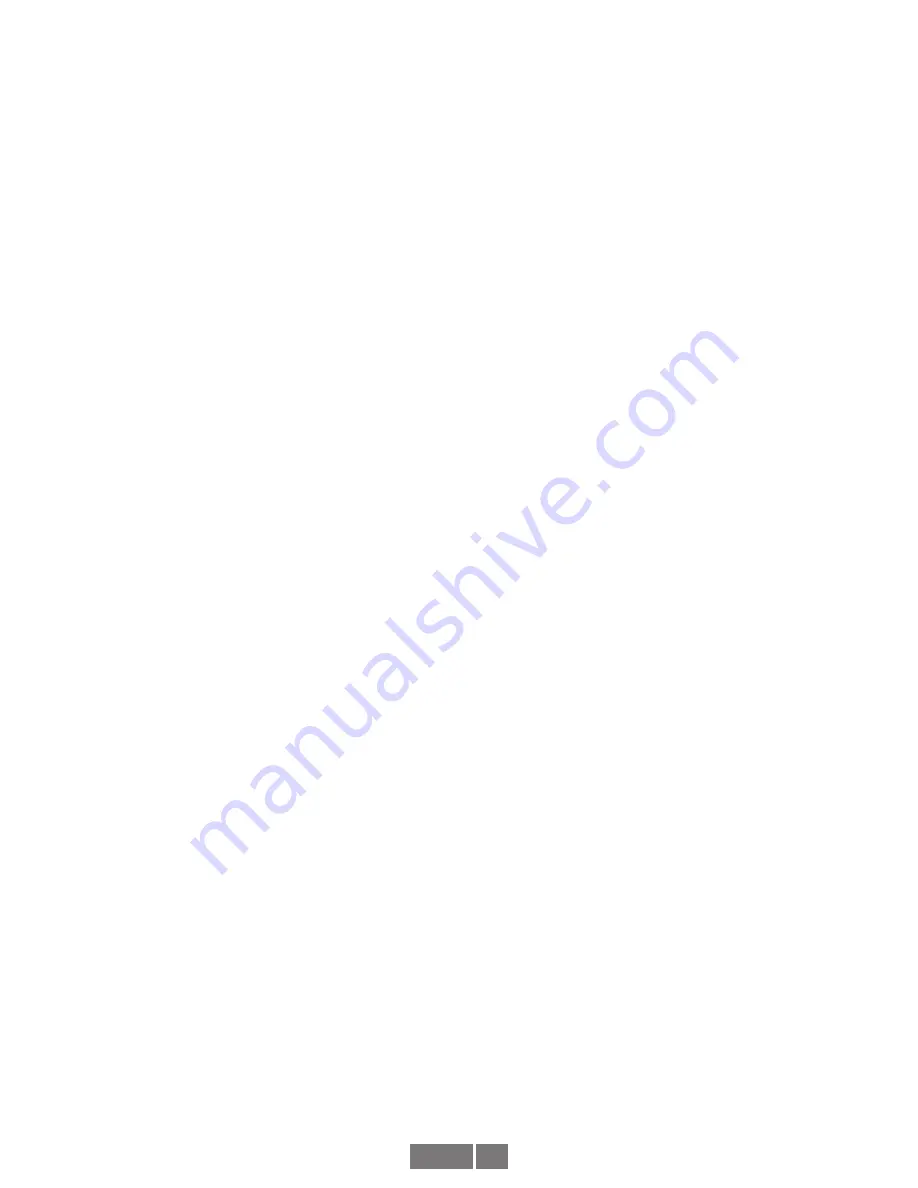
AV6A
2
The encoder must be driven by a positive drive rather than a friction
drive. The following means of coupling are acceptable when properly
installed: Direct Coupling.
With a direct drive, use a flexible disc coupling and align the shafts
as accurately as possible. For motors with a pre-aligned flange, it is
also acceptable to use a “spider” or “jaw” coupling type. If a rubber
slinger disc is used, position it on the shaft so it will rotate freely.
The AV6A performance and life will be directly affected by the
installation. Following this sequence of steps is recommended.
1) Clean and inspect motor/driver shaft. Do not use force to
assemble coupling onto motor/driver shaft. Any mounting
bracket must be secured to a flat, rigid, vibration free steel or
aluminum base which can be machined to accept the
mounting hardware.
2a) For Foot Mounting: Temporarily mount the AV6A to the foot
bracket, install the coupling to the AV6A and driver, and verify
that the location is suitable for installation.
2b) For Flange Mounting: Temporarily mount the AV6A to the flange
bracket, install the coupling to the AV6A and driver, and verify
that the location is suitable for installation.
3a) If the encoder, bracket and coupling are suited to the
area, check motor/encoder shaft alignment with a straight
edge from multiple positions around the shaft circumference to
verify that it meets specifications.
3b) If the encoder, bracket and coupling are suited to the
area, check motor/encoder shaft alignment with a straight
edge from multiple positions around the shaft circumference to
verify that it meets specifications.
4a) While maintaining alignment, precisely mark the position of the
foot bracket on its mounting base.
4b) If the shaft angular alignment is not acceptable, loosen the
mounting screws to the flange and apply thin metal shims to
the face of the encoder and retest the angular alignment until
acceptable.
5a) Remove the AV6A. Transfer punch or layout the mounting hole
pattern as indicated on outline drawing.
5b) If the shafts are parallel, but misaligned (parallel misalignment),
the flange will need to be re-machined. Shimming will NOT
correct parallel misalignment, and will lead to premature
bearing wear or coupling breakage. (After correcting alignment,
proceed to step 8)
6a) Machine through holes or tap holes
in center of base slots to give some degree of freedom in final
alignment.
7a) Reinstall the AV6A with the flexible coupling loosely in place,
and tighten down all mounting hardware. Check
motor/encoder shaft alignment with a straight edge from
multiple positions around the shaft circumference to verify that
it meets specifications. Use thread locker on cap
screws which mount AV6A to foot bracket. Proceed to step 8.
8) Ensure any flat or keyway on the motor and encoder shaft are
aligned with the set screw holes of the flexible coupling. Apply
thread locker to coupling set screws and tighten per
manufacturer’s recommendations.
9) Recheck alignment and tighten all hardware after first several
hours of operation.
ENVIRONMENTAL CONSIDERATIONS
Follow these steps to reduce potential problems:
1) Always mount connection points, conduit couplings, junction
boxes, etc., lower than actual encoder.
2) For washdown areas, shroud or otherwise cover the encoder to
prevent direct water spray. Do not attach the shroud directly to
the encoder.
REPAIRS
REMOVAL INSTRUCTIONS:
1. Unfasten coupling.
2. Remove the screws which secure the encoder to the flange or
foot mount. Note that the foot mount can remain in place.
3. Slide the encoder free of the mount.
REPLACING PARTS
The AV6A has no user-replaceable parts.
CAUTION
Do not attempt to remove, service, or adjust any of the
internal components of the AV6A.