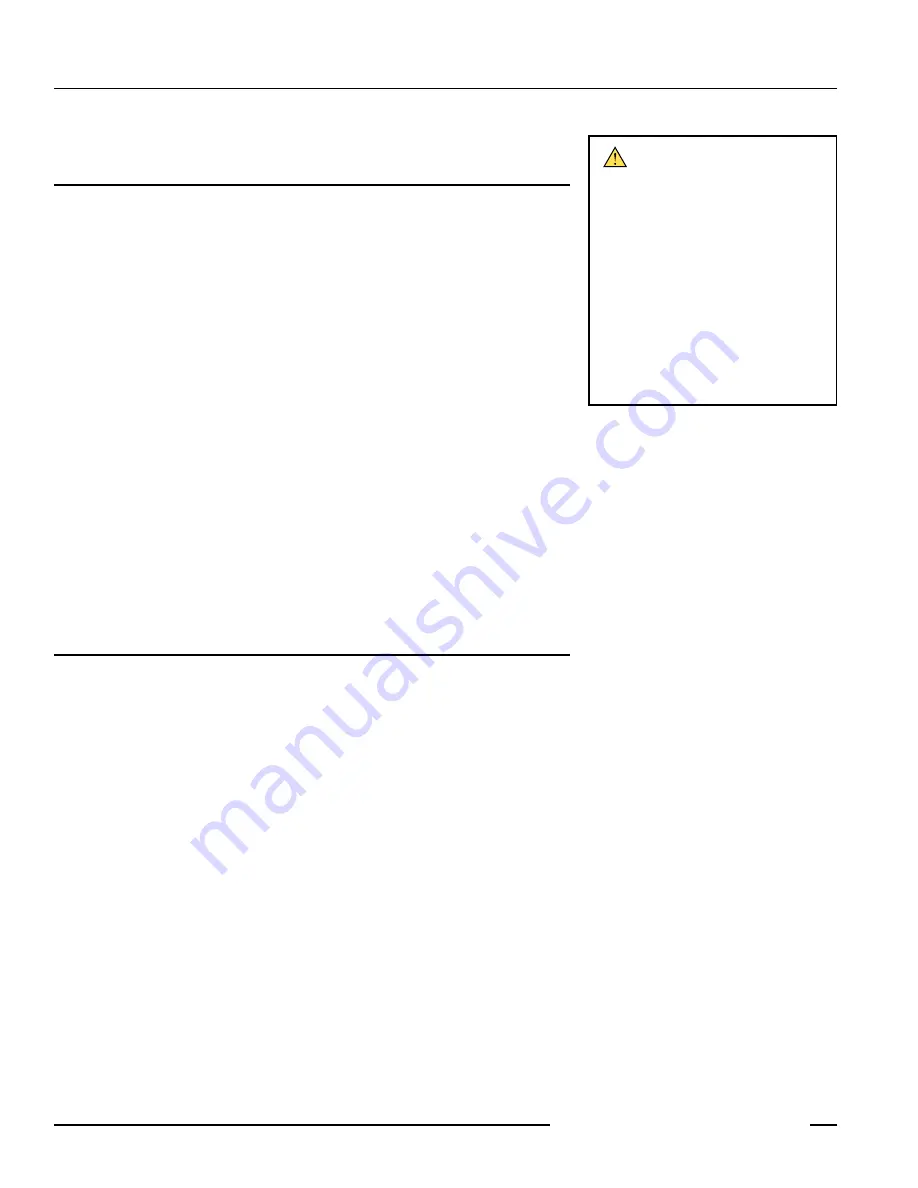
MSC..-1S..E
Supplement: MINI-SCREEN Models with Selectable Trip/Latch Output
P/N 68980
Banner Engineering Corp. • Minneapolis, MN U.S.A.
www.bannerengineering.com • Tel: 763.544.3164
Section 2.10 Addition
2.10(s) External Key Reset
If it is not possible to mount the control box so that it complies with the warning at right, an
external Reset switch must be provided for the installation that can comply with the warning.
The user must supply a means to reset the MINI-SCREEN system if a latch condition occurs
(after clearing an interruption of the defined area in Latch mode), or after a lockout condition
(see Section 5 of the primary instruction manual).
When wiring external switches, the corresponding control box-mounted key reset switches
should be disconnected (or if that is not possible, the keys removed and placed under
supervisory control). The key reset (manual reset) connection is located at TB2 “Key 1” and
“Key 2” (see Figure 20 in the primary manual). If disconnected, loose wires from the Key
Reset switches must be secured (i.e., tape or wire-tie the loose ends) so they do not cause
shorts within the control box.
All reset switches must be located outside the guarded area, where the switch operator has
a full and unobstructed view of the entire guarded area and any associated hazards while the
reset is performed. The reset switch also must not be reachable from within the guarded area
and must be protected (through the use of rings, or guards, for example) against unauthorized
or inadvertent operation.
The reset switch must be a normally open switch that is held closed for approximately 0.5
seconds, and then re-opened to accomplish the reset. In the associated primary instruction
manual, the “RUN” position is the open condition of the switch; the “Reset” position is closed.
The switch must be capable of switching 15 to 50V dc at 20 to 100 mA.
Section 3.2.1 Addition
3.2.1.1(s) Pass-Through Hazards
Methods of Reducing or Eliminating Pass-Through Hazards
The pass-through hazard must be eliminated or reduced to acceptable levels (as determined
by the user) by employing supplemental safeguarding. One solution is to combine perimeter
guarding with area guarding so that an individual is continually sensed while within the
hazardous area. Supplemental safeguards for area guarding include safety mats, area
scanners, and horizontally mounted safety light curtains.
It is also possible to reduce the separation distance by reducing the stopping time of the
machine, or by using a full-length safety light curtain with a small object detection capability
that reduces the Dpf adder. While it is recommended to eliminate the pass-through hazard
altogether, this may not be a viable option due to cell or machine layout, machine capabilities,
cost constraints, environmental, or other application considerations.
An alternate method is to ensure that once the safeguarding device is tripped, resulting in
stopping or removing the hazard, the safeguard will latch in a tripped condition, thus requiring
a deliberate manual action to reset the safeguard. This type of supplemental safeguarding
relies upon the location of the reset switch or actuating control as well as safe work
procedures to prevent unexpected start or restart.
The location of the reset switch or actuating control must be located outside the guarded
area, and provide the switch operator with a full unobstructed view of the entire guarded area
and any associated hazards as the reset is preformed. The reset switch or actuating control
must also be positioned so it cannot be reached from within the guarded area and must be
protected against unintended or inadvertent operation (e.g., rings or guards).
WARNING . . .
Reset
Switch Location
Reset switch(es) must be accessible
only from outside, and in full view of,
the hazardous area. Reset switches
must also be out of reach from within
the safeguarded area, and must be
protected against unauthorized or
inadvertent operation (e.g., through the
use of rings or guards). If any areas are
not visible from the Reset switch, additional
means of safeguarding must be provided as
described by the ANSI B11 series of safety
requirements or other appropriate standards.