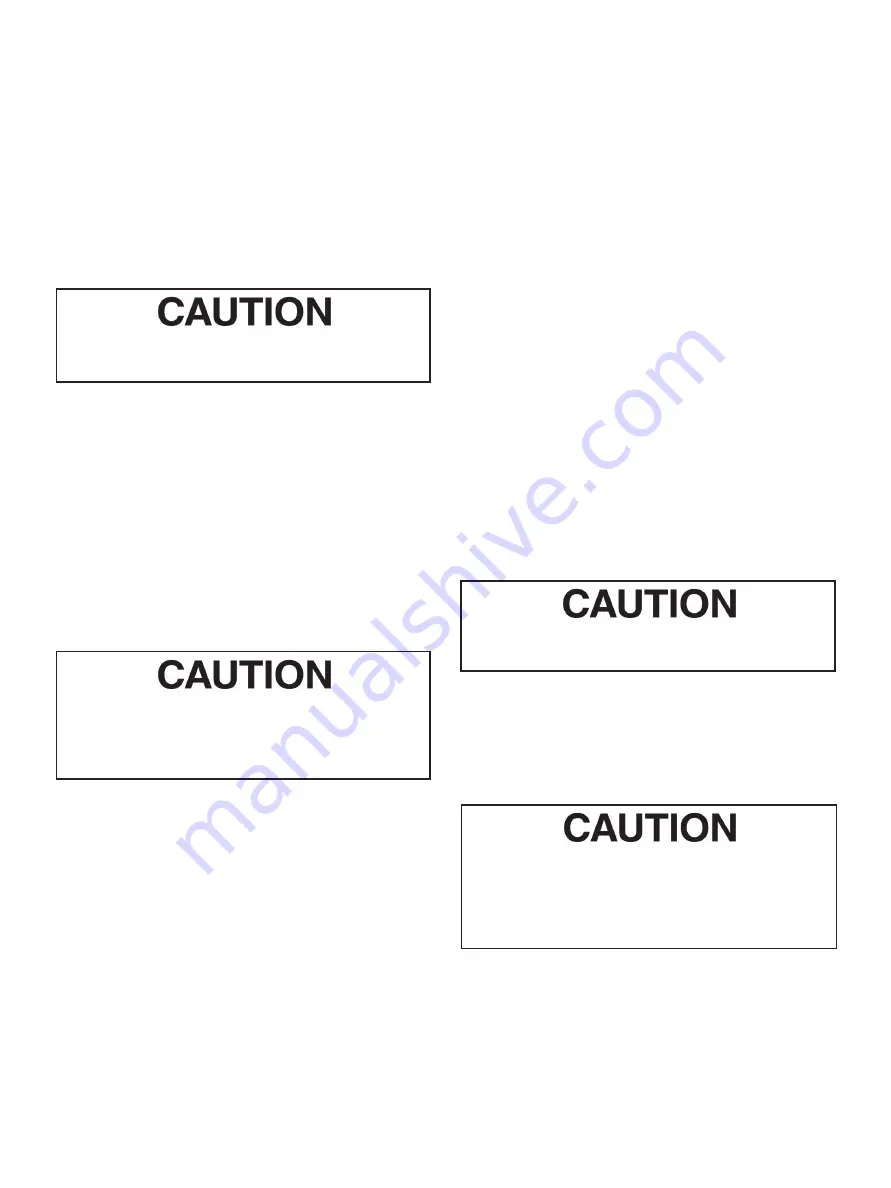
5 | Baker Hughes
Copyright 2020 Baker Hughes Company. All rights reserved.
D.
Remove the adjustable indicator (88) by removing the two
screws (89).
E.
Loosen handwheel lock (52) and turn handwheel (53) so it
does not interfere with the movement of the lever (34).
Note: On valves supplied with the optional limit stop,
(Figure 17) loosen nut (78) and back off the limit stop
screw (77) so it will not interfere with the movement of
the lever (34).
F.
Connect an air line to the actuator supply port and using a
manual loading panel or regulated air supply, apply enough
air pressure to the actuator so the lever will move to an
intermediate position.
Do not exceed pressure listed in Figure 14 for actua-
tor used. Do not use handwheel to move the lever.
Note: If the valve is to be reassembled using the same
orientation, it is recommended that the yoke (33) and
lever (34) alignment, in the closed position, be marked
to simplify reassembly and alignment of the lever and
shaft to ensure proper valve functioning. See Figure 17.
G.
Remove clevis pin clips (5).
H.
Remove clevis pin (7).
I.
Relieve air pressure from actuator enabling clevis (35) to
disengage from lever (34).
Note: If the valve is equipped with a positioner, refer to
the appropriate positioner instruction for procedures
on cam or lever removal. Then proceed to step K.
J.
Remove shaft cover (9) by removing cover screw (10).
Depending on the size and weight of the actuator. It
is recommended that proper lift and support proce-
dures be utilized when removing the spring barrel or
yoke.
K.
Ensure spring barrel is properly supported.
L.
Loosen and remove cap screws (36) and lock washers (37),
then remove spring barrel (38).
M.
Loosen lever capscrew (49).
N.
Loosen the stud nuts (94) and disengage the packing
flange.
O.
Loosen the stud nuts (27) to separate the actuator from the
body S/A.
Note: With body secure, grasp lever and yoke and
separate. Yoke, lever and packing flange are removed
at the same time. The yoke may have to be struck with
a soft face mallet to break it loose.
8.2 Actuator Complete Disassembly
The spring diaphragm actuator used on the Camflex II valve
was designed basically as a low cost non-replaceable item and
therefore disassembly is not recommended. However, in some
instances and for emergency purposes, disassembly may be
required. Proceed as follows.
A.
If the actuator is not removed from the body proceed to the
paragraph 9.1 A. to 9.1 L.
B.
Loosen locknut (46) then remove the clevis (35) and the
locknut (46).
C.
Loosen and remove capscrew (41) and remove dia-phragm
case (42) and diaphragm (40).
D.
Using a deep socket, loosen and remove lock nut (45) and
washer (44).
E.
Remove piston (43) and spring (39) and inspect all
components.
F.
Proceed to section 10.2 for reassembly.
8.3 Valve Body (Refer to Figures 4
and 16)
Maintenance to the internal components required on the Camflex
II Valve can normally be easily determined since the seat ring
and plug can be seen once the valve is removed from the line.
Although it may be determined that the seat ring does not need
replacement, it must be noted that the new plug and seat ring
must be lapped, thus requiring the disassembly of the body. It is
recommended that both seat ring and plug be replaced if one or
the other is damaged due to service.
After the actuator has been removed from the body, dis-
assemble the valve using the following procedure:
Prior to performing maintenance on the valve, isolate
the valve and vent the process pressure.
A.
For 35002 SB (Separable Bonnet) versions, remove
bonnet nuts (104) and lift off bonnet (102) complete with
packing (17) and packing follower (15) from the body as an
assembly. Proceed to step D.
B.
Remove packing follower (15).
C.
Remove safety pin (16).
The purpose of the safety pin is to prevent the shaft
from being pushed out if the yoke is removed while
the valve is still pressurized. The internal compo-
nents of the valve cannot be removed without first
removing the safety pin.
D.
Pull on the shaft (19) to remove it.
Note: Difficulty is sometimes encountered when
removing the shaft from the plug mainly due to an
excessive accumulation of deposits between the plug
splines and the shaft. Application of heat to the plug
shaft bore while using one of the following methods
will facilitate removal.