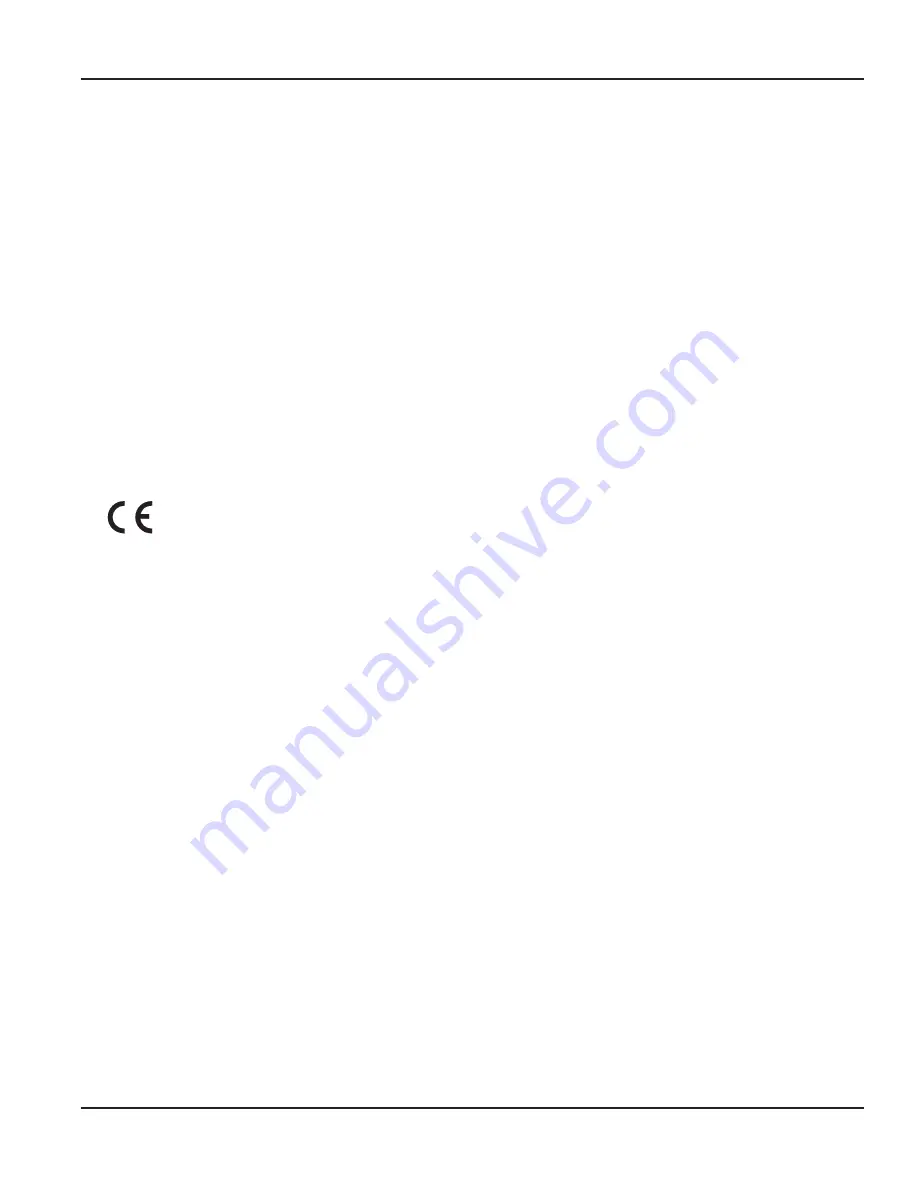
INTRODUCTION
Used in conjunction with any Badger Meter impeller flow monitor or transmitter, Badger Meter non-magnetic flow sensors
provide an accurate rate of liquid flow as well as total accumulated flow . A number of sensor models are offered, which cover
applications for a wide range of pipe sizes and pressure/temperature specifications .
The flow sensors generate a frequency which is proportional to flow rate . An internal preamplifier allows the pulse signal to
travel up to 2000 feet without further amplification . Power to operate the sensor is provided by the flow monitor . The impeller
bearing assembly, shaft and O-rings are replaceable in the field .
Badger Meter flow sensors feature a closed, six-bladed impeller design, using a proprietary, non-magnetic sensing
technology . The forward-swept impeller shape provides higher, more constant torque than four-bladed impeller designs,
and is less prone to fouling by water-borne debris . The forward-curved shape, coupled with the absence of magnetic
drag, provides improved operation and repeatability, even at lower flow rates . As the liquid flow turns the impeller, a low
impedance signal is transmitted with a frequency proportional to the flow rate .
Sensors of similar type are interchangeable, so there is no need for recalibration after servicing or replacement .
This manual provides instructions for the following insertion style flow sensors, as indicated:
220BR; 220SS; 220PV; 225BR; 226BR; 226SS
CERTIFICATION
MECHANICAL INSTALLATION
Flow measurement accuracy for all flow measuring devices is highly dependent on proper location in the piping system .
Irregular flow velocity profiles caused by valves, fittings, and pipe bends can lead to inaccurate overall flow rate indications
although local flow velocity measurement may be accurate . A sensor located where it can be affected by air bubbles, floating
debris, or sediment may not achieve full accuracy and could be damaged . Badger Meter flow sensors are designed to operate
reliably under adverse conditions . Follow these recommendations to provide maximum system accuracy:
• Choose a location along the pipe where 10 pipe diameters upstream and 5 pipe diameters downstream of the sensor
provide no flow disturbance . Pipe bends, valves, other fittings, pipe enlargements and reductions should not be present in
this length of pipe .
• The preferred location around the circumference of a horizontal pipe is on top . If trapped air or debris will interfere, then
the sensor should be located further around the pipe from the top but not more than 45 degrees from top center . The
sensor should never be located at the bottom of the pipe, as sediment may collect there . Locations off top center cause
the impeller friction to increase, which may affect performance at low flow rates . Any circumferential location is correct for
installation in vertical pipes .
• Allow an insertion depth of 1-1/2 inches (38 mm) for pipe sizes 2-1/2 inches and larger for accurate flow rate calibration .
Detailed installation instructions for various sensor mounting configurations on the following pages include methods for
providing correct insertion depth .
• Align the sensor so that the impeller rotation is parallel to flow . Alignment instructions are included on the
following pages .
Introduction
Page 3
February 2018
SEN-UM-01635-EN-11