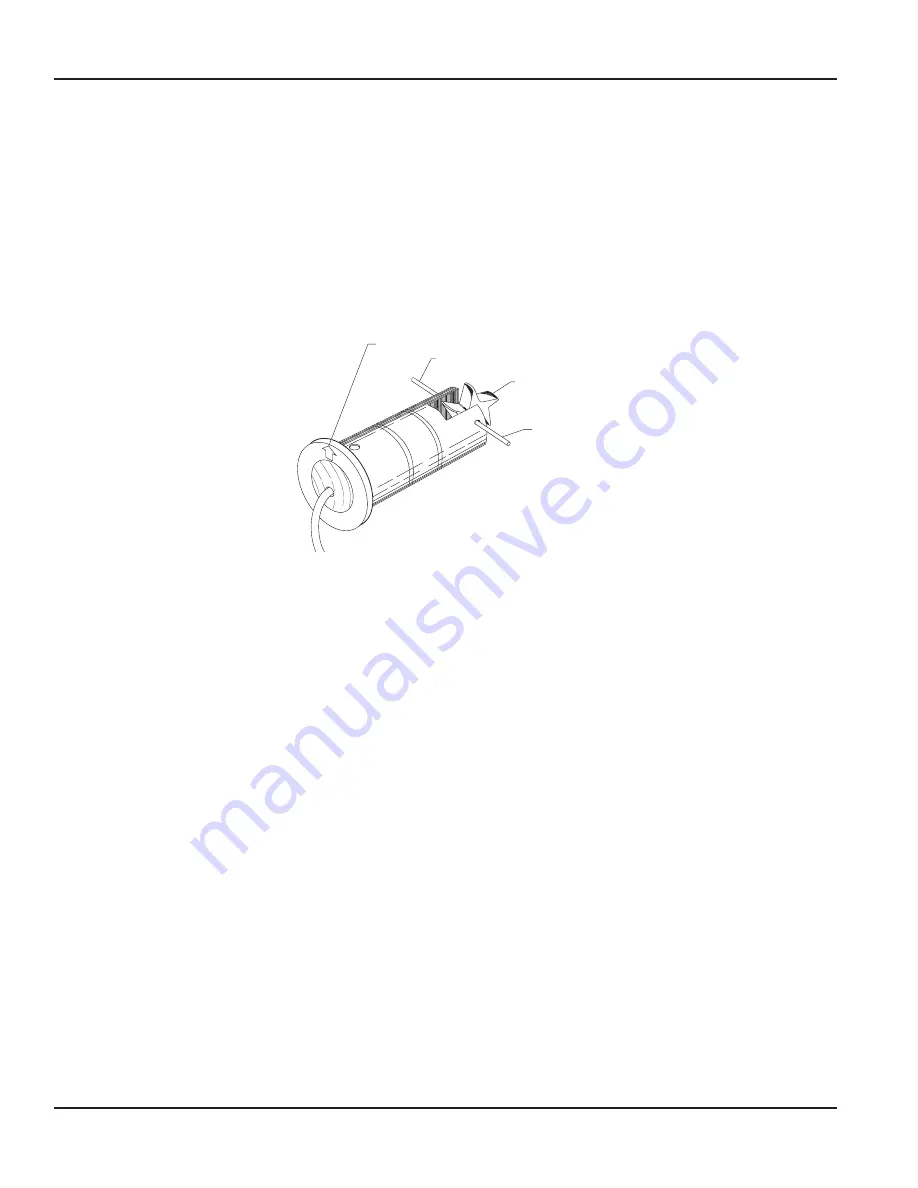
IMPELLER ASSEMBLY AND SHAFT REPLACEMENT
If you are replacing an existing Badger Meter sensor and have already calibrated your flow monitor/transmitter, no calibration
changes are necessary . For installation of a new flow monitor or for relocation of a sensor in a new pipe size, see the
calibration instructions in this manual .
1 . Depressurize the pipe from which the sensor is to be removed . If the sensor is one of the Series 225/IR225 or 226/IR226,
consult the installation section on hot tap sensors .
NEVER disturb the securing lock nuts on a pipe under pressure
without the hot tap insertion tool Model HTT installed.
2 . Remove the three lock nuts that secure the positioning collar to the threaded rods of the metal sensor .
OTEE:
N
Before removing the lock nuts, record the dimension from the top of the 2 inch NPT adapter to the bottom of the
positioning collar . This dimension will be required later to reinstall .
NOTE DIRECTION OF ARROW
USE PLIERS HERE
NOTE DIRECTION OF
IMPELLER
USE METAL PIN TO
REMOVE CERAMIC SHAFT
Figure 6: Impeller assembly and shaft replacement
3 . Remove the sensor from the hex adapter or the tee .
OTEE:
N
Note the impeller blade orientation relative to the flow arrows and the alignment hole in metal sensors beside
one of the sight holes . To maintain proper calibration, the impeller must be reinstalled in the same manner, with
the impeller blades pointing toward the small alignment hole, and into the flow direction as indicated by the
flow arrows .
4 . To remove the old impeller blade assembly, push the old shaft out of the sleeve with the new shaft (or small diameter rod)
just far enough to grab the end with a pair of pliers and pull the shaft completely out . The impeller assembly will now be
free and will drop out .
5 . Inspect the shaft and bearings for wear, and replace as necessary .
6 . See
Figure 5
. To reinstall, position the impeller in the cavity, oriented as in the
NOTE
above, so that the impeller blades
point into the flow direction and toward the alignment hole located beside one of the sight holes on the metal sensors .
7 . Carefully push the shaft through the sleeve and impeller, taking care not to damage the bearings . Make sure that the shaft
is inserted far enough so that it clears the sleeve on each side of the impeller housing .
OTEE:
N
If the shaft is not carefully installed, the bearing can be deformed preventing free rotation .
8 . Inspect the O-rings for damage and replace as necessary . Clean the O-rings and the sleeve and relubricate with silicone
grease from the packet provided or some other acceptable lubricant .
9 . Install the sensor into the 2 inch NPT adapter or tee so that the alignment hole is facing upstream and flow arrows point
in the direction of the actual flow . Since the positioning collar was not loosened during this operation, the studs should all
line up perfectly when the sight holes are parallel to pipe . If this has been accidentally loosened, see
"Electrical Installation
Safety" on page 11
.
10 . Install and tighten the nuts .
11 . For metal sensors, double check that the distance from the top of the 2 inch NPT adapter to the bottom of the positioning
collar equals the dimension as measured in
Step 2
, and holes in sleeve sight exactly down the pipe, the arrows point
in the direction of flow, and alignment holes located beside one sight hole are pointing towards the source . If not, see
"Mechanical Installation" on page 3
.
This completes the replacement procedure . The system can now be repressurized and tested .
Impeller Assembly and Shaft Replacement
Page 16
February 2018
SEN-UM-01635-EN-11