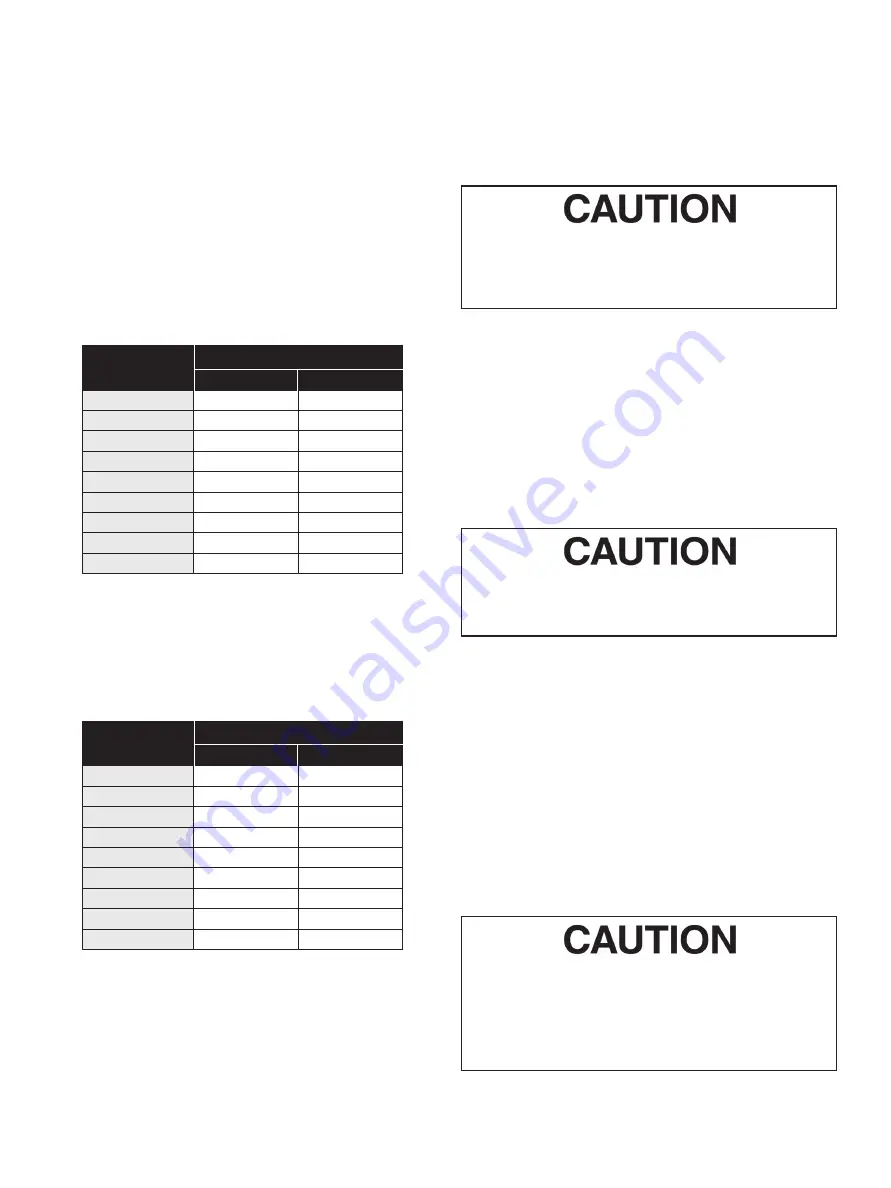
Masoneilan 35002 Series Camflex II Instruction Manual | 12
Copyright 2020 Baker Hughes Company. All rights reserved.
E.
Replace lever (34) on valve shaft (19) and tighten lever
capscrew (49).
F.
Using the lever (34) manually close the plug with sufficient
force to allow seat ring and plug to align.
G.
Using the seat ring wrench, tighten seat ring retainer to the
minimum torque value specified in Figure 12.
Note: In some cases, for the valves from 3" to 12" (DN 80
to 300) with metal seat, the alignment can be improved
by placing a piece of paper 0.10mm (0.004") thick and
approximately 6mm (1/4") wide at a point where the
leading edge and the trailing edge of the plug contacts
the seat ring and close the plug. With a slight pressure
on the lever, the paper strips should both be clamped in
place. For the valve 8" to 12" (DN 200 to 300), the piece
of paper shall be 0.20mm (0.008") thick and 12mm (1/4")
wide.
Valve Size
Minimum Torque
lb.ft
m.N
1" (DN 25)
60
81
1
1
⁄
2
" (DN 40)
95
130
2" (DN 50)
100
135
3" (DN 80)
290
395
4" (DN 100)
363
490
6" (DN 150)
825
1120
8" (DN 200)
975
1320
10" (DN 250)
1350
1830
12" (DN 300)
2250
3050
Figure 12
H.
Proceed to section on body to actuator assembly.
10.7 DVD Plate Reassembly
Using the same method and tooling as described in 8.3.2,
tighten the
Lo-dB™
plate at the indicated torque given in the
table of Figure 13.
Valve Size
Tightening Torque
lb.ft
m.N
1" (DN 25)
74
100
1
1
⁄
2
" (DN 40)
81
110
2" (DN 50)
100
135
3" (DN 80)
220
295
4" (DN 100)
363
490
6" (DN 150)
780
1050
8" (DN 200)
975
1320
10" (DN 250)
1320
1830
12" (DN 300)
2250
3050
Figure 13
11. Actuator Stem Adjustment
(Refer to Figures 16 and 17)
The following procedures must be adhered to in order to ensure
correct valve operation. Failure to do so could result in valve
damage and equipment malfunction.
Correct actuator stem adjustment is imperative for
proper valve functioning. With the actuator assem-
bled to the valve in the desired location and orienta-
tion proceed as follows:
Note: If any of the following steps were completed during
maintenance or reorientation of actuator to valve, proceed
to the next step.
A.
Remove front cover (32) and rear cover (29) by removing
the two-cover screws (30).
B.
Back off handwheel (53) so it does not interfere with the
operation of the lever (34).
C.
If applicable, back off optional limit stop (77) so it will not
interfere with the operation of the lever (34).
D.
Apply air pressure to the actuator and move lever (34) to an
intermediate position.
Do not exceed pressure listed in Figure 14 for the
actuator used. Do not use handwheel (53) to move
lever (34).
E.
Remove adjustable indicator (88) by removing the two
screws (89).
F.
Remove clevis pin clip (5), remove clevis pin (7).
G.
Relieve air pressure to the actuator to allow the clevis (35)
and lever (34) to separate.
Note: If the unit is air-to-open, separate clevis (35) and
lever (34) then loosen clevis locknut (46) and remove
clevis.
H.
Insert clevis pin (7) back in lever (34).
I.
Manually push the lever (34) so the valve is in the closed
position.
J.
Temporarily replace front cover (32) and check the location
of the clevis pin (7) in relation to the closed position indicator
mark on front cover (32).
The relationship must be as shown in Figure 18. If
it is not, the yoke must be separated from the body
and the lever (34) repositioned on the shaft. Refer to
appropriate section. Failure to comply could result in
the valve short stroking or over stroking and could
damage the valve.
Note: If the unit is air-to-open, replace clevis locknut