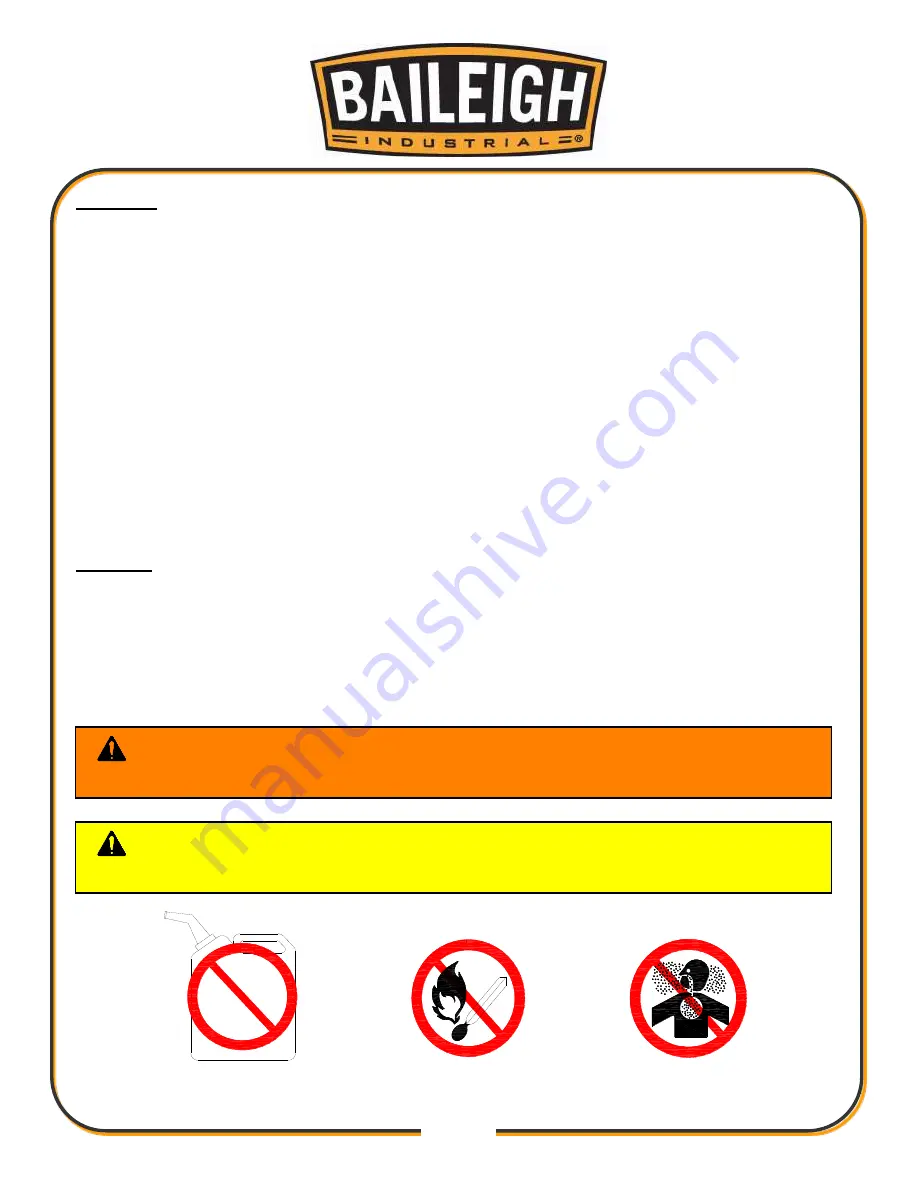
14
14
Mounting
Once you have confirmed that your machine is running properly, you may decide to mount it to a
workbench. Remove the adjustable feet and mount it through the holes in the base. The
strongest mounting option is a "Through Mount" where holes are drilled all the way through the
workbench, and hex bolts, washers, and hex nuts are used to secure the machine to the
workbench.
Another option for mounting is a "Direct Mount" where the machine is simply secured to the
workbench with a lag screw.
Whichever method you choose, it is crucial that the workbench is perfectly flat. Mounting the
lathe to a surface that is not flat may cause the lathe bed to warp. Make sure all four corners are
sitting firmly on the workbench and, if necessary, use shims to level the lathe and prior to
mounting.
Do not over tighten the mounting fasteners as this may crack the cast iron feet.
Cleaning
Your machine may be shipped with a rustproof waxy oil coating and grease on the exposed
unpainted metal surfaces. To remove this protective coating, use a degreaser or solvent
cleaner. For a more thorough cleaning, some parts will occasionally have to be removed.
DO
NOT USE
acetone or brake cleaner as they may damage painted surfaces.
Follow manufacturer’s label instructions when using any type of cleaning product. After cleaning,
wipe unpainted metal surfaces with a light coating of quality oil or grease for protection.
WARNING:
DO NOT USE gasoline or other petroleum products to clean
the machine. They have low flash points and can explode or cause fire.
CAUTION:
When using cleaning solvents work in a well ventilated area.
Many cleaning solvents are toxic if inhaled.
GAS
Содержание WL-1220VS
Страница 3: ...Wood Lathe Operation 41 PARTS DIAGRAM SHEET 1 43 PARTS DIAGRAM SHEET 2 44 Parts List 45...
Страница 20: ...17 17 ELECTRICAL DIAGRAM...
Страница 39: ...36 36 Lubrication Lubricate the locations shown A in Figure 43 with light machine oil Fig 43 A...
Страница 46: ...43 43 PARTS DIAGRAM SHEET 1...
Страница 47: ...44 44 PARTS DIAGRAM SHEET 2...
Страница 51: ...48 48 NOTES...