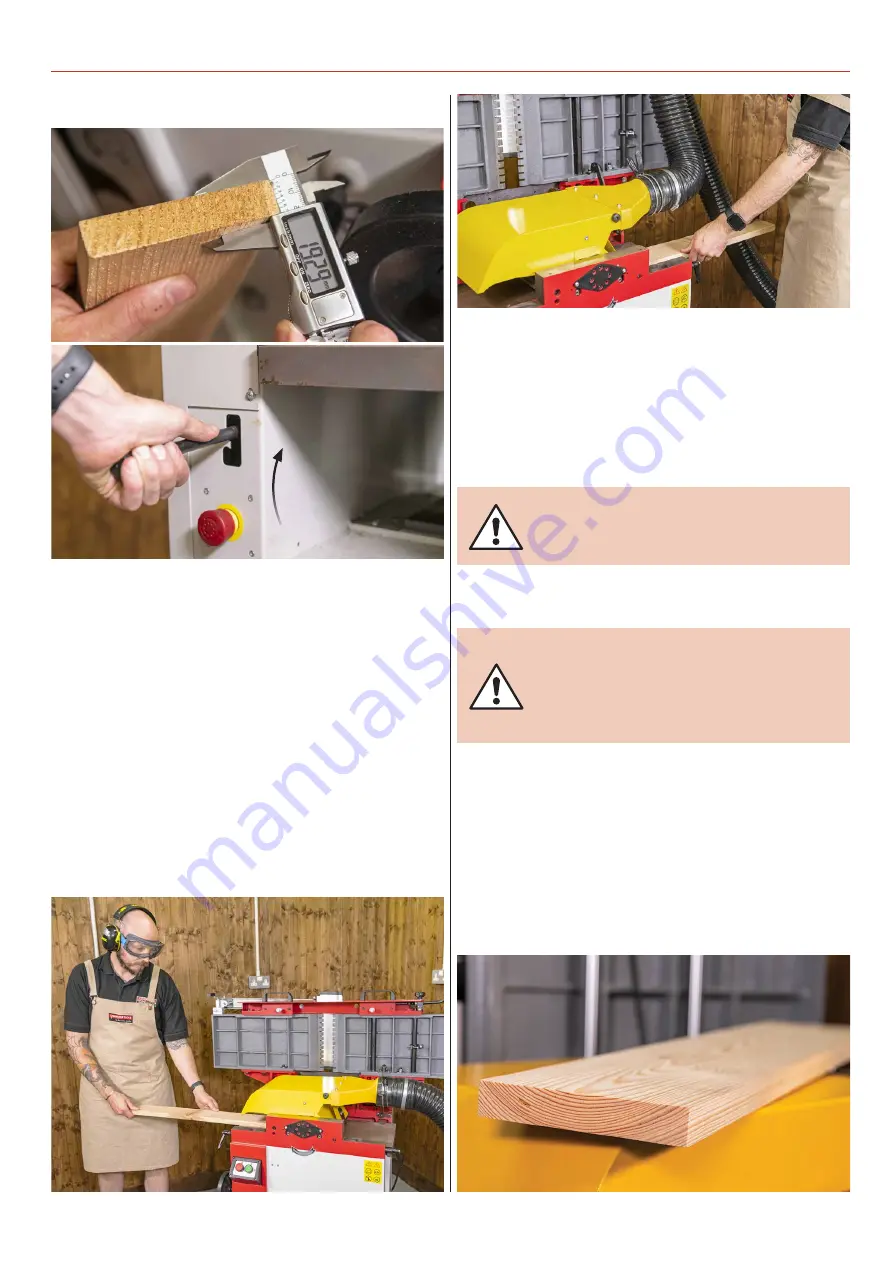
GENERAL USE / OPERATION
13
• Engage the feed rollers (push down to the right &
allow to move upwards), see fig 49.
• Press the green start button and allow the cutter
block to run up to full speed.
• Place the material so that the already machined
face is down, i.e. in contact with the thicknessing
bed, and you are not, if possible, cutting against the
grain.
• Push the material firmly into the machine until
the feed roller ‘picks up’ the material and moves it
through the machine, see fig 50.
Fig 48-49
Fig 50-51
• Move around to the ‘back’ of the machine and
support the timber to prevent it falling to the floor.
When the machining pass is complete measure
the dimension you have just cut and calculate how
much more material you have to remove to reach
the required size, see fig 51.
• Raise the thicknessing bed for the new cut.
NOTE. ONE COMPLETE TURN OF THE
CRANK HANDLE RAISES (OR LOWERS)
THE BED APPROXIMATELY 2MM.
IMPORTANT - WIDER OR HARDER BOARDS
WILL REQUIRE MORE LIGHTER PASSES TO
ACHIEVE THE REQUIRED DIMENSION
RATHER THAN FEWER HEAVY PASSES TO
ENSURE THAT THE MACHINE IS NOT
OVERLOADED!
Repeat the process until you reach your required
material thickness.
• REMEMBER you may want to do a ‘clean up’ pass
on your first surface as well (to remove possible
imperfections, e.g. planing ripples, small ‘dips’ that
didn’t clean perfectly during the first surfacing
phase, etc).
• You now should have clean, dimensioned, square
timber, see fig 52.
Fig 52
Содержание 108512
Страница 1: ...AW2260S Planer Thicknesser Code 108512 Original Instructions AT 22 09 2022 BOOK VERSION 01 ...
Страница 3: ...WHAT S IN THE BOX 3 A B C E I J K F H G D D L M ...
Страница 17: ...EXPLODED DIAGRAM PARTS LIST 17 Continues over Model C2 260S ...
Страница 19: ...EXPLODED DIAGRAM PARTS LIST 19 Continues over Model C2 260S ...
Страница 21: ...EXPLODED DIAGRAM PARTS LIST 21 Continues over Model C2 260S ...
Страница 24: ...WIRING DIAGRAM 24 ...
Страница 27: ...27 ...